Plasma sources are essential in various industrial and scientific applications, ranging from material processing to semiconductor manufacturing. They are used for processes like etching, deposition, and surface modification. However, traditional plasma sources often have limitations in terms of versatility and scalability. This answer explores the different types of plasma sources, their characteristics, and their applications, providing a comprehensive understanding of their functionalities and limitations.
Key Points Explained:
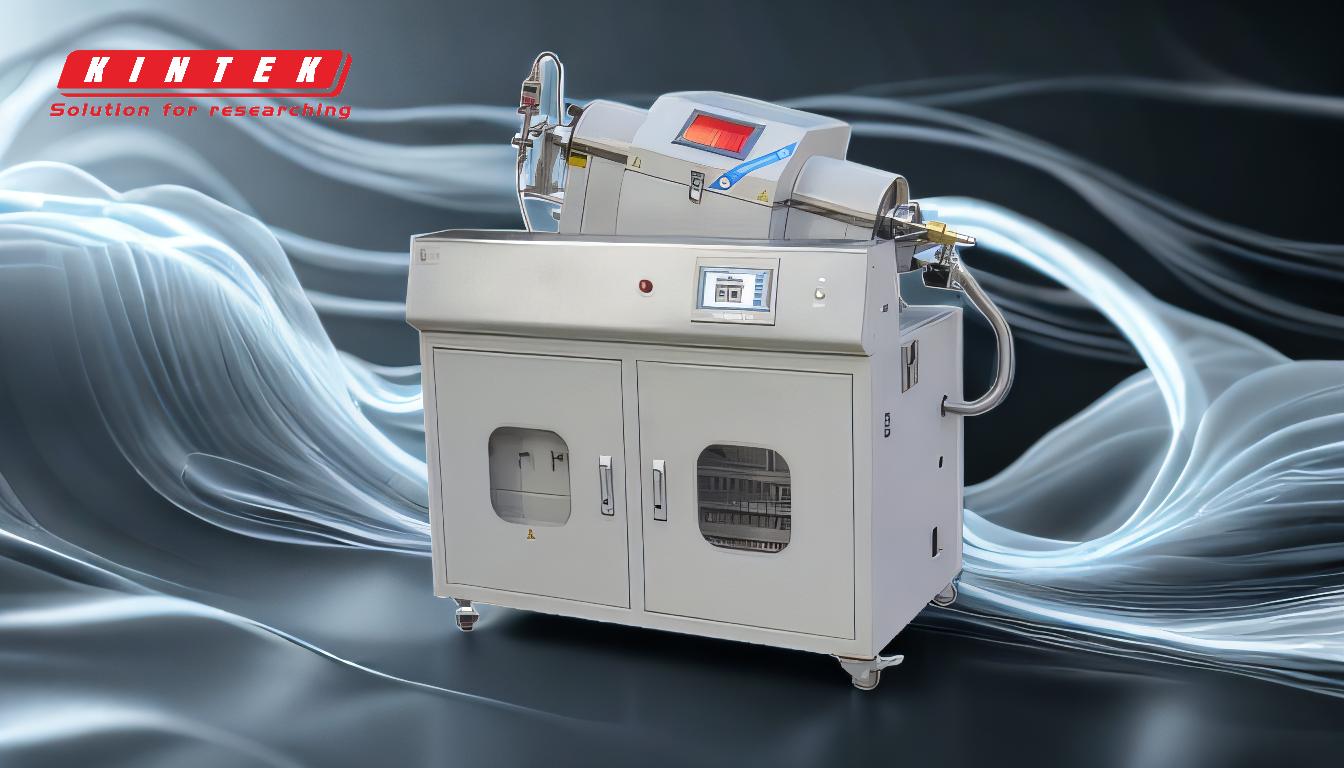
-
Overview of Plasma Sources:
- Plasma sources generate ionized gas, which consists of free electrons, ions, and neutral particles. This ionized gas is used in various applications due to its reactive properties.
- The primary types of plasma sources include:
- Capacitively Coupled Plasmas (CCP): These use radio frequency (RF) electric fields to generate plasma. They are commonly used in etching and deposition processes.
- Inductively Coupled Plasmas (ICP): These use magnetic fields to induce plasma, offering higher density and better control over ion energy. They are often used in more demanding applications like semiconductor manufacturing.
- Microwave Plasmas: These use microwave energy to generate plasma, providing high energy density and are used in applications like diamond film deposition.
- Direct Current (DC) Plasmas: These use a direct current to generate plasma and are typically used in simpler applications like surface cleaning.
-
Capacitively Coupled Plasmas (CCP):
- Operation: CCPs use RF electric fields between two electrodes to ionize the gas. The plasma is generated in the gap between the electrodes.
- Applications: Commonly used in etching processes in semiconductor manufacturing. They are also used in thin-film deposition and surface modification.
- Advantages: Simple design, relatively low cost, and good control over ion energy.
- Limitations: Limited plasma density and scalability, making them less suitable for large-scale or high-throughput processes.
-
Inductively Coupled Plasmas (ICP):
- Operation: ICPs use an inductive coil to generate a magnetic field, which induces an electric field to ionize the gas. The plasma is generated outside the coil, allowing for higher density.
- Applications: Used in advanced semiconductor processing, including high-aspect-ratio etching and ion-assisted deposition.
- Advantages: Higher plasma density, better control over ion energy, and scalability for larger substrates.
- Limitations: More complex design and higher cost compared to CCPs.
-
Microwave Plasmas:
- Operation: Microwave plasmas use microwave energy to ionize the gas. The energy is typically delivered through a waveguide or antenna.
- Applications: Used in specialized applications like diamond film deposition, surface hardening, and plasma polymerization.
- Advantages: High energy density, ability to generate plasma at low pressures, and suitability for high-temperature processes.
- Limitations: Requires precise control of microwave energy and is less common in mainstream industrial applications.
-
Direct Current (DC) Plasmas:
- Operation: DC plasmas use a direct current between two electrodes to ionize the gas. The plasma is generated in the gap between the electrodes.
- Applications: Used in simpler applications like surface cleaning, sputtering, and some types of deposition.
- Advantages: Simple and cost-effective, easy to operate.
- Limitations: Limited plasma density and control, making them less suitable for advanced or high-precision applications.
-
Challenges and Limitations of Traditional Plasma Sources:
- Versatility: Traditional plasma sources are often limited to specific processes, such as etching or deposition. They may not be easily adaptable to different applications without significant modifications.
- Scalability: The physical characteristics of traditional plasma sources, such as electrode size and plasma density, can limit their scalability. This is particularly challenging for large-scale industrial applications.
- Control and Precision: Achieving precise control over plasma parameters (e.g., ion energy, density) can be difficult with traditional sources, especially in advanced applications like semiconductor manufacturing.
-
Emerging Plasma Technologies:
- Atmospheric Pressure Plasmas: These operate at atmospheric pressure, eliminating the need for vacuum systems. They are being explored for applications like surface treatment and sterilization.
- Remote Plasma Sources: These generate plasma away from the substrate, reducing damage and contamination. They are used in processes like atomic layer deposition (ALD).
- Pulsed Plasmas: These use short pulses of energy to generate plasma, offering better control over ion energy and reducing substrate damage.
In conclusion, while traditional plasma sources like CCP, ICP, microwave, and DC plasmas have been widely used in various applications, they often face limitations in versatility and scalability. Emerging technologies like atmospheric pressure plasmas, remote plasma sources, and pulsed plasmas are addressing some of these challenges, offering new possibilities for advanced applications. Understanding the strengths and limitations of each type of plasma source is crucial for selecting the right technology for specific industrial or scientific needs.
Summary Table:
Plasma Source | Operation | Applications | Advantages | Limitations |
---|---|---|---|---|
Capacitively Coupled Plasmas (CCP) | Uses RF electric fields between electrodes to generate plasma. | Etching, thin-film deposition, surface modification. | Simple design, low cost, good ion energy control. | Limited plasma density and scalability. |
Inductively Coupled Plasmas (ICP) | Uses magnetic fields to induce plasma, generated outside the coil. | Advanced semiconductor processing, high-aspect-ratio etching, ion-assisted deposition. | High plasma density, better ion energy control, scalable for larger substrates. | Complex design, higher cost. |
Microwave Plasmas | Uses microwave energy to ionize gas, delivered via waveguide or antenna. | Diamond film deposition, surface hardening, plasma polymerization. | High energy density, low-pressure operation, suitable for high-temperature processes. | Requires precise microwave control, less common in mainstream applications. |
Direct Current (DC) Plasmas | Uses direct current between electrodes to ionize gas. | Surface cleaning, sputtering, simple deposition. | Simple, cost-effective, easy to operate. | Limited plasma density and control, less suitable for advanced applications. |
Discover the right plasma source for your application—contact our experts today!