Cold isostatic pressing (CIP) is a widely used manufacturing process that offers numerous advantages, such as producing high-integrity billets with minimal distortion or cracking. However, it also has several disadvantages, including higher tooling costs, process complexity, and limitations in shape and size. These drawbacks can impact its suitability for certain applications and increase production costs. Below, we explore the key disadvantages of cold isostatic pressing in detail.
Key Points Explained:
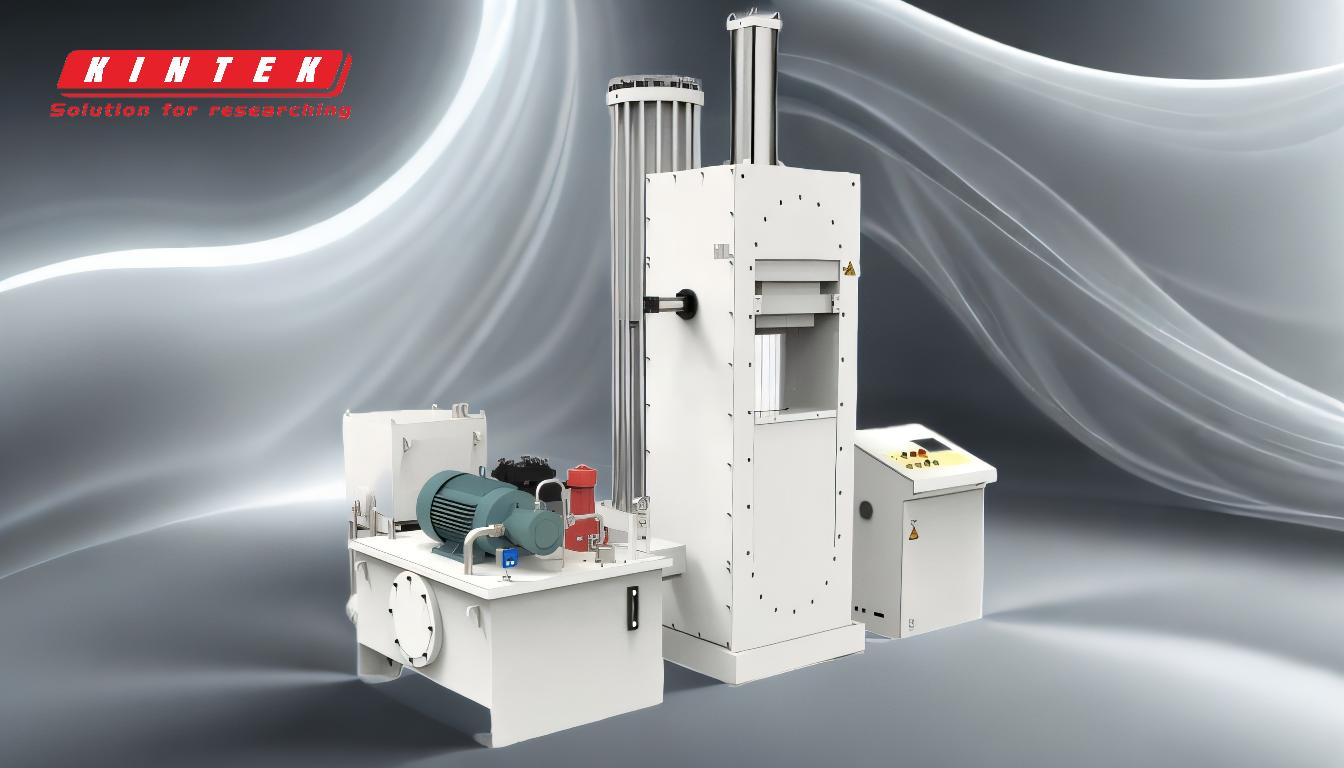
-
Higher Tooling Costs
- Cold isostatic pressing requires specialized equipment, including flexible molds and high-pressure vessels. These tools are more expensive compared to those used in uniaxial pressing.
- The molds must be designed to withstand high pressures, which increases material and manufacturing costs.
- Maintenance and replacement of these molds can also add to the overall expenses, making CIP less economical for small-scale production.
-
Process Complexity
- CIP involves multiple steps, such as loading powder into a flexible mold, sealing the mold, applying pressure via a liquid, and removing the compacted powder body.
- Each step requires precise control to ensure uniform density and avoid defects, increasing the complexity of the process.
- Operators need specialized training to handle the equipment and troubleshoot issues, which can further increase labor costs.
-
Limitations in Shape and Size
- While CIP allows for the engineering of somewhat complex shapes, it has limitations compared to other molding processes.
- Dry-bag isostatic pressing, a variant of CIP, experiences friction on the side of the mold not compressed by the pressurizing liquid, which can lead to uneven density distribution.
- Certain features, such as sharp corners or intricate details, may require additional green machining, adding to the production time and cost.
-
Time-Consuming Process
- The CIP process is slower compared to uniaxial pressing due to the need for careful mold preparation, pressure application, and post-processing steps.
- The time required to achieve uniform compaction and release pressure can delay production schedules, especially for high-volume manufacturing.
-
Material Limitations
- Not all materials are suitable for CIP. Some powders may not compact uniformly under isostatic pressure, leading to defects in the final product.
- The process may also require specific binders or additives to improve powder flow and compaction, which can increase material costs.
-
Environmental and Safety Concerns
- The use of high-pressure liquids in CIP poses safety risks, requiring stringent safety protocols and equipment.
- The disposal of used pressure fluids and cleaning of molds can have environmental implications, necessitating proper waste management systems.
In summary, while cold isostatic pressing offers significant advantages in terms of product quality and performance, its disadvantages—such as higher tooling costs, process complexity, and limitations in shape and size—must be carefully considered when selecting a manufacturing process. These factors can impact the feasibility and cost-effectiveness of CIP for specific applications.
Summary Table:
Disadvantage | Details |
---|---|
Higher Tooling Costs | Specialized equipment like flexible molds and high-pressure vessels are expensive. |
Process Complexity | Multiple steps require precise control, increasing labor and operational costs. |
Limitations in Shape/Size | Complex shapes and sharp corners may need additional machining, raising costs. |
Time-Consuming Process | Slower than uniaxial pressing due to careful mold prep and pressure release. |
Material Limitations | Not all powders compact uniformly, requiring binders or additives. |
Environmental/Safety Risks | High-pressure liquids pose safety risks and require proper waste management. |
Want to learn more about cold isostatic pressing and its challenges? Contact our experts today for tailored advice!