Induction heaters, while efficient and versatile, come with several disadvantages that can impact their usability and cost-effectiveness. These include the need for dedicated and often expensive inductors, high-current density management, lack of refining capacity in induction furnaces, poor adaptability for complex workpieces, significant initial investment, and the requirement for skilled personnel. Additionally, induction heating is primarily effective for surface heating, which may limit its application in certain heat treatment processes. Understanding these drawbacks is crucial for making informed decisions when considering induction heating technology for specific applications.
Key Points Explained:
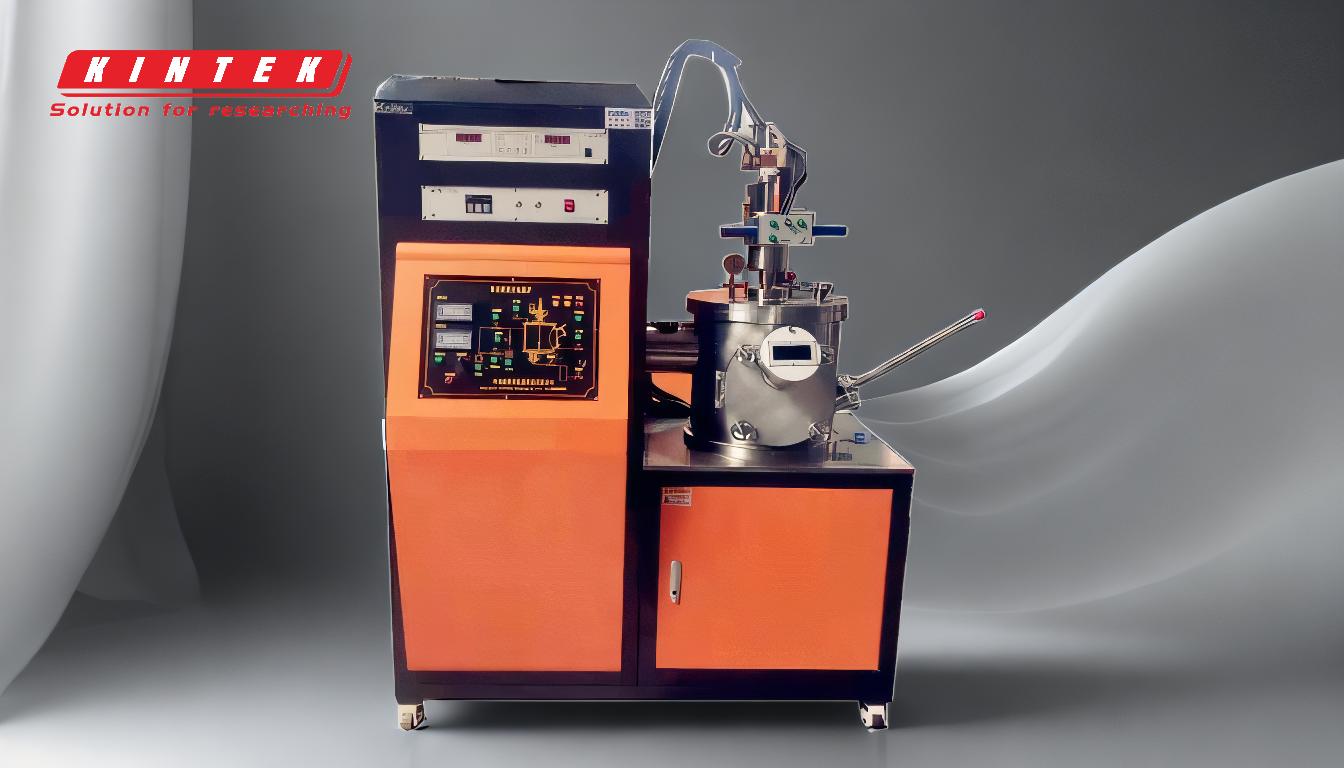
-
Need for Dedicated Inductors:
- Induction heating requires the production of specialized inductors tailored to specific applications. This customization can be costly and time-consuming, limiting the flexibility of the technology.
- Example: For different shapes and sizes of workpieces, unique inductors must be designed and manufactured, increasing both initial and ongoing costs.
-
High-Current Density Management:
- Managing high-current densities in small copper inductors is a significant challenge. This often necessitates specialized engineering and precise 'copper-fitting' to ensure efficient operation and prevent overheating.
- Example: High-current densities can lead to increased wear and tear on the inductors, requiring frequent maintenance and potential replacements.
-
Lack of Refining Capacity in Induction Furnaces:
- Induction furnaces do not have the capability to refine materials. The charge materials must be free of oxides and of a known composition, which can be a limitation in some industrial processes.
- Example: In metal melting applications, any oxides present in the charge materials can lead to the loss of alloying elements, necessitating their re-addition to the melt.
-
Poor Adaptability for Complex Workpieces:
- Induction hardening technology is not well-suited for complex mechanical parts. It is primarily effective for simple workpieces in assembly line production.
- Example: Complex geometries and intricate designs may not achieve uniform heating, leading to inconsistent hardening results.
-
Significant Initial Investment:
- The initial cost of setting up an induction heating system can be high, including the expense of specialized equipment and power supplies.
- Example: Purchasing and installing an induction furnace, along with the necessary power converters and control systems, requires a substantial upfront investment.
-
Requirement for Skilled Personnel:
- Operating induction heating systems requires skilled personnel with expertise in induction heating principles and safety procedures.
- Example: Proper training and experience are necessary to ensure safe and efficient operation, which can add to the overall cost and complexity.
-
Primarily Effective for Surface Heating:
- Induction heating is most effective for surface heating, which may limit its application in certain heat treatment processes that require uniform heating throughout the material.
- Example: For processes that need deep penetration heating, such as through-hardening of thick sections, induction heating may not be the most suitable method.
-
Control and Optimization Challenges:
- Robust control algorithms are required to manage different induction heating loads and operating points. Multi-coil systems present additional challenges in terms of control and optimization.
- Example: Implementing real-time identification control units with adaptive algorithms can improve performance, but it adds to the complexity and cost of the system.
Understanding these disadvantages is essential for evaluating the suitability of induction heating technology for specific applications and ensuring that the benefits outweigh the potential drawbacks.
Summary Table:
Disadvantage | Description | Example |
---|---|---|
Need for Dedicated Inductors | Custom inductors are costly and time-consuming to produce. | Unique inductors required for different workpiece shapes increase costs. |
High-Current Density Management | Managing high currents in small inductors is challenging and requires precision. | High-current density leads to wear and tear, requiring frequent maintenance. |
Lack of Refining Capacity | Induction furnaces cannot refine materials, requiring pre-cleaned charge. | Oxides in charge materials lead to alloy loss, necessitating re-addition. |
Poor Adaptability for Complex Workpieces | Limited effectiveness for complex geometries. | Inconsistent heating results in complex parts. |
Significant Initial Investment | High setup costs for equipment and power supplies. | Induction furnaces and control systems require substantial upfront costs. |
Requirement for Skilled Personnel | Skilled operators are needed for safe and efficient operation. | Training adds to operational costs and complexity. |
Primarily Effective for Surface Heating | Limited to surface heating, not suitable for deep penetration. | Unsuitable for through-hardening thick sections. |
Control and Optimization Challenges | Complex algorithms needed for multi-coil systems. | Adaptive control units increase system complexity and cost. |
Need help deciding if induction heating is right for your application? Contact our experts today for personalized advice!