Heat treating operations are critical in modifying the mechanical, physical, and chemical properties of materials, but they are prone to failures if not executed properly. These failures can arise from improper surface preparation, incorrect temperature control, inadequate cooling rates, or contamination during the process. Such issues can lead to defects like coating peeling, bubbling, pitting, or variegation, as well as structural weaknesses, reduced durability, or inconsistent material properties. Understanding the common failures and their root causes is essential for ensuring the quality and reliability of heat-treated components.
Key Points Explained:
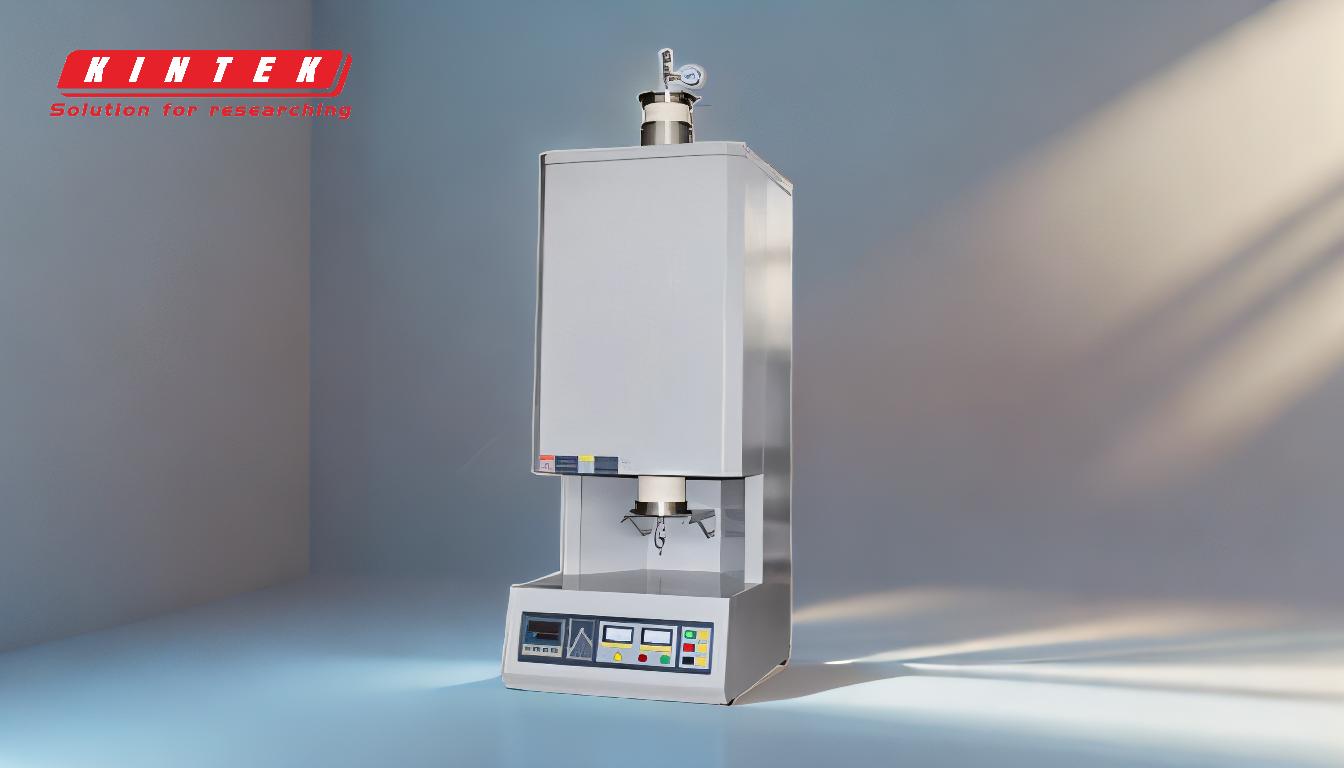
-
Improper Surface Preparation:
- Issue: Inadequate surface preparation before heat treatment can result in coating defects such as peeling, bubbling, pitting, and variegation.
- Cause: Rough or unrefined surfaces prevent the formation of strong, uniform, and anti-corrosive coatings.
- Solution: Ensure thorough cleaning, polishing, and surface refinement before heat treatment to achieve optimal adhesion and coating quality.
-
Temperature Control Failures:
- Issue: Incorrect temperature settings or fluctuations during heat treatment can lead to inconsistent material properties.
- Cause: Overheating or underheating can cause improper phase transformations, resulting in soft spots, brittleness, or uneven hardness.
- Solution: Use precise temperature control systems and regularly calibrate equipment to maintain consistent heating conditions.
-
Cooling Rate Mismanagement:
- Issue: Improper cooling rates can cause thermal stresses, warping, or cracking in the material.
- Cause: Rapid cooling (quenching) or slow cooling (annealing) must be carefully controlled to achieve the desired microstructure and mechanical properties.
- Solution: Select appropriate cooling mediums (e.g., oil, water, air) and monitor cooling rates to prevent defects.
-
Contamination During Heat Treatment:
- Issue: Contaminants such as oil, grease, or oxides on the material surface can lead to surface defects or uneven heat distribution.
- Cause: Contamination interferes with the heat transfer process and can cause localized overheating or underheating.
- Solution: Clean the material thoroughly before heat treatment and ensure a controlled atmosphere (e.g., inert gas or vacuum) to prevent contamination.
-
Inconsistent Material Properties:
- Issue: Variations in hardness, strength, or ductility across the material can occur due to uneven heat treatment.
- Cause: Non-uniform heating or cooling can result in inconsistent phase transformations and mechanical properties.
- Solution: Use uniform heating methods (e.g., induction heating) and ensure even cooling to achieve consistent results.
-
Stress Relief Failures:
- Issue: Improper stress relief can leave residual stresses in the material, leading to warping or cracking during machining or use.
- Cause: Inadequate heating or cooling during stress relief processes can fail to eliminate internal stresses.
- Solution: Follow precise stress relief protocols, including proper heating and slow cooling, to minimize residual stresses.
-
Case Hardening Defects:
- Issue: Inconsistent case depth or surface hardness can occur during case hardening processes like carburizing or nitriding.
- Cause: Uneven carbon or nitrogen diffusion can result from improper temperature control or insufficient process time.
- Solution: Monitor and control the diffusion process carefully to achieve uniform case depth and hardness.
-
Annealing Failures:
- Issue: Improper annealing can lead to excessive softening or insufficient stress relief in the material.
- Cause: Incorrect annealing temperatures or cooling rates can fail to achieve the desired microstructure.
- Solution: Follow specific annealing guidelines for the material and application to ensure proper softening and stress relief.
By addressing these common failures and implementing best practices, manufacturers can improve the quality and reliability of heat-treated components, ensuring they meet the required performance standards.
Summary Table:
Failure Type | Issue | Cause | Solution |
---|---|---|---|
Improper Surface Preparation | Coating defects (peeling, bubbling, pitting, variegation) | Rough or unrefined surfaces | Thorough cleaning, polishing, and surface refinement |
Temperature Control Failures | Inconsistent material properties | Overheating or underheating | Use precise temperature control systems and calibrate equipment |
Cooling Rate Mismanagement | Thermal stresses, warping, or cracking | Improper cooling rates | Select appropriate cooling mediums and monitor cooling rates |
Contamination | Surface defects or uneven heat distribution | Oil, grease, or oxides on the material surface | Clean thoroughly and use a controlled atmosphere |
Inconsistent Material Properties | Variations in hardness, strength, or ductility | Non-uniform heating or cooling | Use uniform heating methods and ensure even cooling |
Stress Relief Failures | Residual stresses causing warping or cracking | Inadequate heating or cooling during stress relief | Follow precise stress relief protocols with proper heating and slow cooling |
Case Hardening Defects | Inconsistent case depth or surface hardness | Uneven carbon or nitrogen diffusion | Monitor and control diffusion process carefully |
Annealing Failures | Excessive softening or insufficient stress relief | Incorrect annealing temperatures or cooling rates | Follow specific annealing guidelines |
Ensure your heat treatment processes are flawless—contact our experts today for tailored solutions!