Ceramics, while offering numerous advantages such as high hardness, thermal stability, and chemical resistance, also come with several disadvantages that limit their widespread application. These disadvantages primarily revolve around challenges in reliability, density, strength, and manufacturing processes. For instance, achieving uniform structure and fine grains without pores is difficult, and sintering ceramics at lower temperatures without compromising their properties remains a significant hurdle. Additionally, ceramics are inherently brittle, which makes them prone to cracking under stress. These limitations often require advanced manufacturing techniques and careful material selection to mitigate, which can increase costs and complexity.
Key Points Explained:
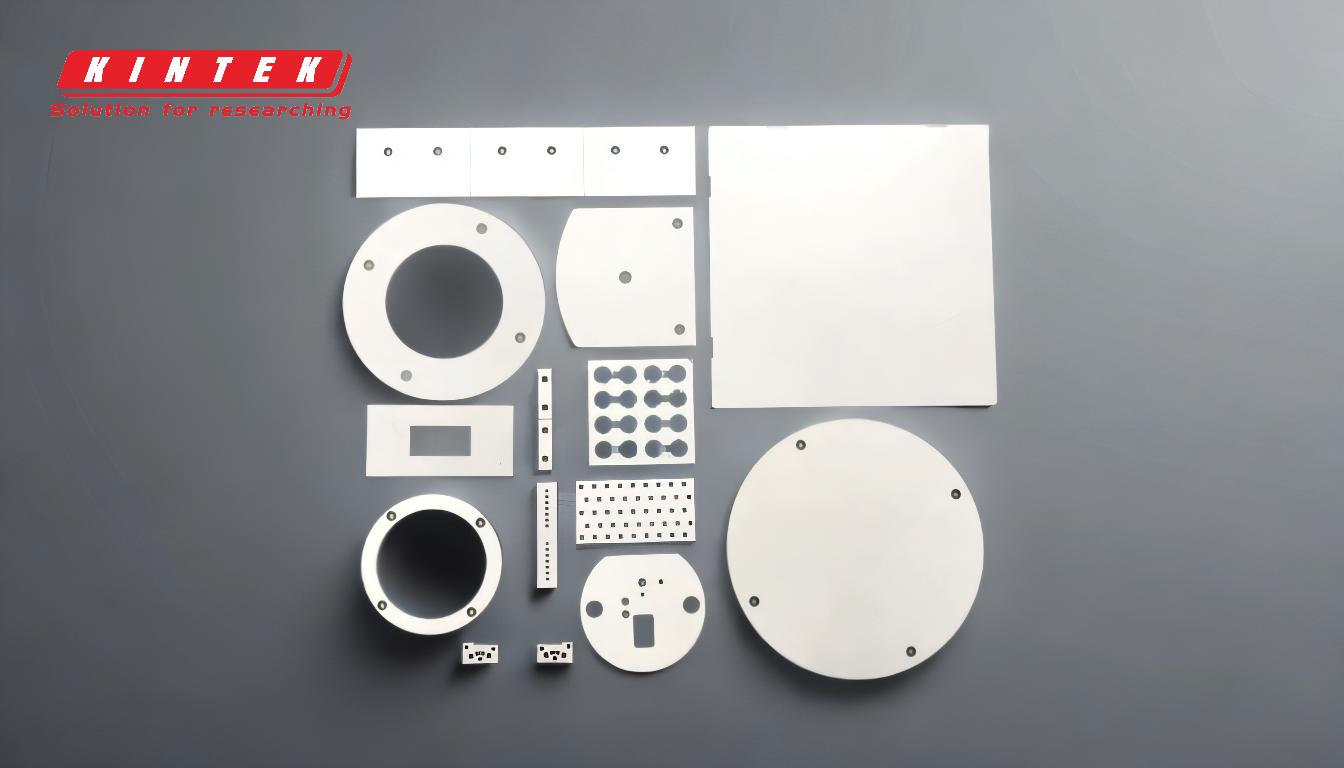
-
Brittleness and Low Fracture Toughness:
- Ceramics are inherently brittle, meaning they lack the ability to deform plastically under stress. This makes them highly susceptible to cracking and fracture, especially under tensile or impact loads.
- Unlike metals, which can absorb energy through deformation, ceramics fail catastrophically once a crack initiates, limiting their use in applications requiring high toughness.
-
Difficulty in Achieving Uniform Density and Structure:
- Manufacturing ceramics with no pores, uniform structure, and fine grains is challenging. Pores and irregularities in the microstructure can act as stress concentrators, reducing the material's overall strength and reliability.
- Achieving rapid densification at lower sintering temperatures is a key goal, as high-temperature sintering can lead to grain growth and weakened grain boundaries.
-
High Manufacturing Costs and Complexity:
- The production of high-quality ceramics often requires advanced techniques such as hot pressing, spark plasma sintering, or chemical vapor deposition, which are expensive and time-consuming.
- Precision in manufacturing is critical to avoid defects, which further increases costs and limits scalability for large-scale applications.
-
Limited Design Flexibility:
- Due to their brittleness, ceramics are difficult to machine or shape into complex geometries without causing cracks or surface damage.
- Post-processing techniques, such as grinding or polishing, are often required, adding to the overall cost and production time.
-
Thermal Shock Susceptibility:
- While ceramics are excellent at withstanding high temperatures, they are prone to thermal shock—sudden temperature changes can cause cracking due to differential expansion and contraction.
- This limits their use in applications where rapid temperature fluctuations are common, such as in certain industrial or aerospace environments.
-
Challenges in Joining and Integration:
- Ceramics are difficult to join with other materials, such as metals or polymers, due to differences in thermal expansion coefficients and bonding mechanisms.
- Specialized techniques, such as brazing or diffusion bonding, are often required, which can be costly and may introduce weak points in the final product.
-
Environmental and Health Concerns:
- The production of some ceramics, particularly those involving toxic materials or high-energy processes, can have environmental and health impacts.
- For example, the sintering process may release harmful gases, and the disposal of ceramic waste can be problematic due to its non-biodegradable nature.
-
Limited Availability of Raw Materials:
- High-performance ceramics often require rare or expensive raw materials, such as zirconia or alumina, which can drive up costs and limit availability.
- The reliance on specific raw materials also makes ceramic production vulnerable to supply chain disruptions.
-
Performance Limitations in Certain Applications:
- While ceramics excel in high-temperature and wear-resistant applications, they may not perform as well in environments requiring high toughness, flexibility, or impact resistance.
- For example, in structural applications where metals or composites might be more suitable, ceramics are often avoided due to their brittleness.
-
Research and Development Challenges:
- Despite ongoing advancements, achieving the ideal combination of properties—such as high strength, toughness, and thermal stability—remains a significant challenge for ceramic material scientists.
- Innovations in nanotechnology and additive manufacturing are being explored to address these limitations, but widespread adoption is still in its early stages.
In summary, while ceramics offer unique advantages, their disadvantages—such as brittleness, manufacturing complexity, and susceptibility to thermal shock—pose significant challenges. Addressing these limitations requires ongoing research, advanced manufacturing techniques, and careful consideration of material properties for specific applications.
Summary Table:
Disadvantage | Key Challenges |
---|---|
Brittleness and Low Fracture Toughness | Prone to cracking under stress; lacks plastic deformation. |
Uniform Density and Structure | Difficult to achieve fine grains and no pores; high sintering temperatures needed. |
High Manufacturing Costs | Requires advanced techniques like hot pressing; precision increases costs. |
Limited Design Flexibility | Difficult to machine; post-processing adds time and cost. |
Thermal Shock Susceptibility | Cracking due to sudden temperature changes. |
Joining and Integration | Hard to bond with metals/polymers; specialized techniques required. |
Environmental and Health Concerns | Toxic materials and high-energy processes pose risks. |
Limited Raw Materials | Reliance on rare or expensive materials like zirconia. |
Performance Limitations | Not suitable for high toughness or impact resistance applications. |
Research and Development | Achieving ideal properties remains a challenge. |
Interested in overcoming ceramic material challenges? Contact our experts today for tailored solutions!