Graphite is widely used in high-temperature applications due to its excellent thermal and electrical conductivity, as well as its ability to withstand extreme temperatures. However, despite its advantages, there are several disadvantages to using graphite, particularly in applications like graphite furnaces. These drawbacks include its susceptibility to oxidation, brittleness, and potential contamination issues, which can limit its effectiveness in certain environments. Below, we explore these disadvantages in detail.
Key Points Explained:
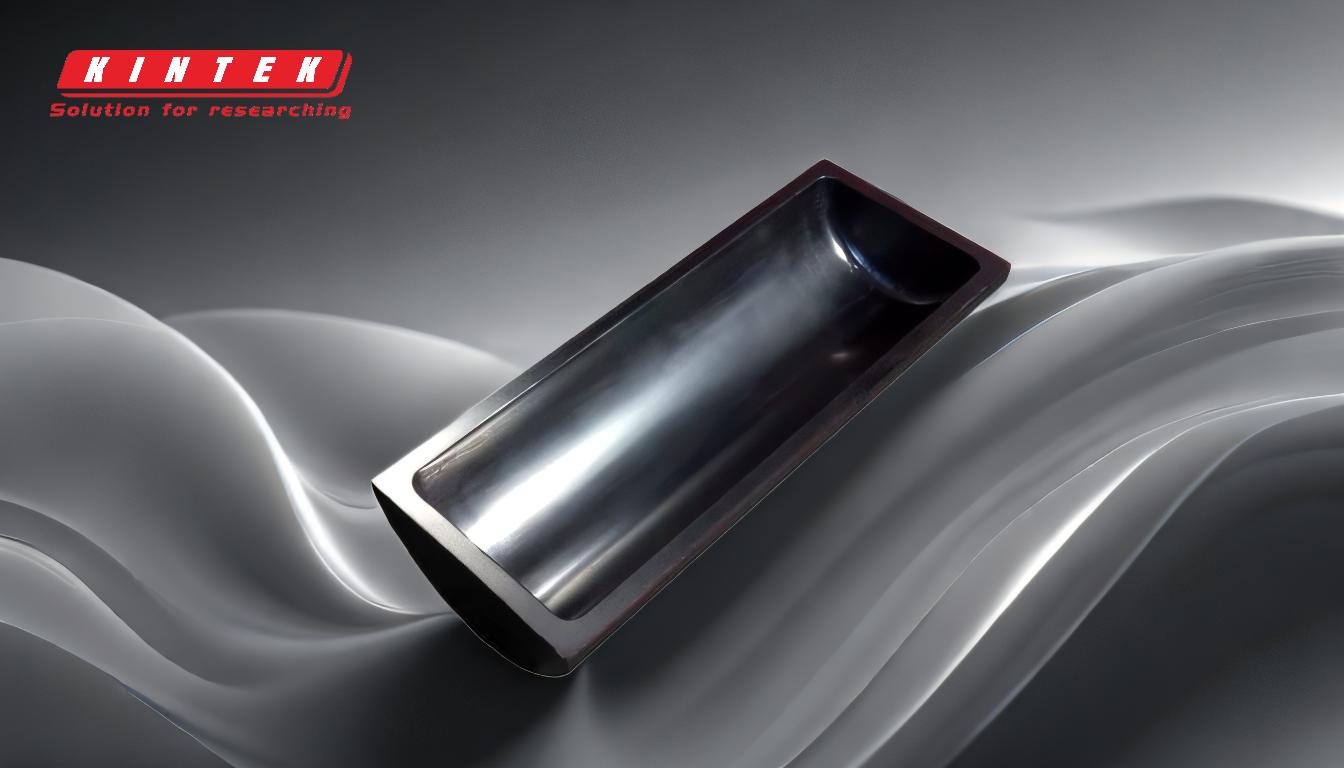
-
Susceptibility to Oxidation
- Graphite is prone to oxidation at high temperatures, especially in the presence of oxygen. This can lead to the formation of carbon monoxide or carbon dioxide, which degrades the material over time.
- In a graphite furnace, oxidation can reduce the lifespan of the heating elements and other graphite components, necessitating frequent replacements and increasing maintenance costs.
- To mitigate this issue, inert atmospheres (e.g., argon or nitrogen) are often required, which adds complexity and cost to the system.
-
Brittleness and Mechanical Weakness
- Graphite is inherently brittle, making it susceptible to cracking or breaking under mechanical stress or thermal shock.
- In high-temperature applications, rapid heating or cooling cycles can cause thermal expansion or contraction, leading to fractures in the graphite components.
- This brittleness limits its use in applications where mechanical durability is critical, such as in environments with frequent temperature fluctuations.
-
Contamination Risks
- Graphite can release fine particles or dust, especially when it undergoes wear or abrasion. These particles can contaminate the surrounding environment or the materials being processed in the furnace.
- In sensitive applications, such as semiconductor manufacturing or high-purity material processing, this contamination can be detrimental to product quality.
- Additionally, graphite can react with certain materials at high temperatures, leading to unwanted chemical reactions or impurities.
-
High Cost of High-Quality Graphite
- While graphite is generally cost-effective compared to some refractory materials, high-quality, high-purity graphite required for specialized applications can be expensive.
- The cost of maintaining a graphite furnace can also be high due to the need for inert atmospheres, regular replacements, and specialized handling to prevent contamination or damage.
-
Limited Use in Reactive Environments
- Graphite is not suitable for use in environments with reactive gases or chemicals, as it can react with substances like halogens, strong acids, or alkalis.
- This limitation restricts its application in certain industrial processes where such reactive conditions are present.
-
Energy Consumption
- While graphite furnaces are known for their fast heating speeds, they can also consume significant amounts of energy, especially when operating at very high temperatures.
- The need for inert atmospheres further increases energy consumption, as additional systems are required to maintain these conditions.
-
Difficulty in Machining and Handling
- Graphite is a soft material, which makes it challenging to machine with precision. It can also generate fine dust during machining, posing health and safety risks.
- Specialized tools and handling procedures are often required, adding to the overall cost and complexity of using graphite components.
In conclusion, while graphite offers several advantages, such as fast heating and high-temperature stability, its disadvantages—such as susceptibility to oxidation, brittleness, contamination risks, and high costs—must be carefully considered. These factors can significantly impact the performance, maintenance, and overall cost-effectiveness of systems like graphite furnaces. Understanding these limitations is crucial for making informed decisions when selecting materials for high-temperature applications.
Summary Table:
Disadvantage | Description |
---|---|
Susceptibility to Oxidation | Prone to oxidation at high temperatures, requiring inert atmospheres. |
Brittleness | Fragile under mechanical stress or thermal shock, limiting durability. |
Contamination Risks | Releases fine particles, risking contamination in sensitive applications. |
High Cost | High-quality graphite and maintenance costs for inert atmospheres are expensive. |
Reactive Environments | Unsuitable for use with reactive gases or chemicals. |
Energy Consumption | High energy usage, especially with inert atmosphere requirements. |
Machining Challenges | Difficult to machine, generating dust and requiring specialized tools. |
Need help choosing the right material for your high-temperature applications? Contact our experts today!