High temperature furnaces are specialized equipment designed to operate at extremely high temperatures, typically ranging from 1400°C to 1800°C. They are widely used in various applications, including material testing, sintering, glass melting, and powder metallurgy. The two primary types of high temperature furnaces are tube furnaces and box furnaces, each with unique features tailored to specific industrial or laboratory needs. Tube furnaces are characterized by their cylindrical chambers and rapid heating capabilities, while box furnaces are categorized based on their temperature ranges and heating elements. These furnaces play a critical role in quality control laboratories and industrial processes, ensuring materials meet stringent thermal and performance standards.
Key Points Explained:
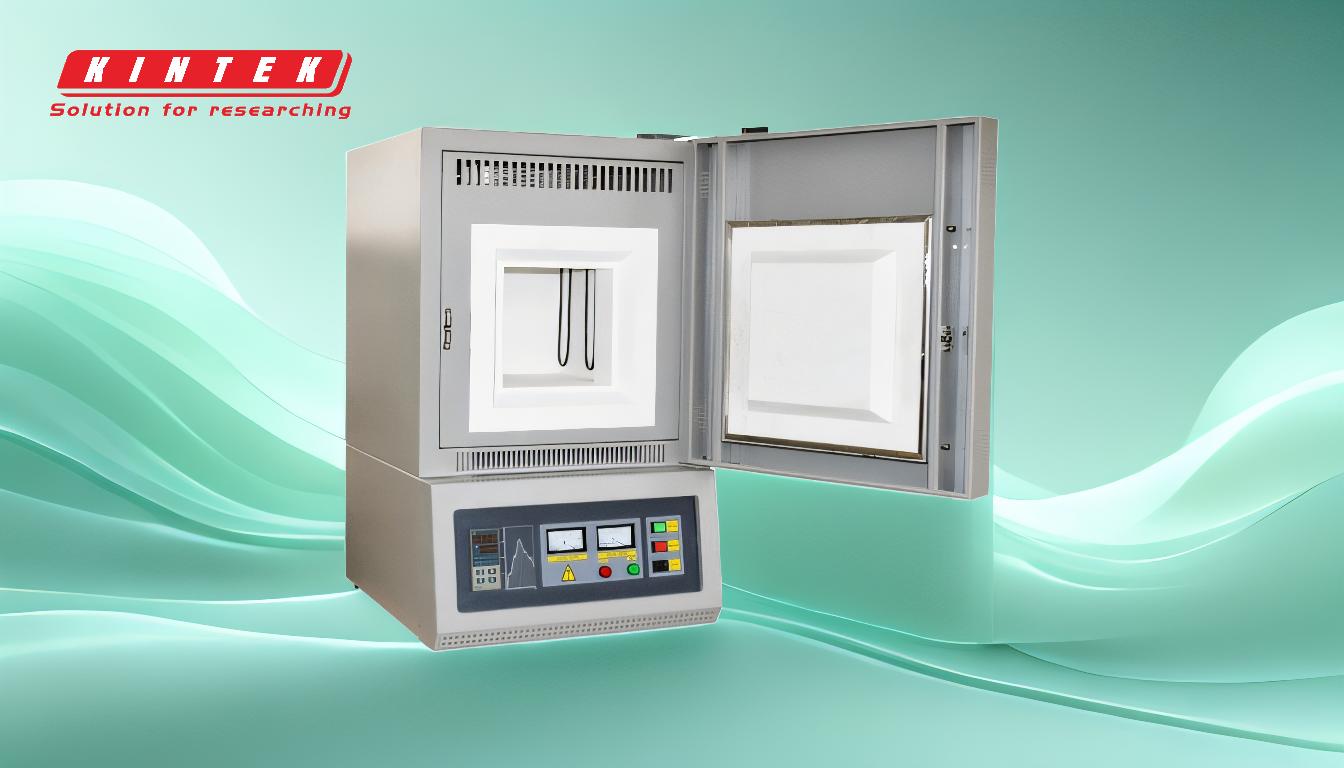
-
Types of High Temperature Furnaces:
- High temperature furnaces are primarily categorized into two types: tube furnaces and box furnaces.
- Tube furnaces feature cylindrical chambers surrounded by heating elements, enabling rapid heat-up, recovery, and cool-down. They are versatile and can be used horizontally or vertically, making them suitable for a wide range of applications.
- Box furnaces are classified based on their temperature ranges, such as below 1200°C, 1400°C, 1600°C, 1700°C, and 1800°C. The specific temperature range depends on the heating elements and application requirements.
-
Temperature Capabilities:
- High temperature furnaces can achieve temperatures between 1400°C and 1800°C, making them suitable for extreme thermal testing and industrial processes.
- The ability to reach such high temperatures is essential for applications like sintering, glass melting, and testing ceramics under extreme conditions.
-
Applications of High Temperature Furnaces:
- In quality control laboratories, these furnaces are used for thermal testing to evaluate the thermal stability, durability, and performance of materials.
- Industrial applications include sintering of high-temperature materials, glass melting, fusion and firing processes, and powder metallurgy.
-
Features of Tube Furnaces:
- Tube furnaces are designed with features such as independent digital control modules, double-shell construction, variable density insulation, and split-hinge designs.
- These features enhance their functionality, making them adaptable to various experimental and industrial setups.
-
Classification of Box Furnaces:
- Box furnaces are categorized based on their maximum operating temperatures, which are determined by the type of heating elements used.
- This classification ensures that the furnace selected is appropriate for the specific temperature requirements of the application.
-
General Furnace Types:
- Furnaces are broadly divided into three categories: household, industrial, and laboratory furnaces.
- High temperature furnaces fall under the industrial and laboratory categories, where precision and high thermal performance are critical.
By understanding these key points, purchasers of high temperature furnaces can make informed decisions based on the specific requirements of their applications, ensuring optimal performance and efficiency.
Summary Table:
Type | Key Features | Temperature Range | Applications |
---|---|---|---|
Tube Furnaces | Cylindrical chambers, rapid heating, versatile (horizontal/vertical use) | Up to 1800°C | Material testing, sintering, glass melting, powder metallurgy |
Box Furnaces | Categorized by temperature range, heating elements determine max temperature | 1200°C to 1800°C | Thermal testing, sintering, fusion, firing processes, high-temperature material processing |
Need help choosing the right high temperature furnace for your application? Contact our experts today!