Furnaces used for melting materials, particularly metals, come in various types, each designed for specific applications and materials. The primary types include induction furnaces, electric-resistance furnaces, fuel-fired furnaces, cupola furnaces, electric arc furnaces, and crucible furnaces. Induction furnaces are highly efficient and clean, ideal for melting and alloying metals with minimal losses, though they offer limited refining capabilities. Electric-resistance and fuel-fired furnaces are commonly used for melting-point determinations, while cupola furnaces, electric arc furnaces, and crucible furnaces cater to different industrial needs, such as large-scale metal melting or specialized alloy production. Each furnace type has unique features, such as size, capacity, and energy efficiency, making them suitable for specific tasks in metallurgy and material processing.
Key Points Explained:
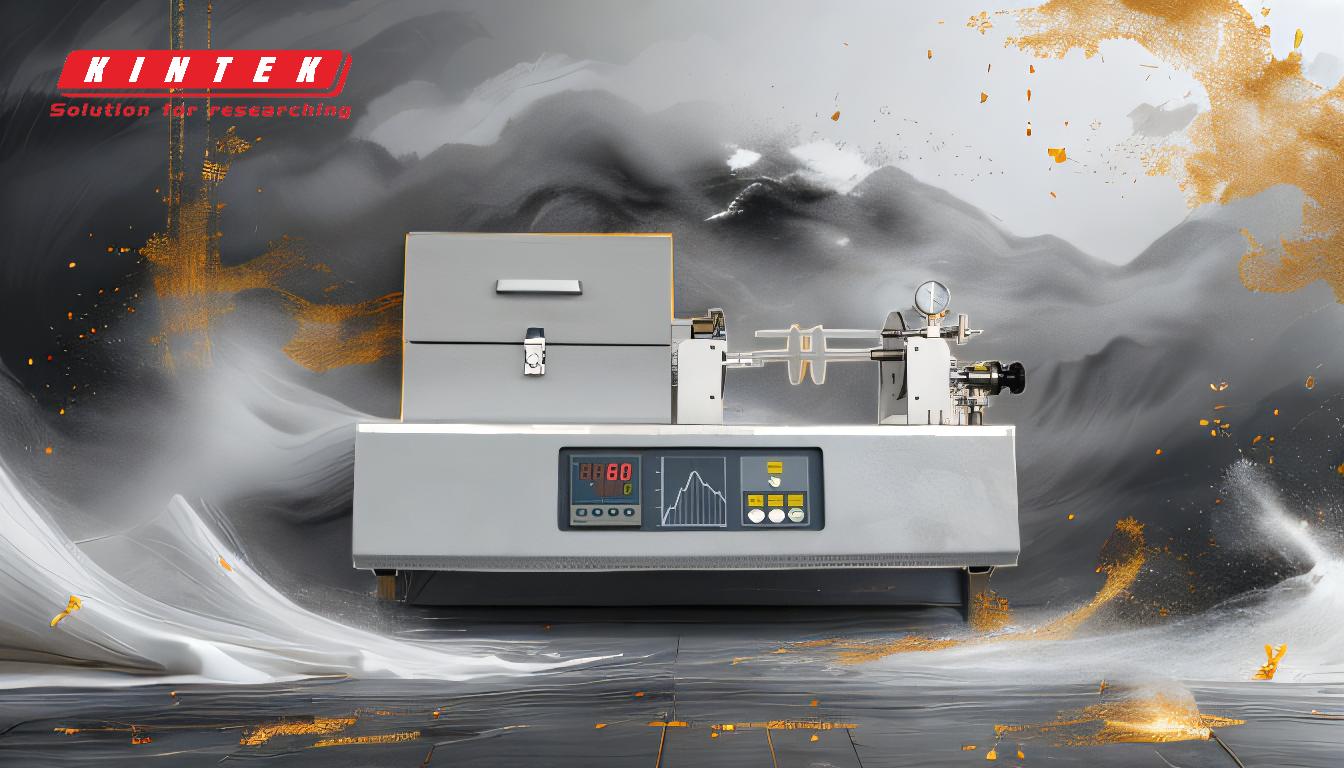
-
Induction Furnaces:
- Coreless, Channel, and Crucible Types: Induction furnaces are categorized into coreless, channel, and crucible types, each differing in size, capacity, frequency, and design. Coreless furnaces are versatile and widely used for melting metals, while channel furnaces are ideal for continuous melting processes. Crucible furnaces are smaller and suitable for specialized applications.
- Main Frequency and Medium Frequency: Induction furnaces are further divided into main frequency and medium frequency types. Main frequency furnaces operate at lower frequencies and are suitable for larger-scale melting, while medium frequency furnaces are more energy-efficient and used for smaller batches.
- Advantages: Induction furnaces are clean, energy-efficient, and offer precise control over the melting process. They are ideal for melting and alloying a wide range of metals with minimal melt losses. However, they provide limited refining capabilities.
-
Electric-Resistance Furnaces:
- Carbon Resistors: These furnaces use carbon-based materials like graphite tubes, crushed carbon, or Kryptol as resistors. They are commonly used for melting-point determinations and are suitable for high-temperature applications.
- Metal Resistors: Furnaces with metal resistors, such as iridium tubes or wires, and tungsten or molybdenum wires or tubes, are used for precise temperature control and high-temperature melting processes.
-
Fuel-Fired Furnaces:
- These furnaces rely on combustible fuels like gas or oil to generate heat. They are often used in industrial settings for melting metals and are suitable for large-scale operations. Fuel-fired furnaces are cost-effective but may lack the precision and energy efficiency of electric furnaces.
-
Cupola Furnaces:
- Cupola furnaces are primarily used for melting iron and producing cast iron. They are vertical, cylindrical furnaces that use coke as a fuel source. Cupola furnaces are known for their high melting capacity and are commonly used in foundries.
-
Electric Arc Furnaces:
- These furnaces use an electric arc to generate heat for melting metals. They are highly efficient and capable of melting large quantities of metal quickly. Electric arc furnaces are commonly used in steel production and recycling industries.
-
Crucible Furnaces:
- Crucible furnaces are small, portable furnaces used for melting small quantities of metal. They are ideal for specialized applications, such as jewelry making or laboratory experiments. Crucible furnaces are simple in design and easy to operate.
-
Sintering Furnaces:
- Vacuum Sintering Furnaces: Used for sintering high chromium cast steel rolls and other materials, these furnaces feature precise temperature control and high uniformity.
- Tunnel Type Enamel Sintering Furnaces: Energy-efficient continuous operation furnaces used in the enamel industry for sintering large products like decorative panels and bathtubs.
- Alumina Sintering Furnaces: Designed for alumina sintering with fully automated temperature control.
- Cart Type Drill Sintering Furnaces: Widely used in the alloy sintering industry for mining and petroleum alloy drill sintering, with fully automatic execution of the sintering process curve.
Each type of furnace has its unique advantages and applications, making them suitable for different industrial and laboratory needs. The choice of furnace depends on factors such as the material to be melted, the scale of operation, and the desired level of control and efficiency.
Summary Table:
Furnace Type | Key Features | Applications |
---|---|---|
Induction Furnaces | Clean, energy-efficient, precise control; limited refining capabilities | Melting and alloying metals; coreless, channel, and crucible types |
Electric-Resistance | Carbon or metal resistors; high-temperature capabilities | Melting-point determinations; precise temperature control |
Fuel-Fired Furnaces | Combustible fuels (gas/oil); cost-effective; less precise | Large-scale metal melting; industrial settings |
Cupola Furnaces | High melting capacity; uses coke as fuel | Melting iron; cast iron production |
Electric Arc Furnaces | Electric arc heat; highly efficient; fast melting | Steel production; metal recycling |
Crucible Furnaces | Small, portable; simple design | Jewelry making; laboratory experiments |
Sintering Furnaces | Precise temperature control; automated processes | Sintering high chromium cast steel rolls, alumina, and alloy drill sintering |
Need help choosing the right furnace for your application? Contact our experts today!