Austempering is a heat treatment process that offers several advantages, such as improved ductility, toughness, and reduced distortion compared to traditional quenching and tempering. However, it also has notable disadvantages, including limitations in material suitability, higher costs, and process complexity. The process is not universally applicable to all steels, particularly those with high carbon content, and it requires precise control of temperature and time, which can increase operational costs. Additionally, the need for specialized equipment and the longer processing times can make austempering less efficient for high-volume production. These factors must be carefully considered when deciding whether to use austempering for a specific application.
Key Points Explained:
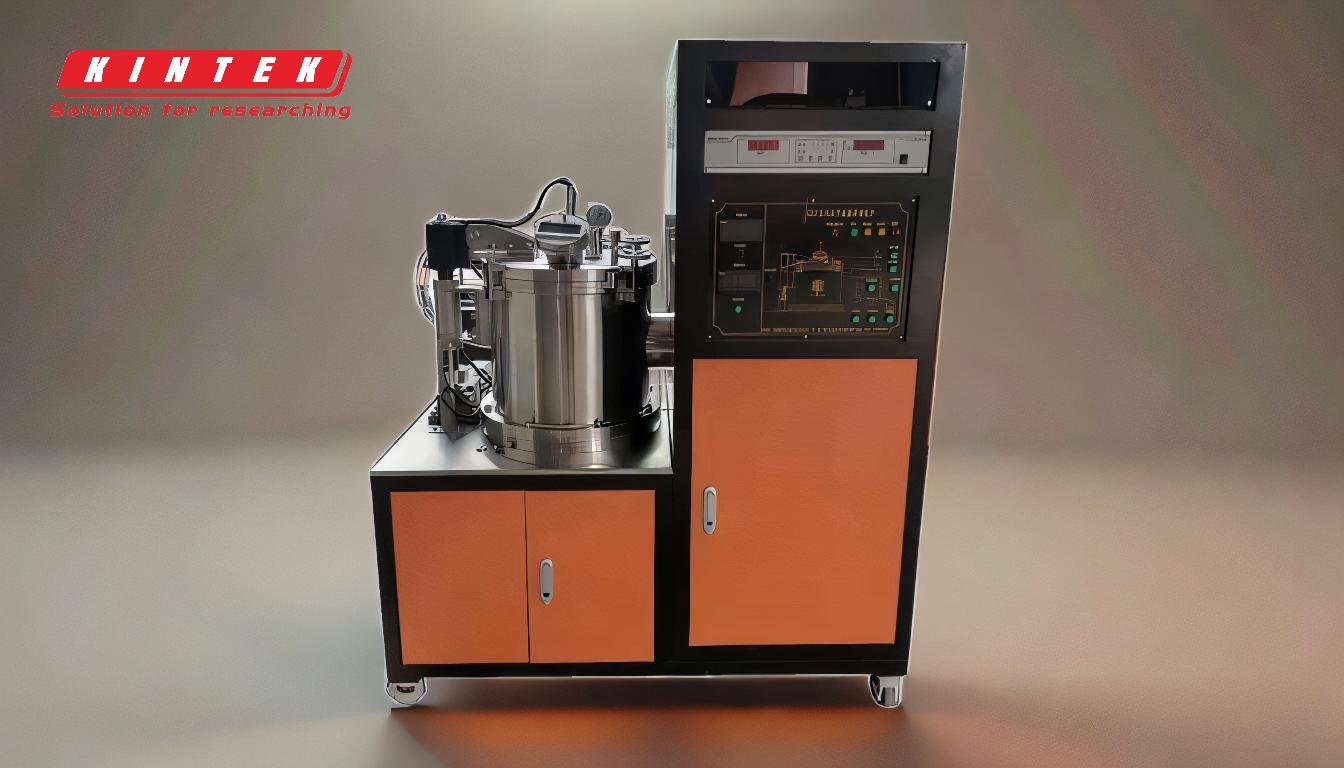
-
Material Limitations:
- Not Suitable for All Steels: Austempering is most effective for medium-carbon steels and certain alloy steels. High-carbon steels, such as tool steels, are less suitable because they may not achieve the desired microstructure (bainite) due to their high hardenability and risk of forming martensite.
- Restricted to Specific Applications: The process is not universally applicable and is often limited to parts requiring high toughness and wear resistance, such as gears, springs, and agricultural equipment.
-
Higher Costs:
- Specialized Equipment: Austempering requires precise temperature control and specialized quenching baths (e.g., salt baths or molten metal baths), which can be expensive to set up and maintain.
- Longer Processing Times: The process involves holding the material at an intermediate temperature for an extended period to form bainite, which increases energy consumption and labor costs compared to traditional quenching and tempering.
-
Process Complexity:
- Precise Temperature and Time Control: Achieving the desired bainitic microstructure requires strict control over the temperature of the quenching medium and the duration of the isothermal hold. Any deviation can result in undesirable microstructures, such as martensite or pearlite.
- Limited Thickness Compatibility: Thicker sections may not cool uniformly, leading to inconsistent microstructure and properties. This restricts austempering to parts with relatively uniform cross-sections.
-
Reduced Efficiency for High-Volume Production:
- Slower Cycle Times: The extended hold times required for bainite formation make austempering less suitable for high-volume production where rapid processing is essential.
- Batch Processing Limitations: The process is often conducted in batches, which can limit throughput compared to continuous heat treatment methods.
-
Potential for Inconsistent Results:
- Sensitivity to Cooling Rate: The cooling rate must be carefully controlled to avoid the formation of martensite, which can compromise the desired mechanical properties.
- Dependence on Quenching Medium: The effectiveness of austempering depends on the quenching medium's ability to maintain a consistent temperature, which can be challenging in large-scale operations.
-
Environmental and Safety Concerns:
- Use of Salt Baths: Salt baths, commonly used in austempering, can pose environmental and safety risks due to the potential for salt spills, fumes, and the need for proper disposal.
- Handling Molten Metals: If molten metal baths are used, additional safety precautions are required to protect workers from burns and exposure to hazardous materials.
In conclusion, while austempering offers significant benefits in terms of mechanical properties and reduced distortion, its disadvantages—such as material limitations, higher costs, process complexity, and reduced efficiency for high-volume production—must be carefully weighed. These factors make it less suitable for certain applications and require careful consideration of the specific requirements of the part being treated.
Summary Table:
Disadvantage | Details |
---|---|
Material Limitations | Not suitable for high-carbon steels; limited to specific applications. |
Higher Costs | Requires specialized equipment and longer processing times. |
Process Complexity | Precise temperature and time control needed; limited thickness compatibility. |
Reduced Efficiency | Slower cycle times; batch processing limits throughput. |
Inconsistent Results | Sensitivity to cooling rate; dependence on quenching medium. |
Environmental & Safety Risks | Use of salt baths and molten metals poses risks. |
Considering austempering for your application? Contact our experts today to discuss your needs!