Thin films are influenced by a variety of factors that span from the material properties to the deposition process and environmental conditions. These factors include substrate temperature, deposition parameters, material properties, microstructure, and post-deposition characteristics. Understanding these factors is crucial for optimizing the thin film's performance, adhesion, and functionality in applications such as electronics, optics, and coatings. Below, we explore the key factors in detail, providing insights into how each aspect impacts the final properties of thin films.
Key Points Explained:
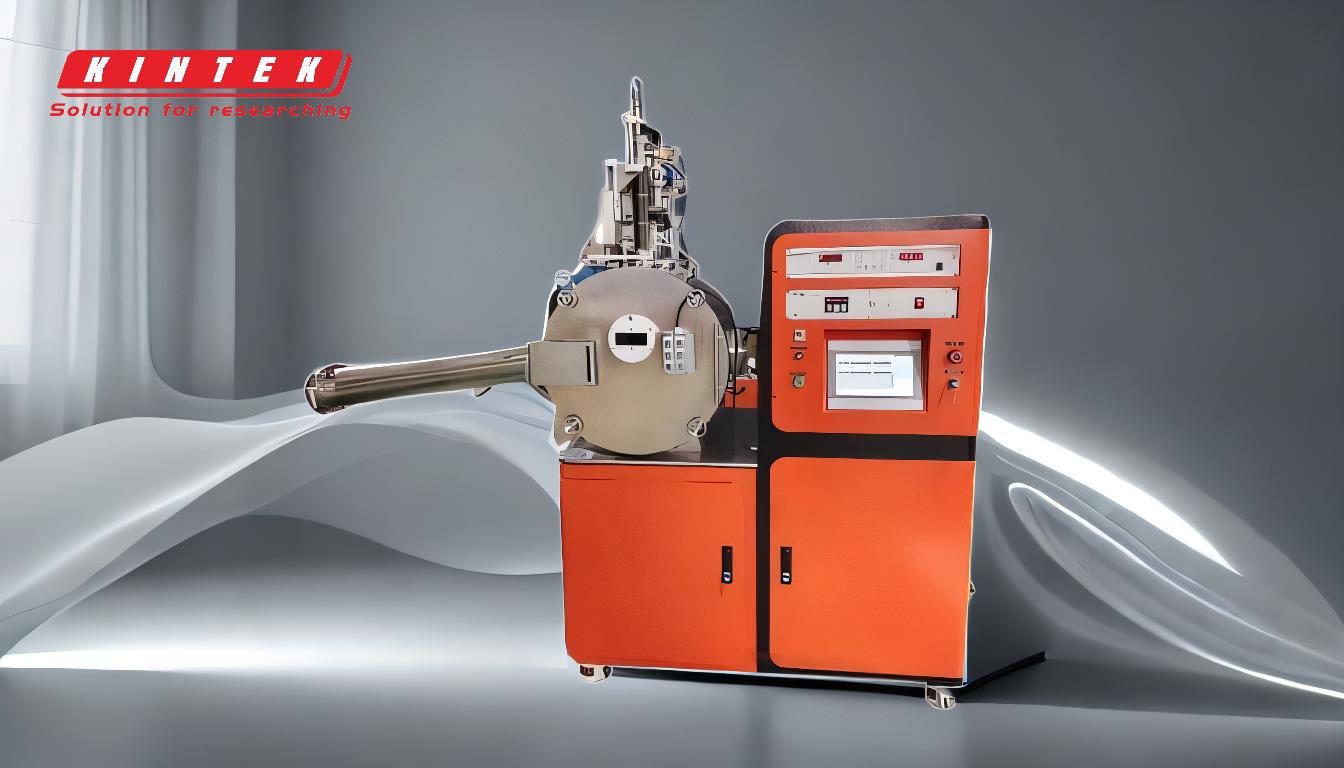
-
Substrate Temperature
- Substrate temperature plays a critical role in determining the quality and uniformity of thin films.
- Higher temperatures (above 150 °C) provide evaporated atoms with sufficient energy to move freely, leading to better film uniformity and improved adhesion to the substrate.
- Proper heating ensures that the film forms a strong bond with the substrate, which is essential for durability and performance.
-
Deposition Parameters
- The deposition process is influenced by factors such as:
- Deposition Temperature: Affects the energy of adatoms and their ability to form a uniform layer.
- Deposition Rate: A slower rate often results in higher-quality films with fewer defects.
- Residual Gas Composition: The presence of impurities in the vacuum chamber can alter the film's properties.
- These parameters must be carefully controlled to achieve the desired film characteristics.
- The deposition process is influenced by factors such as:
-
Material Properties
- The intrinsic properties of the material being deposited significantly impact the thin film's performance:
- Purity: Higher purity materials result in fewer defects and better electrical or optical properties.
- Melting/Boiling Points: Influence the deposition method and temperature requirements.
- Electrical Resistivity and Refractive Index: Critical for applications in electronics and optics.
- These properties must align with the intended application to ensure optimal functionality.
- The intrinsic properties of the material being deposited significantly impact the thin film's performance:
-
Microstructure and Surface Dynamics
- The microstructure of thin films is shaped by:
- Surface Mobility of Adatoms: Determines how atoms arrange themselves on the substrate.
- Re-sputtering and Shadowing: Can lead to uneven film growth or defects.
- Ion Implantation: Enhances film properties by embedding ions into the substrate.
- These processes affect the film's mechanical, electrical, and optical properties.
- The microstructure of thin films is shaped by:
-
Optical Properties
- Thin films used in optical applications are influenced by:
- Electrical Conductivity: Affects light absorption and reflection.
- Structural Defects: Voids, localized defects, and oxide bonds can scatter light and reduce transmission efficiency.
- Film Roughness and Thickness: Directly impact the reflection and transmission coefficients.
- These factors must be optimized to achieve the desired optical performance.
- Thin films used in optical applications are influenced by:
-
Quality Control and Manufacturing Considerations
- Practical factors such as:
- Client Specifications: Ensure the film meets specific application requirements.
- Cost and Efficiency: Balance between high-quality production and economic feasibility.
- Quality Control: Ensures consistency and reliability in the final product.
- These considerations are essential for successful thin film manufacturing.
- Practical factors such as:
-
Environmental and Process Conditions
- The environment during deposition, such as:
- Vacuum Conditions: Residual gases can introduce impurities or alter film properties.
- Substrate Nature: The material and surface condition of the substrate affect film adhesion and growth.
- These conditions must be carefully managed to achieve the desired film properties.
- The environment during deposition, such as:
By understanding and controlling these factors, manufacturers can optimize the deposition process to produce thin films with tailored properties for specific applications. Whether for electronics, optics, or protective coatings, the interplay of these factors determines the success of the final product.
Summary Table:
Factor | Impact on Thin Films |
---|---|
Substrate Temperature | Determines film uniformity and adhesion; higher temperatures improve bonding and quality. |
Deposition Parameters | Deposition rate, temperature, and residual gas composition affect film quality and defects. |
Material Properties | Purity, melting/boiling points, and electrical/optical properties influence functionality. |
Microstructure | Surface mobility, re-sputtering, and ion implantation shape mechanical and optical traits. |
Optical Properties | Conductivity, defects, and roughness impact light absorption, reflection, and transmission. |
Quality Control | Ensures consistency, reliability, and adherence to client specifications. |
Environmental Conditions | Vacuum conditions and substrate nature affect film adhesion and growth. |
Optimize your thin film production today—contact our experts for tailored solutions!