Induction furnaces are widely used in various industries for melting metals and alloys due to their efficiency, precise temperature control, and clean operation. They are categorized based on their design, power supply, and application. The main types include coreless induction furnaces, channel induction furnaces, and vacuum induction furnaces. Each type has unique features and is suited for specific industrial needs, such as melting, holding, or refining metals. Understanding these types helps in selecting the right furnace for a particular application.
Key Points Explained:
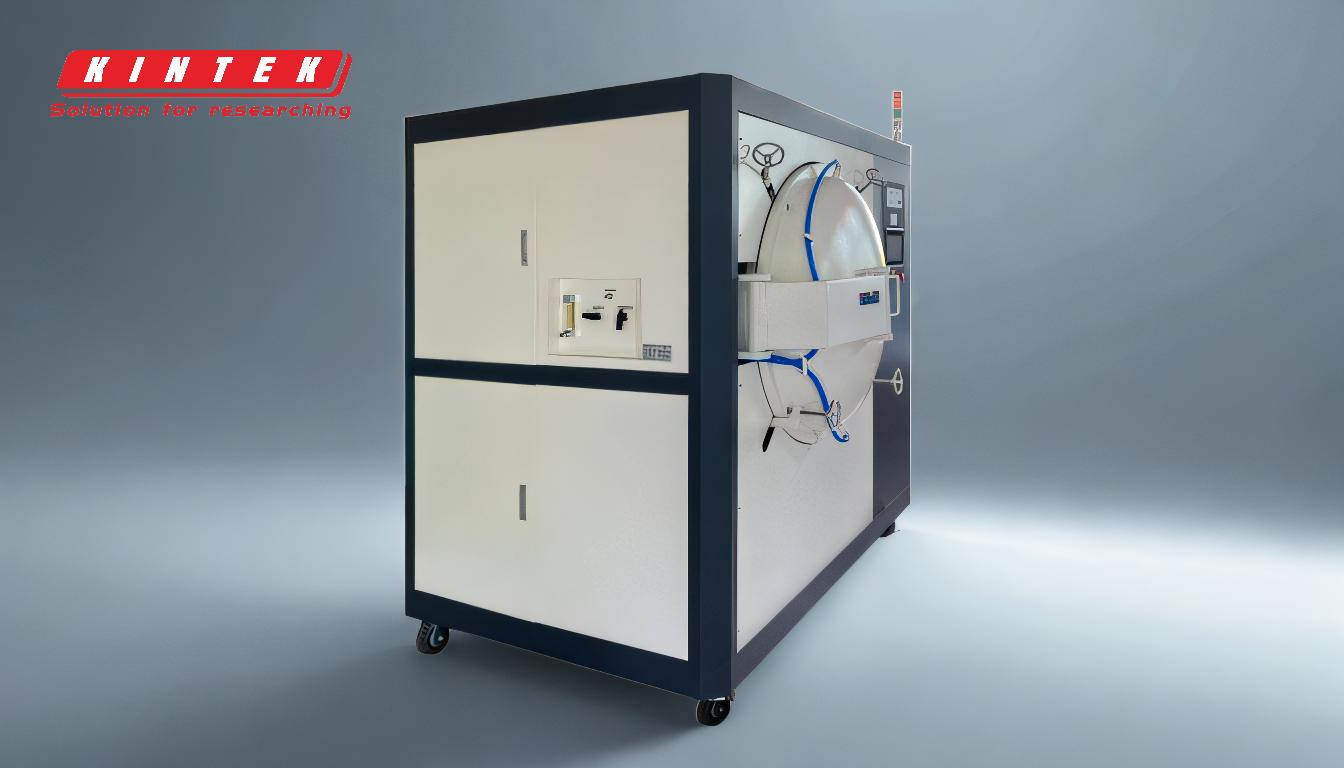
-
Coreless Induction Furnaces:
- Design: These furnaces have a cylindrical coil that generates an electromagnetic field, inducing eddy currents in the metal charge, which heats and melts it.
- Applications: Ideal for melting a wide range of metals, including steel, iron, copper, and aluminum.
- Advantages: High efficiency, flexibility in metal types, and easy maintenance.
- Limitations: Requires a molten metal starter charge for initial operation.
-
Channel Induction Furnaces:
- Design: These furnaces feature a looped channel filled with molten metal, which acts as a secondary winding. The primary coil induces currents in the channel, maintaining the metal in a molten state.
- Applications: Best suited for holding and superheating molten metals, often used in foundries and die-casting operations.
- Advantages: Energy-efficient for holding molten metal, long lifespan, and low operating costs.
- Limitations: Limited to holding and superheating; not ideal for melting large quantities of solid metal.
-
Vacuum Induction Furnaces:
- Design: These furnaces operate under a vacuum or controlled atmosphere, preventing oxidation and contamination of the metal.
- Applications: Used for melting and refining high-purity metals and alloys, such as superalloys, titanium, and specialty steels.
- Advantages: Produces high-purity metals, reduces oxidation, and allows precise control over alloy composition.
- Limitations: High initial cost and complex operation.
-
Comparison with Sintering Furnaces:
- Sintering furnaces, unlike induction furnaces, are used for compacting and forming materials like ceramics and metals by applying heat without melting. They are categorized by size and temperature range, making them suitable for specific heat treatments like tempering or annealing.
-
Selection Criteria:
- Metal Type: Coreless furnaces are versatile, while channel furnaces are better for holding molten metal. Vacuum furnaces are ideal for high-purity applications.
- Production Scale: Coreless furnaces are suitable for medium to large-scale production, whereas channel furnaces are better for continuous operations.
- Budget and Maintenance: Coreless furnaces are cost-effective and easy to maintain, while vacuum furnaces require higher investment and expertise.
By understanding the different types of induction furnaces and their applications, purchasers can make informed decisions based on their specific needs, such as the type of metal, production scale, and budget constraints.
Summary Table:
Type | Design | Applications | Advantages | Limitations |
---|---|---|---|---|
Coreless Induction | Cylindrical coil generating electromagnetic field to melt metal | Melting steel, iron, copper, aluminum | High efficiency, flexible metal types, easy maintenance | Requires molten metal starter charge |
Channel Induction | Looped channel with molten metal acting as a secondary winding | Holding and superheating molten metals (foundries, die-casting) | Energy-efficient, long lifespan, low operating costs | Limited to holding; not for melting large solid quantities |
Vacuum Induction | Operates under vacuum/controlled atmosphere to prevent oxidation | Melting high-purity metals (superalloys, titanium, specialty steels) | High-purity metals, reduced oxidation, precise alloy control | High initial cost, complex operation |
Need help choosing the right induction furnace for your application? Contact our experts today!