Vapor phase deposition is a broad category of techniques used to create thin films and coatings on substrates. It is divided into two main types: Chemical Vapor Deposition (CVD) and Physical Vapor Deposition (PVD). CVD involves chemical reactions to deposit materials, while PVD relies on physical processes like evaporation or sputtering. Each method has unique variants, such as Atmospheric Pressure CVD (APCVD), Low Pressure CVD (LPCVD), Plasma-Enhanced CVD (PECVD), thermal evaporation, and sputtering. These techniques are chosen based on the desired material properties, substrate compatibility, and specific application requirements.
Key Points Explained:
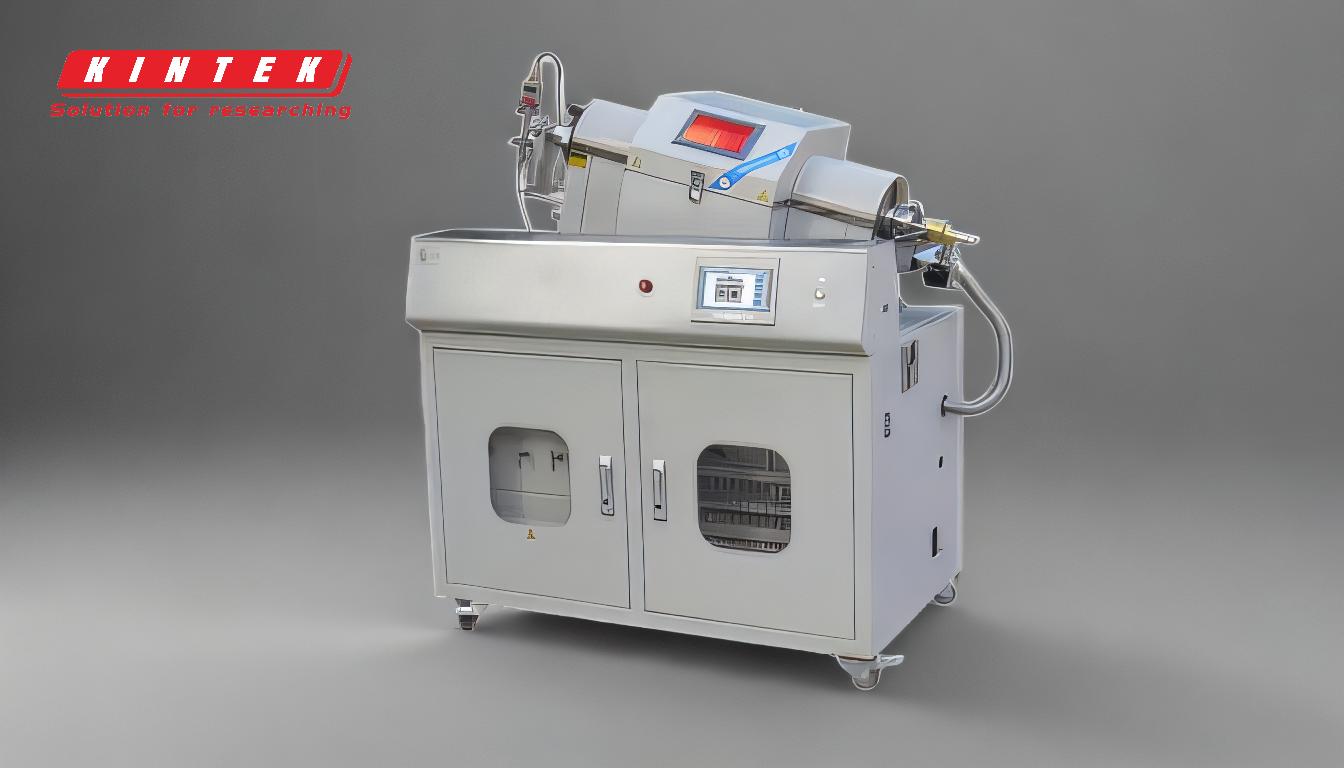
-
Chemical Vapor Deposition (CVD)
CVD is a process where chemical reactions are used to deposit thin films on substrates. It is widely used in semiconductor manufacturing, coatings, and nanotechnology. Key types of CVD include:- Atmospheric Pressure CVD (APCVD): Operates at atmospheric pressure, suitable for high-throughput applications but may result in less uniform films.
- Low Pressure CVD (LPCVD): Conducted under reduced pressure, producing highly uniform and high-quality films, often used in semiconductor fabrication.
- Ultrahigh Vacuum CVD (UHVCVD): Performed in an ultrahigh vacuum environment, ideal for depositing extremely pure and defect-free films.
- Plasma-Enhanced CVD (PECVD): Utilizes plasma to enhance chemical reactions, enabling lower deposition temperatures and faster processing times.
- Metal-Organic CVD (MOCVD): Uses metal-organic precursors, commonly employed for depositing compound semiconductors like gallium nitride (GaN).
- Laser-Induced CVD (LCVD): Employs laser energy to drive chemical reactions, allowing precise localized deposition.
-
Physical Vapor Deposition (PVD)
PVD involves physical processes to deposit materials without chemical reactions. Common PVD techniques include:- Thermal Evaporation: The source material is heated until it vaporizes, and the vapor condenses on the substrate. Simple and cost-effective but limited in material compatibility.
- Electron Beam Evaporation: Uses a high-energy electron beam to vaporize the source material, enabling higher melting point materials to be deposited.
- Sputtering: Involves bombarding a target material with ions to eject atoms, which then deposit on the substrate. Offers excellent film uniformity and adhesion.
-
Key Factors in Vapor Deposition
- Target Materials: The choice of material (e.g., metals, semiconductors, ceramics) depends on the application and desired film properties.
- Deposition Technology: Techniques like atomic layer deposition (ALD) and electron beam lithography offer precise control over film thickness and composition.
- Chamber Pressure: Ranges from atmospheric pressure to ultrahigh vacuum, influencing film quality and deposition rate.
- Substrate Temperature: Affects film adhesion, crystallinity, and uniformity.
-
Applications of Vapor Deposition
- Semiconductor Manufacturing: CVD and PVD are used to deposit conductive, insulating, and semiconducting layers in integrated circuits.
- Optical Coatings: Thin films are applied to lenses, mirrors, and displays to enhance optical properties.
- Protective Coatings: PVD and CVD are used to create wear-resistant, corrosion-resistant, and thermally insulating coatings.
- Nanotechnology: Precise deposition techniques enable the fabrication of nanostructures and devices.
-
Advantages and Limitations
- CVD Advantages: Produces high-quality, uniform films with excellent conformality. Can deposit a wide range of materials.
- CVD Limitations: Often requires high temperatures and complex equipment. Some precursors are hazardous.
- PVD Advantages: Operates at lower temperatures than CVD. Suitable for depositing metals and alloys with strong adhesion.
- PVD Limitations: Limited to materials that can be vaporized or sputtered. May require vacuum conditions, increasing equipment complexity.
By understanding the different types of vapor phase deposition and their specific applications, users can select the most appropriate technique for their needs, ensuring optimal film quality and performance.
Summary Table:
Type | Key Techniques | Applications |
---|---|---|
CVD | APCVD, LPCVD, UHVCVD, PECVD, MOCVD, LCVD | Semiconductor manufacturing, optical coatings, nanotechnology |
PVD | Thermal evaporation, electron beam evaporation, sputtering | Protective coatings, semiconductor layers, wear-resistant coatings |
Key Factors | Target materials, deposition technology, chamber pressure, substrate temperature | Influences film quality, adhesion, and uniformity |
Need help selecting the right vapor deposition technique? Contact our experts today!