Chemical Vapor Deposition (CVD) is a versatile and widely used technique for depositing thin films and coatings onto substrates through chemical reactions between gaseous precursors and the heated surface of the substrate. The method is highly adaptable, with various techniques tailored to specific applications, temperature ranges, and substrate sensitivities. Examples of CVD methods include thermal CVD, plasma-enhanced CVD, and low-pressure CVD, among others. These methods are employed across industries for applications ranging from semiconductor manufacturing to the production of nanomaterials and pigments.
Key Points Explained:
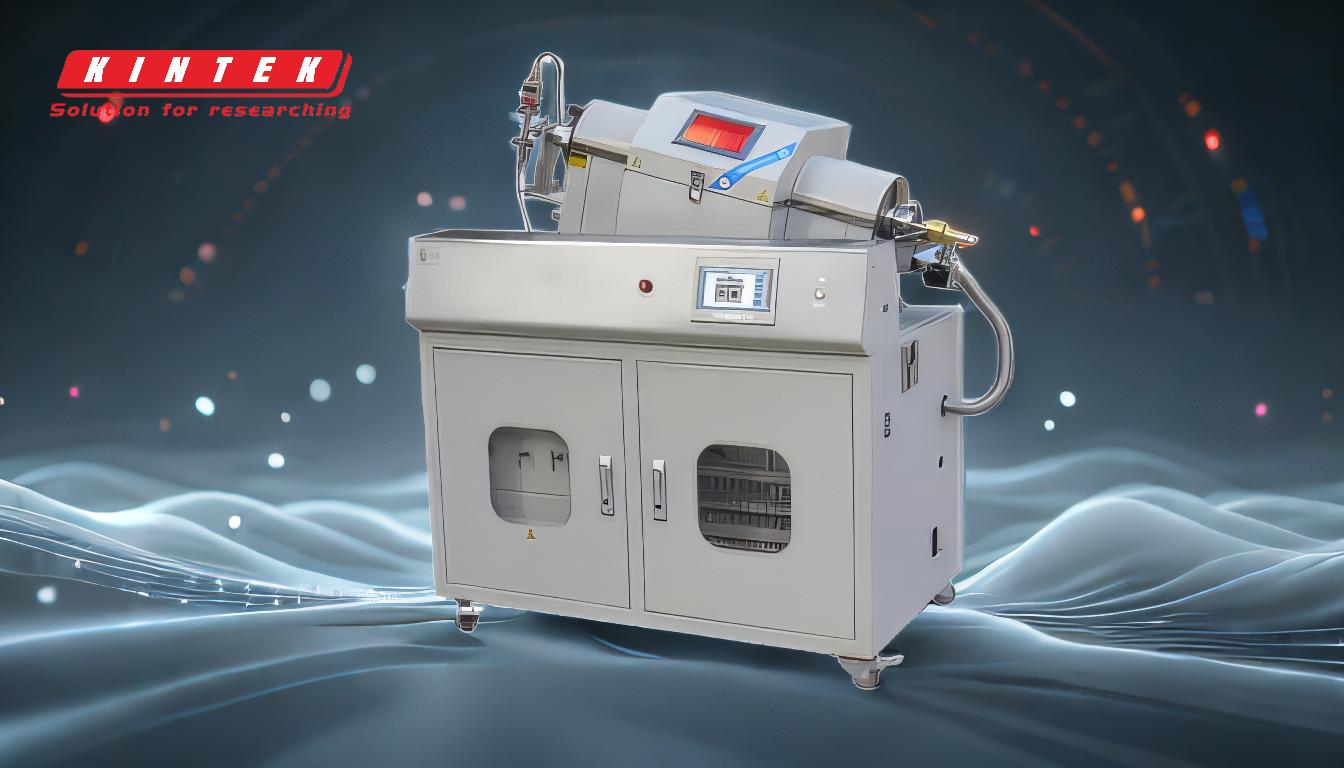
-
Thermal CVD
- Conducted at high or low temperatures, depending on the substrate and desired film properties.
- Can operate at atmospheric or reduced pressures.
- Suitable for applications requiring high-purity films, such as semiconductor manufacturing.
-
Plasma-Enhanced CVD (PECVD)
- Utilizes plasma to enable chemical reactions at lower temperatures, making it ideal for thermally sensitive substrates.
- Commonly used in the production of thin films for electronics and optics.
-
Low-Pressure CVD (LPCVD)
- Operates under reduced pressure to enhance film uniformity and reduce contamination.
- Often used in the fabrication of microelectronic devices.
-
Microwave Plasma CVD (MPCVD)
- Employs microwave-generated plasma to deposit high-quality diamond films.
- Widely used in the production of synthetic diamonds and advanced coatings.
-
Ultra-High Vacuum CVD (UHVCVD)
- Conducted in an ultra-high vacuum environment to achieve extremely pure and defect-free films.
- Ideal for advanced semiconductor and nanotechnology applications.
-
Aerosol-Assisted CVD
- Uses aerosolized precursors to deposit films, enabling the use of non-volatile or complex precursors.
- Applied in the production of nanomaterials and functional coatings.
-
Direct Liquid Injection CVD
- Involves the direct injection of liquid precursors into the reaction chamber.
- Suitable for depositing films with precise stoichiometry, such as in the production of complex oxides.
-
Remote Plasma-Enhanced CVD
- Separates the plasma generation from the deposition zone to reduce substrate damage.
- Used for depositing high-quality films on delicate substrates.
-
Hot Filament CVD
- Utilizes a heated filament to decompose gaseous precursors.
- Commonly employed in the synthesis of carbon-based materials like diamond films.
-
Applications of CVD
- Manufacturing of pigments (e.g., TiO2, SiO2, Al2O3, Si3N4, and carbon black powders).
- Production of nanosized and micron-sized materials for industrial use.
- Deposition of thin films for semiconductors, optics, and protective coatings.
By leveraging these diverse CVD techniques, industries can achieve precise control over film properties, enabling the development of advanced materials and technologies.
Summary Table:
CVD Method | Key Features | Applications |
---|---|---|
Thermal CVD | High/low temperatures, atmospheric/reduced pressures | High-purity films for semiconductors |
Plasma-Enhanced CVD (PECVD) | Lower temperatures, plasma-assisted reactions | Thin films for electronics and optics |
Low-Pressure CVD (LPCVD) | Reduced pressure for uniform films and reduced contamination | Microelectronic device fabrication |
Microwave Plasma CVD (MPCVD) | Microwave-generated plasma for high-quality diamond films | Synthetic diamonds, advanced coatings |
Ultra-High Vacuum CVD (UHVCVD) | Ultra-high vacuum for pure, defect-free films | Advanced semiconductors, nanotechnology |
Aerosol-Assisted CVD | Uses aerosolized precursors for non-volatile or complex precursors | Nanomaterials, functional coatings |
Direct Liquid Injection CVD | Direct injection of liquid precursors for precise stoichiometry | Complex oxide production |
Remote Plasma-Enhanced CVD | Separates plasma generation to reduce substrate damage | High-quality films on delicate substrates |
Hot Filament CVD | Heated filament to decompose precursors | Carbon-based materials like diamond films |
Need the right CVD method for your project? Contact our experts today for tailored solutions!