Nitriding and carburizing are both case-hardening processes used to enhance the surface properties of metals, but they have distinct differences in terms of their applications, advantages, and disadvantages. While nitriding offers benefits such as improved hardness, wear resistance, and fatigue life, it also has several disadvantages compared to carburizing. These include limitations in case depth, material compatibility, process temperature, and post-treatment requirements. Below, we explore the key disadvantages of nitriding over carburizing in detail.
Key Points Explained:
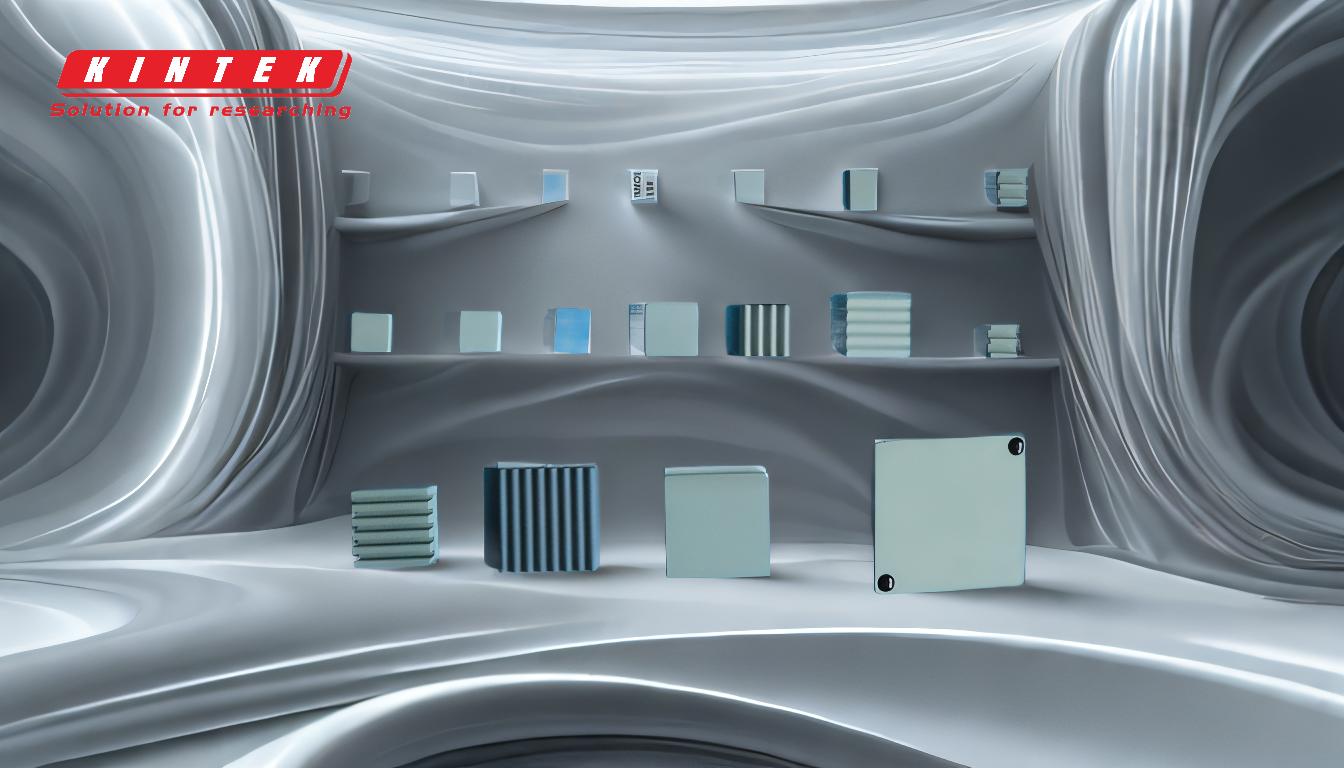
-
Limited Case Depth
- Nitriding typically produces a thinner case depth compared to carburizing.
- Carburizing can achieve case depths ranging from 0.5 mm to 2 mm or more, depending on the process duration and material.
- Nitriding, on the other hand, usually results in case depths of 0.1 mm to 0.6 mm, which may not be sufficient for applications requiring deeper hardened layers.
- This limitation makes nitriding less suitable for parts subjected to high wear or heavy loads, where a thicker hardened layer is necessary.
-
Material Compatibility
- Nitriding is primarily effective on specific alloy steels, such as those containing chromium, molybdenum, and aluminum, which form hard nitrides.
- Carburizing, however, can be applied to a broader range of low-carbon and alloy steels, making it more versatile.
- This restricted material compatibility of nitriding limits its use in industries where a wide variety of steel grades are employed.
-
Lower Process Temperature
- Nitriding is performed at relatively lower temperatures (typically 500°C to 570°C) compared to carburizing (typically 850°C to 950°C).
- While the lower temperature reduces distortion and energy consumption, it also limits the diffusion of nitrogen into the metal, resulting in a shallower case depth.
- Carburizing's higher temperature allows for deeper carbon diffusion, making it more effective for applications requiring significant case hardening.
-
Post-Treatment Requirements
- Nitriding does not require quenching after the process, which reduces the risk of distortion.
- However, the lack of quenching means that nitrided parts may have lower core hardness compared to carburized parts, which undergo quenching and tempering to achieve a hard surface and tough core.
- This limitation can affect the overall mechanical performance of nitrided components, particularly in high-stress applications.
-
Surface Finish and Aesthetics
- Nitriding can sometimes result in a surface finish that is less aesthetically pleasing due to the formation of a brittle "white layer" (a compound layer of iron nitrides).
- This layer may require additional post-processing, such as grinding or polishing, to achieve the desired surface quality.
- Carburizing, followed by quenching and tempering, generally produces a smoother and more uniform surface finish, reducing the need for additional finishing steps.
-
Cost and Complexity
- Nitriding processes, such as gas nitriding or plasma nitriding, can be more complex and costly compared to carburizing.
- The need for precise control of nitrogen-containing atmospheres or plasma environments increases equipment and operational costs.
- Carburizing, being a more established and widely used process, is often more cost-effective and easier to implement in large-scale production environments.
-
Application-Specific Limitations
- Nitriding is less effective for parts requiring through-hardening or those subjected to high-impact loads, as it primarily hardens the surface.
- Carburizing, with its deeper case depth and ability to harden both the surface and core, is better suited for such applications.
- Additionally, nitrided parts may exhibit reduced toughness, making them less suitable for dynamic or impact-heavy environments.
In summary, while nitriding offers advantages such as reduced distortion and improved wear resistance, its disadvantages—such as limited case depth, restricted material compatibility, and higher costs—make carburizing a more versatile and effective choice for many industrial applications. The decision between nitriding and carburizing ultimately depends on the specific requirements of the part, including its intended use, material composition, and desired mechanical properties.
Summary Table:
Aspect | Nitriding | Carburizing |
---|---|---|
Case Depth | 0.1 mm to 0.6 mm (thinner) | 0.5 mm to 2 mm or more (deeper) |
Material Compatibility | Limited to specific alloy steels (e.g., Cr, Mo, Al) | Compatible with a wide range of low-carbon and alloy steels |
Process Temperature | 500°C to 570°C (lower) | 850°C to 950°C (higher) |
Post-Treatment | No quenching required (lower core hardness) | Quenching and tempering (higher core hardness) |
Surface Finish | May require additional finishing due to brittle "white layer" | Smoother and more uniform finish |
Cost and Complexity | Higher cost and complexity (e.g., gas/plasma nitriding) | More cost-effective and easier to implement |
Applications | Less effective for high-impact or through-hardening applications | Better suited for high-impact and through-hardening applications |
Need help choosing the right case-hardening process for your application? Contact our experts today!