The heat treatment of steel is a critical process that involves heating and cooling steel to alter its physical and mechanical properties. Factors affecting this process include the temperature, cooling rate, and the composition of the steel. Proper heat treatment can enhance the strength, hardness, and durability of steel, making it suitable for various industrial applications. Understanding these factors is essential for achieving the desired material properties and ensuring the quality of the final product.
Key Points Explained:
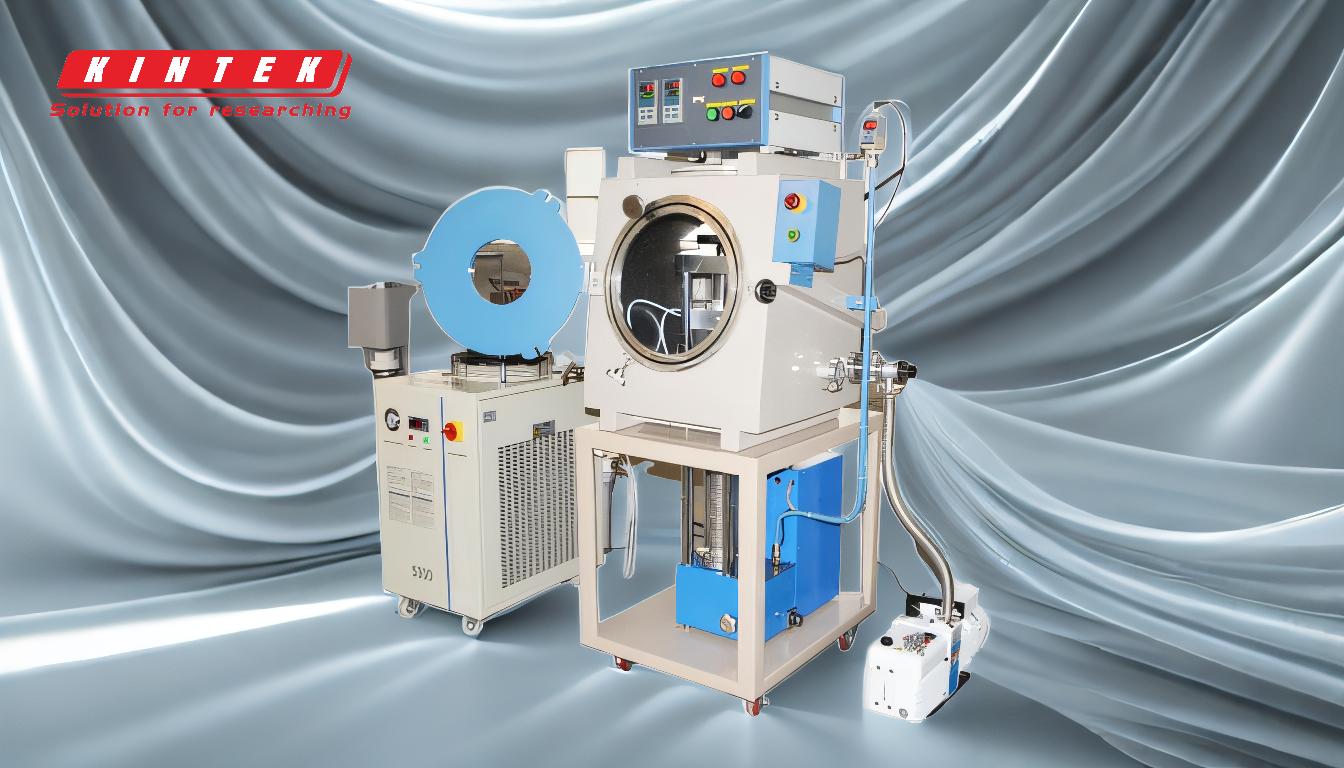
-
Temperature Control:
- The temperature at which steel is heated plays a crucial role in its heat treatment. Steel needs to be heated to specific temperatures to achieve the desired microstructure. For instance, heating steel to 2200° F (1200° C) makes it more ductile and malleable, allowing it to be shaped under pressure without cracking. This temperature is critical for processes like forging, where steel is permanently formed.
-
Cooling Rate:
- The rate at which steel is cooled after heating significantly affects its final properties. Rapid cooling, or quenching, can increase hardness but may also introduce brittleness. Conversely, slow cooling, or annealing, can improve ductility and reduce internal stresses. The cooling method (e.g., air cooling, oil quenching, or water quenching) must be carefully selected based on the desired outcome.
-
Steel Composition:
- The chemical composition of steel, including the presence of alloying elements like carbon, manganese, and chromium, influences its response to heat treatment. Different compositions require different heat treatment processes to achieve optimal properties. For example, high-carbon steels are typically harder but more brittle, while low-carbon steels are more ductile.
-
Heating Environment:
- The environment in which steel is heated can also affect the heat treatment process. For instance, heating in a controlled atmosphere or vacuum can prevent oxidation and decarburization, which can degrade the surface quality of the steel. Techniques like short path vacuum distillation can be used in specialized heat treatment processes to maintain a clean environment.
-
Stirring and Agitation:
- In some heat treatment processes, stirring or agitation of the heating medium (e.g., oil bath) can enhance uniformity in temperature distribution and improve the overall effectiveness of the treatment. This is particularly important in processes where precise temperature control is required.
-
Post-Treatment Processes:
- After heat treatment, additional processes such as tempering or stress relieving may be necessary to achieve the desired balance of hardness and toughness. These processes involve reheating the steel to a lower temperature and then cooling it slowly to reduce brittleness and improve machinability.
-
Material Purity:
- The presence of impurities or harmful heavy metals (e.g., zinc, copper, chromium, cadmium, lead, nickel, mercury, and arsenic) can negatively impact the heat treatment process and the final properties of the steel. Ensuring the purity of the steel is essential for achieving consistent and high-quality results.
By carefully controlling these factors, manufacturers can tailor the heat treatment process to produce steel with specific properties suited for various applications, from construction to aerospace. Understanding and optimizing these factors is key to achieving the desired material performance and longevity.
Summary Table:
Factor | Impact on Heat Treatment |
---|---|
Temperature Control | Determines microstructure; critical for processes like forging. |
Cooling Rate | Affects hardness and ductility; rapid cooling increases hardness, slow cooling improves ductility. |
Steel Composition | Influences response to heat treatment; alloying elements like carbon and chromium are key. |
Heating Environment | Controlled atmosphere prevents oxidation and decarburization, maintaining surface quality. |
Stirring and Agitation | Enhances temperature uniformity, improving treatment effectiveness. |
Post-Treatment | Processes like tempering reduce brittleness and improve machinability. |
Material Purity | Impurities can degrade properties; purity ensures consistent, high-quality results. |
Want to optimize your steel heat treatment process? Contact our experts today for tailored solutions!