Furnace brazing, particularly using a vacuum brazing furnace, is a highly effective method for joining metal components with precision and minimal contamination. However, it does come with certain disadvantages that can affect its suitability for specific applications. These include the need for close fits to enable capillary action, the potential annealing of component parts, and design considerations for brazing material placement. Understanding these drawbacks is crucial for engineers and manufacturers to make informed decisions about whether furnace brazing is the right process for their needs.
Key Points Explained:
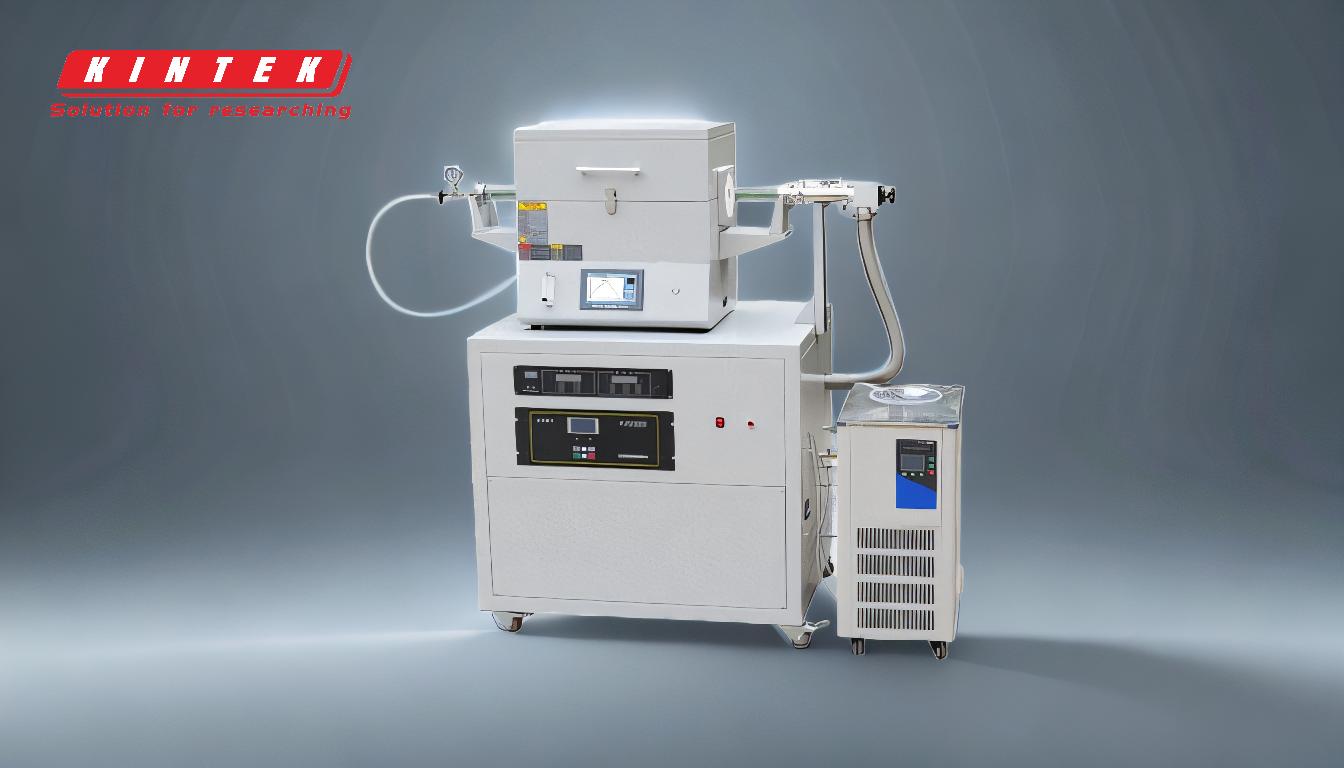
-
Necessity for Close Fits:
- Furnace brazing relies heavily on capillary action to draw the molten filler metal into the joint. This requires the parts to be joined to have very close fits, typically within a few thousandths of an inch. If the gap is too wide, the filler metal may not flow properly, leading to weak or incomplete joints. This necessity for precision in part fitment can increase manufacturing complexity and cost.
-
Annealing of Component Parts:
- During the furnace brazing process, the entire assembly is heated to the brazing temperature, which can be high enough to anneal the base materials. Annealing softens the metal, which can be detrimental if the components are required to maintain their hardness and strength. This is particularly problematic for parts that have been heat-treated or work-hardened prior to brazing.
-
Design Considerations for Brazing Material Placement:
- The design of the components must account for the placement of the brazing material. This often means incorporating features such as grooves, channels, or pre-forms to hold the filler metal in place before heating. These design modifications can complicate the manufacturing process and may require additional machining steps, increasing both time and cost.
-
Potential for Part Distortion:
- Although vacuum brazing is known for minimizing part distortion compared to other joining methods, there is still a risk, especially with complex or thin-walled components. The uniform heating and cooling cycles can induce stresses that lead to warping or distortion, which may necessitate additional post-braze machining or straightening.
-
High Initial Investment:
- The equipment required for furnace brazing, particularly vacuum brazing furnaces, represents a significant capital investment. These furnaces are complex and expensive to purchase, install, and maintain. Additionally, the process often requires specialized tooling and fixtures, further increasing the initial costs.
-
Limited to Certain Materials:
- While furnace brazing is versatile, it is not suitable for all materials. Some metals and alloys may not respond well to the high temperatures involved, or they may require specific atmospheres or fluxes that are not compatible with vacuum brazing. This limitation can restrict the applicability of furnace brazing in certain industries or for specific components.
-
Cycle Time and Throughput:
- The brazing process, especially in a vacuum furnace, can be time-consuming. The need to evacuate the chamber, heat the components, maintain the brazing temperature, and then cool the parts slowly to prevent oxidation or distortion can result in long cycle times. This can limit throughput and may not be suitable for high-volume production where speed is critical.
In summary, while furnace brazing, particularly using a vacuum brazing furnace, offers numerous advantages such as high-quality joints, minimal contamination, and the ability to join complex assemblies, it is not without its drawbacks. These include the need for precise part fitment, potential annealing of components, design complexities, risk of distortion, high initial costs, material limitations, and long cycle times. Understanding these disadvantages is essential for making informed decisions about the suitability of furnace brazing for specific applications.
Summary Table:
Disadvantage | Description |
---|---|
Necessity for Close Fits | Requires precise part fitment for capillary action, increasing complexity and cost. |
Annealing of Component Parts | High temperatures may soften metals, reducing hardness and strength. |
Design Considerations | Requires grooves or channels for filler metal placement, adding manufacturing steps. |
Potential for Part Distortion | Risk of warping or distortion, especially in thin-walled or complex components. |
High Initial Investment | Expensive equipment, tooling, and maintenance costs. |
Limited to Certain Materials | Not suitable for all metals or alloys due to temperature and compatibility issues. |
Cycle Time and Throughput | Long process times, limiting suitability for high-volume production. |
Need help deciding if furnace brazing is right for your application? Contact our experts today for personalized advice!