Sintering is a critical process in materials science and manufacturing, where powdered materials are heated to form a solid mass without melting. The process relies on various sintering mechanisms, which are driven by thermally activated solid-state diffusion and other physical phenomena. The primary mechanisms include surface diffusion, viscous flow, evaporative coalescence, bulk diffusion, and grain boundary diffusion. These mechanisms are influenced by factors such as temperature, pressure, and the presence of a liquid phase. Different types of sintering, such as solid-state sintering, liquid phase sintering, reactive sintering, microwave sintering, spark plasma sintering, and hot isostatic pressing, utilize these mechanisms to achieve specific material properties and densities. Understanding these mechanisms is essential for optimizing sintering processes and producing high-quality materials.
Key Points Explained:
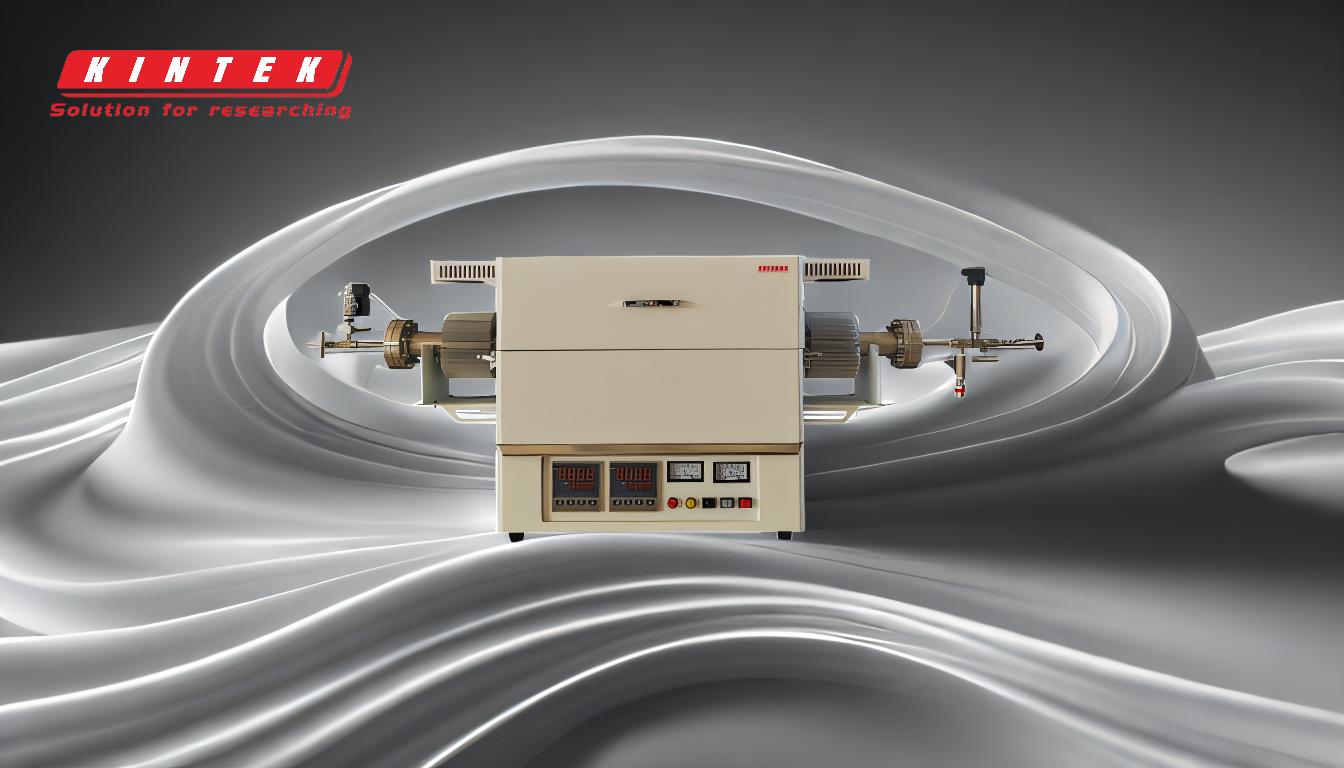
-
Primary Sintering Mechanisms:
- Surface Diffusion: Atoms migrate along the surface of particles, reducing surface energy and promoting particle bonding.
- Viscous Flow: Particles deform and flow under stress, filling gaps and reducing porosity.
- Evaporative Coalescence: Material evaporates from high-energy surfaces and condenses on lower-energy surfaces, leading to particle bonding.
- Bulk Diffusion: Atoms move through the interior of particles, contributing to densification.
- Grain Boundary Diffusion: Atoms migrate along grain boundaries, facilitating particle merging and densification.
-
Types of Sintering:
- Solid-State Sintering: Powdered material is heated just below its melting point, allowing atomic diffusion to bond particles without a liquid phase.
- Liquid Phase Sintering (LPS): A solvent liquid is introduced to reduce porosity and enhance bonding. The liquid is later driven off by heating.
- Reactive Sintering: Involves a chemical reaction between powder particles during heating, leading to the formation of new compounds and enhanced bonding.
- Microwave Sintering: Uses microwave energy to rapidly heat and integrate ceramic materials, reducing processing time.
- Spark Plasma Sintering (SPS): Combines electric current and physical compression to rapidly densify materials.
- Hot Isostatic Pressing (HIP): Applies high pressure and temperature to form and fuse powder particles, resulting in fully dense products.
-
Sintering Process Stages:
- Preparation of the Powder Compact: Powder is compacted using methods like cold welding, 3D printing, or pressing tools in a controlled atmosphere.
- Heating and Consolidation: The compacted powder is heated to just below its melting point, activating diffusion mechanisms and initiating particle bonding.
- Particle Merging: Particles densify and merge, often accelerated by liquid phase sintering.
- Solidification: The material cools and solidifies into a unified mass, achieving the desired mechanical and physical properties.
-
Sinter-HIP Process:
- The Sinter-HIP process combines sintering and hot isostatic pressing to densify materials. It relies on high isostatic pressure to induce material deformation, creep, and diffusion. These mechanisms work together to close pores and eliminate defects, resulting in fully dense and high-quality products.
-
Quantification and Modeling:
- Sintering mechanisms can be quantified using sintering models, often developed with tools like Linseis push rod dilatometers. These models help in understanding and optimizing the sintering process by predicting material behavior under different conditions.
Understanding these sintering mechanisms and processes is crucial for material scientists and engineers to design and produce materials with specific properties, such as high density, strength, and thermal stability. Each type of sintering and its associated mechanisms offer unique advantages, making them suitable for different applications in industries ranging from aerospace to electronics.
Summary Table:
Sintering Mechanism | Description |
---|---|
Surface Diffusion | Atoms migrate along particle surfaces, reducing energy and promoting bonding. |
Viscous Flow | Particles deform under stress, filling gaps and reducing porosity. |
Evaporative Coalescence | Material evaporates and condenses, leading to particle bonding. |
Bulk Diffusion | Atoms move through particle interiors, contributing to densification. |
Grain Boundary Diffusion | Atoms migrate along grain boundaries, aiding particle merging and densification. |
Types of Sintering | Key Characteristics |
---|---|
Solid-State Sintering | Heating below melting point; no liquid phase. |
Liquid Phase Sintering (LPS) | Uses a solvent liquid to reduce porosity and enhance bonding. |
Reactive Sintering | Chemical reactions form new compounds during heating. |
Microwave Sintering | Rapid heating using microwave energy. |
Spark Plasma Sintering (SPS) | Combines electric current and compression for rapid densification. |
Hot Isostatic Pressing (HIP) | Applies high pressure and temperature for fully dense products. |
Optimize your sintering process with expert guidance—contact us today!