Sintering temperature plays a critical role in determining the microstructure and properties of materials. It influences grain size, porosity, density, and grain boundary distribution, which in turn affect the material's strength, durability, and hardness. Optimal sintering temperatures ensure a fully dense part with desired properties, while deviations (too high or too low) can lead to defects, degraded properties, or over-sintering. For example, zirconia achieves maximum strength at around 1500℃, with significant strength reductions at higher or lower temperatures. The sintering atmosphere also impacts the final properties, as it can prevent oxidation or reduce surface oxides.
Key Points Explained:
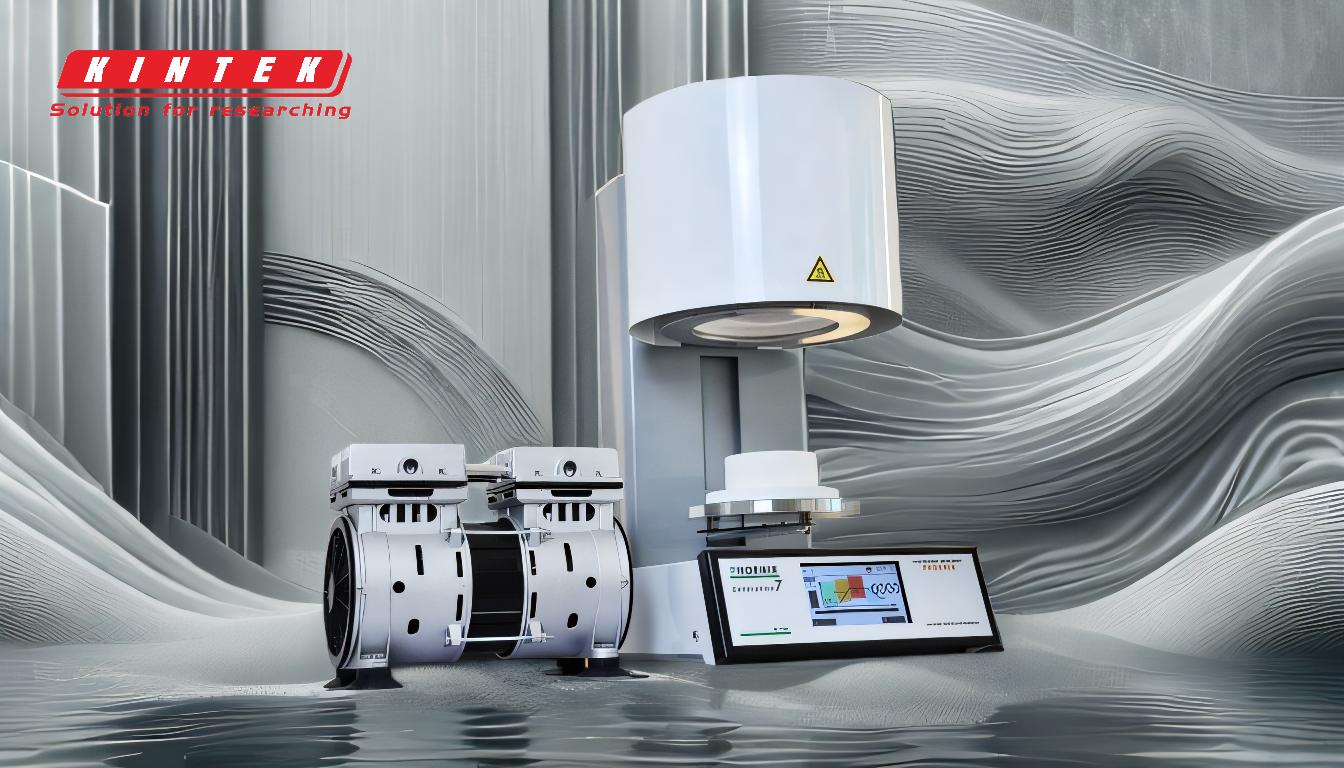
-
Grain Size and Microstructure:
- Sintering temperature directly affects grain size, pore size, and grain boundary distribution.
- Higher temperatures can lead to grain growth, which may reduce material strength due to larger grains.
- Optimal temperatures ensure a balanced microstructure, enhancing properties like strength and durability.
-
Porosity and Density:
- Sintering at the correct temperature ensures proper densification, reducing porosity and increasing density.
- Low sintering temperatures result in insufficient densification, leaving high porosity and degraded properties.
- Over-sintering (high temperatures or prolonged heating) can cause excessive grain growth and defects, reducing density and strength.
-
Material Strength and Hardness:
- Optimal sintering temperatures maximize material strength and hardness by achieving a fully dense and well-structured material.
- For example, zirconia exhibits maximum strength at around 1500℃. Deviations of ±150℃ can significantly reduce strength due to grain growth or insufficient sintering.
-
Crystallinity and Molecular Weight:
- Low sintering temperatures can lead to insufficient sintering, resulting in high crystallinity but poor molecular bonding.
- High sintering temperatures or prolonged heating can cause over-sintering, increasing crystallization enthalpy and reducing molecular weight, which degrades material properties.
-
Sintering Atmosphere:
- The atmosphere during sintering (e.g., reducing or inert) affects the final material properties.
- A reducing atmosphere prevents oxidation and allows the reduction of surface oxides, improving material integrity.
- The choice of atmosphere is crucial for achieving desired properties, especially in ceramics and metals.
-
Defects and Degradation:
- High sintering temperatures or long heating times can introduce defects such as cracks, voids, or excessive grain growth.
- Low temperatures or insufficient heating times result in incomplete sintering, leading to weak and brittle materials.
-
Optimal Sintering Conditions:
- Each material has an optimal sintering temperature and time range that maximizes its properties.
- Deviations from this range, even by small margins, can lead to significant reductions in performance.
- For example, zirconia's strength drops significantly at temperatures above or below 1500℃.
By carefully controlling sintering temperature, time, and atmosphere, manufacturers can achieve materials with the desired microstructure and properties, ensuring high performance in their intended applications.
Summary Table:
Aspect | Impact of Sintering Temperature |
---|---|
Grain Size | Higher temperatures cause grain growth, reducing strength; optimal temps ensure balanced growth. |
Porosity & Density | Correct temps reduce porosity and increase density; low temps leave high porosity. |
Strength & Hardness | Optimal temps maximize strength; deviations (e.g., zirconia at ±150℃) reduce performance. |
Crystallinity | Low temps lead to poor molecular bonding; high temps reduce molecular weight and degrade properties. |
Atmosphere | Reducing or inert atmospheres prevent oxidation, improving material integrity. |
Defects | High temps cause cracks or voids; low temps result in weak, brittle materials. |
Optimal Conditions | Each material has a specific temp range; deviations significantly reduce performance. |
Achieve the perfect sintering conditions for your materials—contact our experts today to learn more!