Dry ashing is a widely used method for preparing samples for elemental analysis, particularly in environmental, food, and biological sciences. While it is effective for many applications, it has several notable disadvantages. These include potential loss of volatile elements, incomplete ashing of certain materials, contamination risks, and the requirement for high temperatures that may damage lab equipment. Additionally, dry ashing can be time-consuming and may not be suitable for all sample types, particularly those with high organic content or heat-sensitive components. Understanding these limitations is crucial for selecting the appropriate sample preparation method for specific analytical needs.
Key Points Explained:
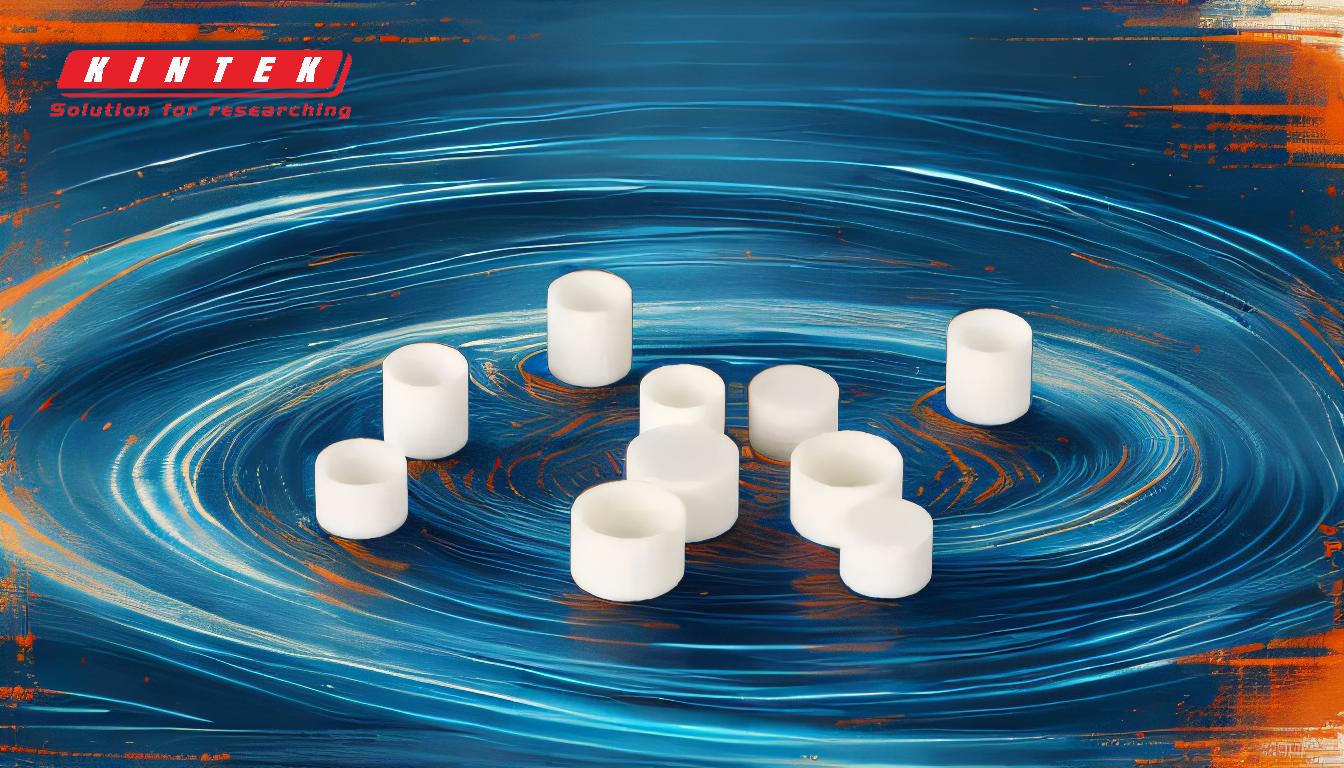
-
Loss of Volatile Elements
- Dry ashing involves heating samples at high temperatures (typically 450–600°C) to oxidize organic matter and leave behind inorganic residues.
- During this process, volatile elements such as mercury, arsenic, selenium, and lead can be lost due to evaporation or sublimation.
- This makes dry ashing unsuitable for analyzing samples where these elements are of interest, as the results may be inaccurate or incomplete.
-
Incomplete Ashing
- Some materials, particularly those with high carbon or refractory content, may not fully ash at the temperatures used in dry ashing.
- Incomplete ashing can leave behind residual organic matter, which can interfere with subsequent analytical techniques like atomic absorption spectroscopy (AAS) or inductively coupled plasma (ICP).
- This limitation often necessitates additional steps, such as wet ashing, to ensure complete sample preparation.
-
Risk of Contamination
- Dry ashing requires the use of crucibles or other containers made of materials like porcelain, quartz, or platinum.
- These materials can introduce contaminants into the sample, especially if they are not properly cleaned or if they react with the sample at high temperatures.
- Contamination can lead to inaccurate results, particularly for trace element analysis.
-
High Temperature Requirements
- The high temperatures used in dry ashing can damage or degrade heat-sensitive components in the sample, such as certain organic compounds or volatile organic compounds (VOCs).
- This limits the applicability of dry ashing for samples that require preservation of specific chemical structures or compounds.
-
Time-Consuming Process
- Dry ashing is a relatively slow process, often requiring several hours to complete, depending on the sample type and size.
- This can be a disadvantage in high-throughput laboratories where rapid sample preparation is essential.
-
Unsuitability for Certain Sample Types
- Samples with high organic content, such as fats, oils, or waxes, may not ash uniformly, leading to inconsistent results.
- Heat-sensitive samples, such as certain biological tissues or polymers, may degrade or lose critical components during the ashing process.
- In such cases, alternative methods like wet ashing or microwave digestion may be more appropriate.
-
Equipment Wear and Tear
- The high temperatures used in dry ashing can cause wear and tear on laboratory equipment, such as muffle furnaces and crucibles.
- Over time, this can lead to increased maintenance costs and the need for frequent replacement of equipment.
-
Limited Applicability for Trace Analysis
- Dry ashing is generally less suitable for trace element analysis due to the potential for contamination and loss of volatile elements.
- For trace analysis, more sensitive and precise methods, such as wet ashing or microwave-assisted digestion, are often preferred.
In summary, while dry ashing is a valuable technique for many applications, its disadvantages must be carefully considered when selecting a sample preparation method. Factors such as the sample type, target elements, and analytical requirements should guide the choice of method to ensure accurate and reliable results.
Summary Table:
Disadvantage | Description |
---|---|
Loss of Volatile Elements | Volatile elements like mercury and lead can evaporate, leading to inaccurate results. |
Incomplete Ashing | High carbon or refractory materials may not fully ash, requiring additional steps. |
Risk of Contamination | Crucibles can introduce contaminants, affecting trace element analysis. |
High Temperature Requirements | Heat-sensitive components may degrade, limiting applicability. |
Time-Consuming Process | Dry ashing can take several hours, slowing down high-throughput labs. |
Unsuitability for Certain Types | High organic or heat-sensitive samples may not ash uniformly. |
Equipment Wear and Tear | High temperatures can damage lab equipment, increasing maintenance costs. |
Limited Trace Analysis Use | Not ideal for trace element analysis due to contamination and volatile loss. |
Need help selecting the right sample preparation method? Contact our experts today for tailored solutions!