Heat treatment of metals is a widely used process to enhance mechanical properties such as hardness, strength, and toughness. However, it comes with several disadvantages that can impact the material's performance, cost, and application suitability. These drawbacks include potential distortion or warping, residual stresses, reduced ductility, increased brittleness, and higher costs associated with energy consumption and equipment. Additionally, improper heat treatment can lead to inconsistent results, making it crucial to carefully control the process. Below, we explore these disadvantages in detail to provide a comprehensive understanding of the challenges associated with heat treatment.
Key Points Explained:
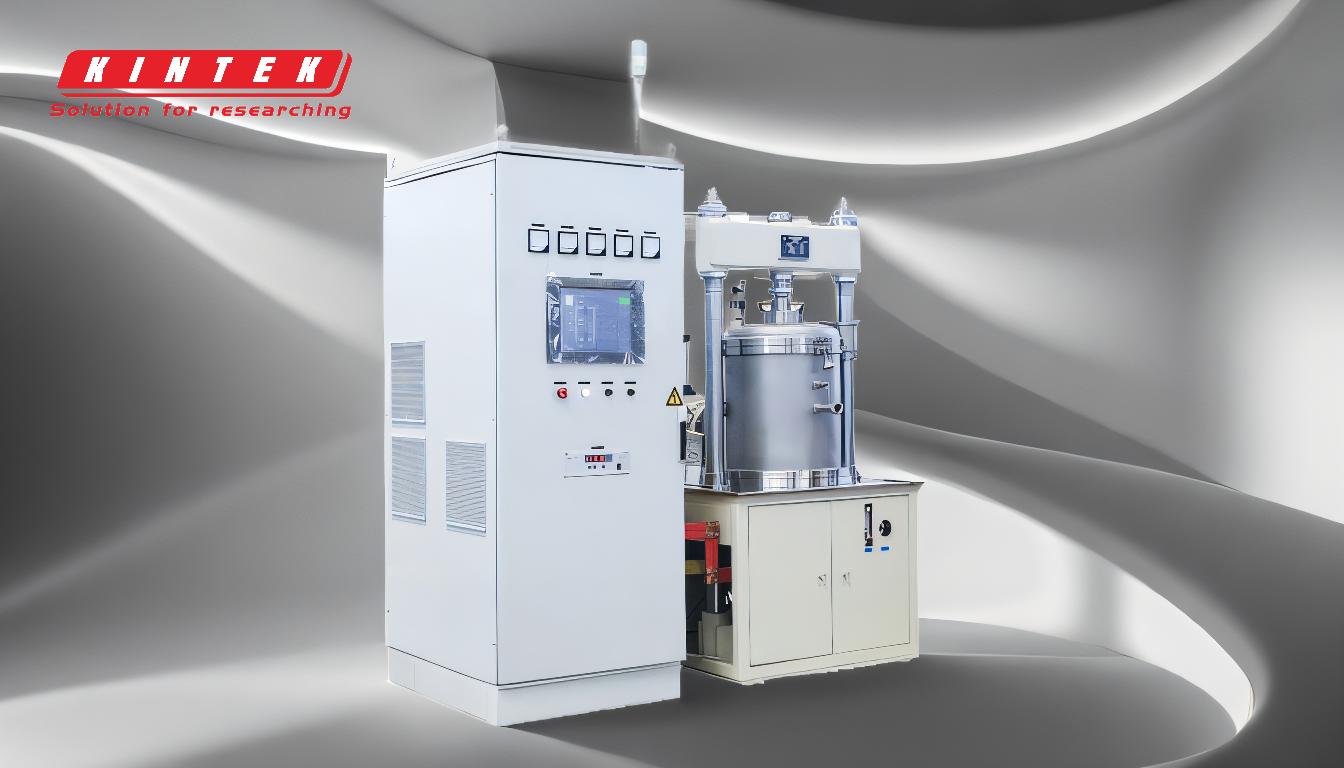
-
Distortion and Warping
- During heat treatment, metals undergo significant temperature changes, which can cause uneven expansion and contraction. This often leads to distortion or warping of the material.
- Thin or complex-shaped components are particularly susceptible to these issues, as they lack the structural integrity to withstand thermal stresses.
- Distortion can render parts unusable, requiring additional machining or even scrapping, which increases costs and waste.
-
Residual Stresses
- Rapid cooling, such as quenching, can introduce residual stresses within the metal. These stresses occur because the outer layers cool faster than the inner layers, creating internal tension.
- Residual stresses can compromise the structural integrity of the material, leading to premature failure under load or during service.
- Stress-relief treatments may be required to mitigate this issue, adding extra steps and costs to the process.
-
Reduced Ductility and Increased Brittleness
- While heat treatment can improve hardness and strength, it often reduces ductility, making the material more brittle.
- Brittle materials are prone to cracking or fracturing under impact or stress, limiting their suitability for applications requiring toughness.
- For example, over-hardening a steel component can make it too brittle for use in high-stress environments like automotive or aerospace applications.
-
Energy Consumption and Environmental Impact
- Heat treatment processes, such as annealing, quenching, and tempering, require significant energy input to achieve and maintain high temperatures.
- This high energy consumption contributes to increased operational costs and a larger carbon footprint, making heat treatment less environmentally friendly.
- Industries are increasingly seeking alternative methods to reduce energy usage and environmental impact.
-
Cost of Equipment and Maintenance
- Heat treatment requires specialized equipment, such as furnaces, quenching tanks, and tempering ovens, which can be expensive to purchase and maintain.
- Regular maintenance is necessary to ensure consistent results, adding to the overall cost of the process.
- Small-scale manufacturers may find it challenging to justify the investment in such equipment.
-
Inconsistent Results Due to Improper Control
- Heat treatment is a highly sensitive process that requires precise control over temperature, cooling rates, and time.
- Variations in these parameters can lead to inconsistent results, such as uneven hardness or incomplete transformation of the microstructure.
- Skilled operators and advanced monitoring systems are essential to achieve reliable outcomes, further increasing costs.
-
Material-Specific Limitations
- Not all metals respond well to heat treatment. For example, some alloys may not achieve the desired properties or may require extremely specific conditions.
- Certain materials, like aluminum or titanium, have unique heat treatment requirements that can complicate the process and limit its effectiveness.
- This restricts the versatility of heat treatment as a universal solution for improving metal properties.
-
Potential for Surface Oxidation and Decarburization
- Exposure to high temperatures can cause surface oxidation, leading to the formation of scale or oxide layers on the metal.
- Decarburization, the loss of carbon from the surface of steel, can occur during heat treatment, reducing surface hardness and strength.
- These issues often necessitate additional finishing processes, such as grinding or coating, to restore the desired surface properties.
-
Time-Consuming Process
- Heat treatment is not a quick process. Depending on the type of treatment and the material, it can take hours or even days to complete.
- This extended processing time can delay production schedules and increase lead times, impacting overall efficiency.
- For industries requiring rapid turnaround, alternative methods may be more suitable.
-
Health and Safety Risks
- Heat treatment involves working with high temperatures, flammable materials (e.g., quenching oils), and potentially hazardous gases.
- Operators must follow strict safety protocols to prevent accidents, such as burns, fires, or exposure to toxic fumes.
- Ensuring a safe working environment adds to the complexity and cost of the process.
By understanding these disadvantages, manufacturers and engineers can make informed decisions about whether heat treatment is the right choice for their specific application. While it offers significant benefits, the challenges associated with the process must be carefully weighed against the desired outcomes.
Summary Table:
Disadvantage | Key Impact |
---|---|
Distortion and Warping | Uneven expansion/contraction, especially in thin or complex parts. |
Residual Stresses | Internal tension from rapid cooling, leading to premature failure. |
Reduced Ductility | Increased brittleness, making materials prone to cracking. |
Energy Consumption | High energy use increases costs and environmental impact. |
Equipment Costs | Expensive furnaces, quenching tanks, and maintenance. |
Inconsistent Results | Improper control leads to uneven hardness or incomplete transformations. |
Material-Specific Limitations | Not all metals respond well to heat treatment. |
Surface Oxidation | Scale formation and decarburization reduce surface hardness. |
Time-Consuming | Long processing times delay production schedules. |
Health and Safety Risks | High temperatures, flammable materials, and hazardous gases pose risks. |
Need help deciding if heat treatment is right for your application? Contact our experts today for tailored advice!