Induction heating is a highly efficient and precise method of heating conductive materials by generating heat directly within the material through induced eddy currents. Unlike traditional heating methods that rely on external heat sources, induction heating uses electromagnetic fields to create heat internally, allowing for better control and targeted heating. The two main types of induction furnaces are coreless and channel-type, each suited for specific applications such as melting and alloying metals. Coreless furnaces use a water-cooled solenoid coil to heat the metal in a crucible, while channel-type furnaces utilize a loop of molten metal as a secondary winding around an iron core. This method offers advantages such as minimal melt losses and the ability to heat specific depths based on the frequency of the current.
Key Points Explained:
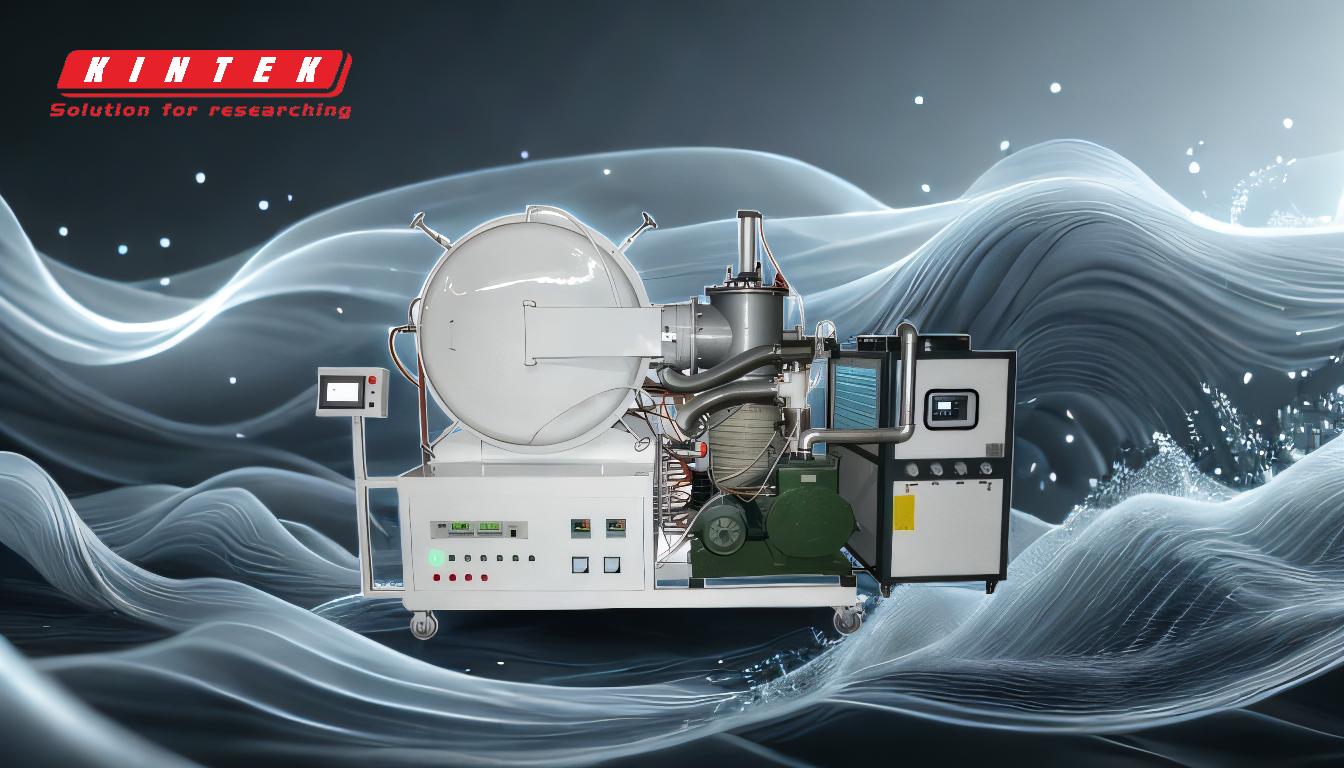
-
Coreless Induction Furnaces:
- Design: In coreless induction furnaces, the metal is placed in a crucible surrounded by a water-cooled alternating current (AC) solenoid coil. The coil generates a magnetic field that induces eddy currents within the metal, causing it to heat up.
- Applications: These furnaces are commonly used for melting and alloying a wide variety of metals. They are particularly useful for processes that require rapid heating and precise temperature control.
- Advantages: Coreless furnaces are versatile, easy to operate, and can handle a wide range of metal types and sizes. They also offer minimal melt losses, making them efficient for high-purity applications.
-
Channel-Type Induction Furnaces:
- Design: Channel-type furnaces feature a loop of molten metal that acts as a single-turn secondary winding around an iron core. The primary winding is connected to an AC power source, which induces a current in the molten metal loop, generating heat.
- Applications: These furnaces are ideal for continuous melting processes and are often used in foundries for casting applications. They are also suitable for holding and superheating molten metal.
- Advantages: Channel-type furnaces are energy-efficient and provide consistent heating. They are particularly effective for processes that require a steady supply of molten metal over extended periods.
-
Mechanism of Induction Heating:
- Eddy Currents: Induction heating works by inducing eddy currents within the conductive material. These currents flow in closed loops within the material, generating heat due to the material's electrical resistance.
- Heat Generation: The heat is generated directly within the material's surface, allowing for precise control over the heating process. The depth of heating can be adjusted by varying the frequency of the AC current, with higher frequencies resulting in shallower heating depths.
- Thermal Conduction: Once heat is generated at the surface, it transfers through the material via thermal conduction. This method ensures uniform heating and minimizes the risk of overheating or thermal stress.
-
Comparison with Traditional Heating Methods:
- Direct vs. Indirect Heating: Traditional heating methods, such as gas furnaces and electric furnaces, rely on external heat sources that transfer heat to the material through convection and radiation. In contrast, induction heating generates heat directly within the material, eliminating the need for direct contact with a flame or heating element.
- Precision and Control: Induction heating offers superior precision and control compared to traditional methods. The ability to target specific areas and adjust heating depths makes it ideal for applications requiring localized heating or precise temperature profiles.
- Efficiency: Induction heating is generally more energy-efficient than traditional methods, as it minimizes heat loss and reduces the time required to reach the desired temperature.
-
Applications of Induction Heating:
- Metal Melting and Alloying: Induction heating is widely used in metalworking industries for melting and alloying metals. The ability to achieve high temperatures quickly and efficiently makes it suitable for producing high-quality alloys with minimal impurities.
- Heat Treatment: Induction heating is also used for heat treatment processes such as hardening, tempering, and annealing. The precise control over heating and cooling rates allows for the production of materials with specific mechanical properties.
- Brazing and Soldering: Induction heating is commonly used in brazing and soldering applications, where it provides fast, localized heating without affecting the surrounding areas. This is particularly useful in the assembly of electronic components and precision engineering.
-
Advantages of Induction Heating:
- Energy Efficiency: Induction heating is highly energy-efficient, as it generates heat directly within the material, reducing energy losses associated with traditional heating methods.
- Speed: The rapid heating capabilities of induction heating make it ideal for processes that require quick turnaround times, such as metal melting and heat treatment.
- Precision: The ability to control heating depth and target specific areas allows for precise temperature control, reducing the risk of overheating or thermal damage.
- Cleanliness: Induction heating is a clean process that does not produce flames, smoke, or other byproducts, making it environmentally friendly and suitable for use in controlled environments.
In summary, induction heating is a versatile and efficient method of heating conductive materials, with coreless and channel-type furnaces being the primary types used in industrial applications. The ability to generate heat directly within the material, combined with precise control over the heating process, makes induction heating a preferred choice for a wide range of applications, from metal melting to heat treatment and brazing.
Summary Table:
Aspect | Coreless Induction Furnaces | Channel-Type Induction Furnaces |
---|---|---|
Design | Metal in a crucible surrounded by a water-cooled AC solenoid coil. | Loop of molten metal as a secondary winding around an iron core. |
Applications | Melting and alloying metals; rapid heating and precise temperature control. | Continuous melting; foundry casting; holding and superheating molten metal. |
Advantages | Versatile, easy to operate, minimal melt losses, handles various metals. | Energy-efficient, consistent heating, ideal for steady molten metal supply. |
Heating Mechanism | Eddy currents generated within the metal via electromagnetic fields. | Eddy currents induced in molten metal loop; heat generated internally. |
Key Benefits | Precise control, energy efficiency, rapid heating, and minimal thermal stress. | Consistent heating, reduced energy loss, and suitability for continuous processes. |
Discover how induction heating can revolutionize your processes—contact our experts today for more details!