Induction heating is a highly efficient and rapid method of heating materials, where heat is generated internally within the object through electromagnetic induction. This process eliminates the need for external heat sources or direct contact, making it ideal for applications where contamination must be avoided. The system typically includes a solid-state RF power supply, an inductor (copper coil), and the workpiece. Factors influencing the efficiency and effectiveness of induction heating include the characteristics of the workpiece, the design of the inductor, the power supply capacity, and the required temperature change. Understanding these factors is crucial for optimizing the induction heating process for specific applications.
Key Points Explained:
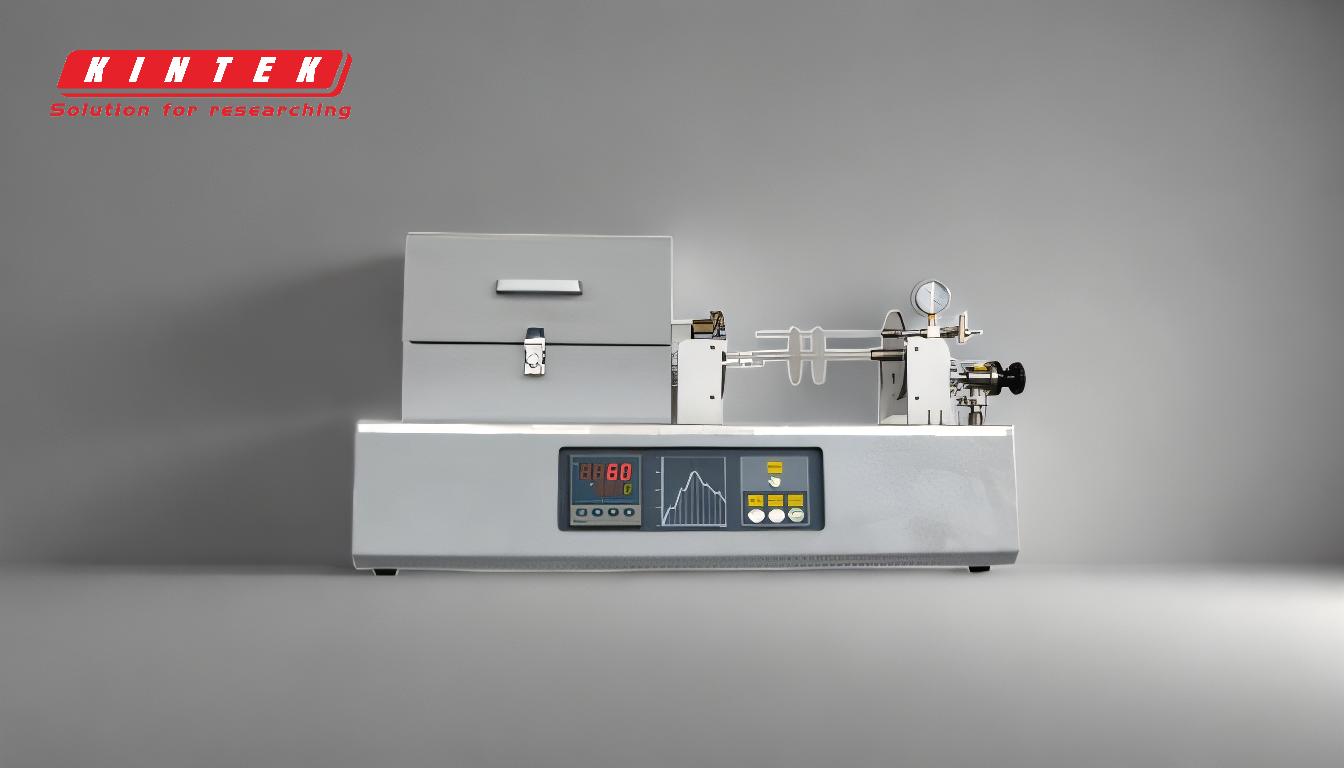
-
Internal Heat Generation:
- Induction heating generates heat directly within the workpiece through electromagnetic induction, rather than relying on external heat sources. This internal generation allows for rapid heating, which is particularly advantageous in industrial processes where speed is essential.
-
No External Contact:
- Since induction heating does not require direct contact between the heat source and the workpiece, it is ideal for applications where contamination must be minimized. This feature is particularly beneficial in industries like food processing, pharmaceuticals, and electronics manufacturing.
-
System Components:
- The primary components of an induction heating system include:
- Solid-State RF Power Supply: Provides the high-frequency alternating current necessary for induction heating.
- Inductor (Copper Coil): The coil generates the alternating magnetic field that induces eddy currents in the workpiece, leading to heating.
- Workpiece: The material to be heated, which must be electrically conductive for induction heating to work effectively.
- The primary components of an induction heating system include:
-
Factors Affecting Efficiency:
- The efficiency of induction heating is influenced by several key factors:
- Characteristics of the Workpiece: The material's electrical conductivity, magnetic permeability, and thermal properties significantly impact how effectively it can be heated.
- Inductor Design: The shape, size, and configuration of the inductor coil affect the distribution and intensity of the magnetic field, which in turn influences heating uniformity and efficiency.
- Power Supply Capacity: The power supply must be capable of delivering sufficient energy to achieve the desired temperature change within the workpiece.
- Required Temperature Change: The specific application's temperature requirements will dictate the necessary power and heating time, influencing overall system efficiency.
- The efficiency of induction heating is influenced by several key factors:
-
Applications and Benefits:
- Induction heating is widely used in various industries due to its rapid heating capabilities and contamination-free process. Common applications include metal hardening, brazing, annealing, and melting. The ability to precisely control heating also makes it suitable for delicate processes in electronics and medical device manufacturing.
By carefully considering these factors, users can optimize their induction heating systems for specific applications, ensuring efficient and effective heating processes.
Summary Table:
Factor | Description |
---|---|
Workpiece Characteristics | Electrical conductivity, magnetic permeability, and thermal properties of the material. |
Inductor Design | Shape, size, and configuration of the coil affecting magnetic field distribution. |
Power Supply Capacity | Energy delivery capability to achieve desired temperature changes. |
Required Temperature Change | Specific temperature requirements influencing power and heating time. |
Optimize your induction heating process today—contact our experts for tailored solutions!