Pyrolysis equipment plays a critical role in converting waste materials like plastics, rubber, and biomass into valuable products such as fuel oil, biochar, and gases. The types of pyrolysis reactors vary based on their design, heating methods, and operational efficiency. Common types include flat head, conical head, and ellipsoid head designs, as well as rotary kiln reactors, fluidized bed reactors, and specialized systems like bubbling fluidized beds, circulating fluid beds, transported beds, and ablative pyrolyzers. Each reactor type is tailored for specific applications, such as fast pyrolysis for bio-oil production or slow pyrolysis for biochar. Key design features like heat transfer efficiency, insulation, and safety mechanisms ensure optimal performance and environmental sustainability.
Key Points Explained:
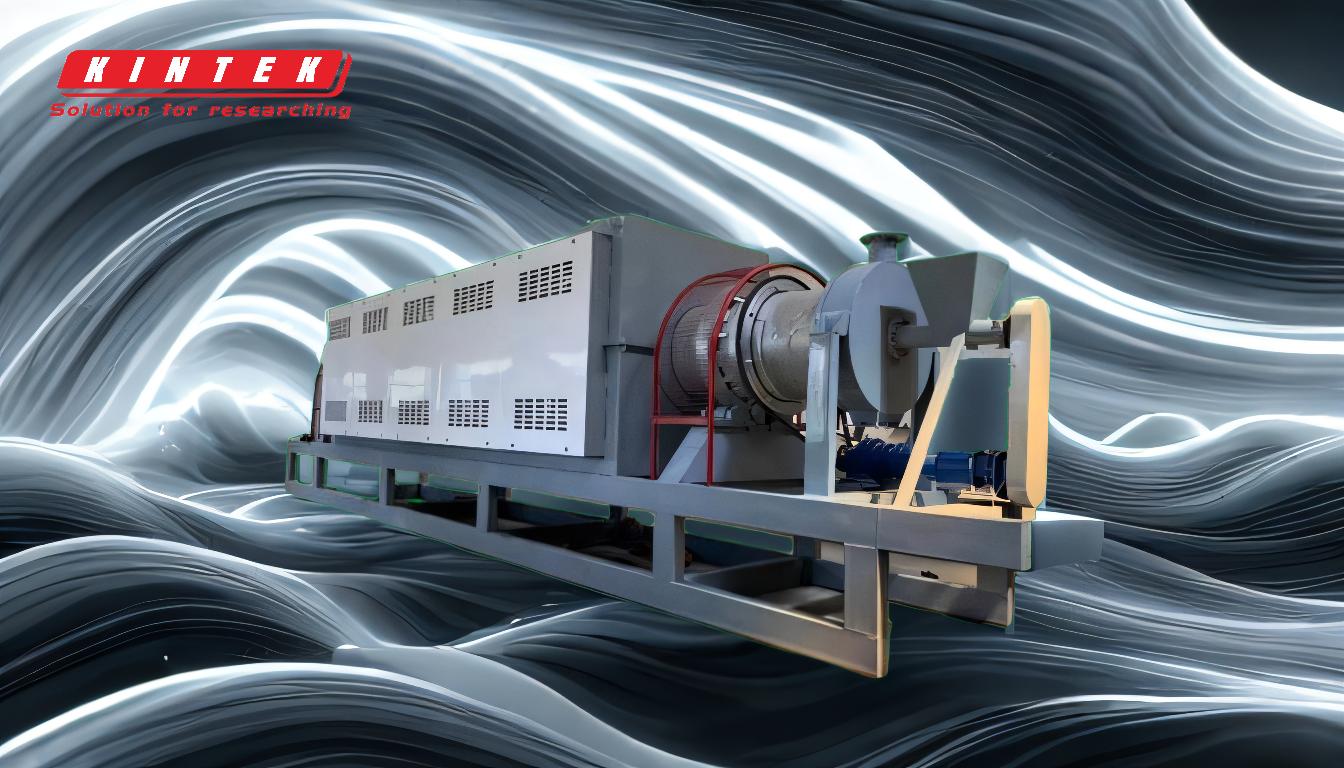
-
Types of Pyrolysis Reactors Based on Head Design:
- Flat Head Design: This design is simple and cost-effective, often used for small-scale pyrolysis processes. It is suitable for applications where uniform heating is not a critical requirement.
- Conical Head Design: This design improves heat distribution and material flow, making it ideal for medium-scale operations. The conical shape helps in better mixing and reduces dead zones.
- Ellipsoid Head Design: This design offers superior heat transfer and structural strength, making it suitable for large-scale industrial applications. It ensures even heating and minimizes stress concentrations.
-
Types of Pyrolysis Reactors Based on Technology:
- Rotary Kiln Reactors: These reactors use indirect heating to break down materials, reducing contamination risks. They are versatile and can handle a wide range of feedstocks, including plastics, rubber, and biomass. The rotating motion ensures uniform heating and efficient pyrolysis.
- Fluidized Bed Reactors: These reactors suspend materials in a gas or liquid, allowing for even heating and faster processing. They are highly efficient and suitable for fast pyrolysis, producing bio-oil as the primary product. The fluidized bed design ensures excellent heat transfer and residence time control.
- Bubbling Fluidized Bed Pyrolyzers: These are a subtype of fluidized bed reactors, characterized by their ability to handle fine particles and produce high-quality bio-oil. They are commonly used in biomass pyrolysis.
- Circulating Fluid Beds: These reactors recycle the bed material, enhancing heat transfer and extending the residence time of the feedstock. They are ideal for continuous pyrolysis processes.
- Transported Beds: These reactors use a carrier gas to transport the feedstock through the reactor, ensuring rapid heating and efficient pyrolysis. They are suitable for large-scale operations.
- Ablative Pyrolyzers: These reactors use mechanical force to press the feedstock against a hot surface, enabling rapid heat transfer and pyrolysis. They are highly efficient but require precise control over operating conditions.
-
Pyrolysis Reactor Design Features:
- Material and Insulation: High-quality boiler steel (Q345R) is used for heat transfer efficiency and longevity. The reactor body and door are insulated with 16mm thick steel and 80mm thick aluminum silicate refractory fiber cotton, ensuring minimal heat loss.
- Welding and Safety: Special welding technology ensures full and neat welds, avoiding defects. Ultrasonic flaw detection tests are conducted to guarantee safety and structural integrity.
- Roller and Motor Design: High-temperature resistant rollers and inverter motors with frequency converters allow for adjustable speed and improved efficiency. Large ring gear structures enhance stability and precision.
- Dynamic Balance Tests: These tests ensure the longevity and stability of the reducer, reducing vibrations and wear during operation.
-
Applications of Pyrolysis Reactors:
- Fast Pyrolysis: Produces bio-oil by rapidly heating biomass to high temperatures (400-700°C). This process is ideal for generating liquid fuels and chemicals.
- Slow Pyrolysis: Produces biochar by heating biomass at lower temperatures (300-400°C). This process is suitable for soil amendment and carbon sequestration.
- Torrefaction: Heats biomass at intermediate temperatures (250-350°C) to produce a solid product with improved fuel characteristics, such as higher energy density and reduced moisture content.
-
Environmental Benefits:
- Pyrolysis reactors are designed to maximize the recycling and reuse of waste materials, contributing to a pollution-free and eco-friendly world. They convert waste plastics, rubbers, tires, and sludge into fuel oil in an oxygen-free and high-temperature environment, helping to solve environmental pollution and reduce landfill waste.
By understanding the different types of pyrolysis reactors and their unique features, purchasers can select the most suitable equipment for their specific applications, ensuring optimal performance and environmental sustainability.
Summary Table:
Type of Reactor | Key Features | Applications |
---|---|---|
Flat Head Design | Simple, cost-effective, uniform heating not critical | Small-scale pyrolysis processes |
Conical Head Design | Improved heat distribution, better mixing, reduced dead zones | Medium-scale operations |
Ellipsoid Head Design | Superior heat transfer, structural strength, even heating | Large-scale industrial applications |
Rotary Kiln Reactors | Indirect heating, versatile, uniform heating | Wide range of feedstocks (plastics, rubber, biomass) |
Fluidized Bed Reactors | Even heating, faster processing, excellent heat transfer | Fast pyrolysis for bio-oil production |
Ablative Pyrolyzers | Rapid heat transfer, mechanical force for pyrolysis | High-efficiency pyrolysis with precise control |
Ready to choose the right pyrolysis equipment for your needs? Contact us today for expert guidance!