Heat treatment of metals is a critical process used to alter their physical and mechanical properties, making them more suitable for specific applications. The five most common heat treatment methods are annealing, quenching, tempering, case hardening, and precipitation hardening. Each method serves a unique purpose, such as improving ductility, increasing hardness, or reducing internal stresses. These processes are widely used in industries like automotive, aerospace, and manufacturing to ensure metals meet the required performance standards. Below, we explore these five methods in detail, explaining their processes, benefits, and applications.
Key Points Explained:
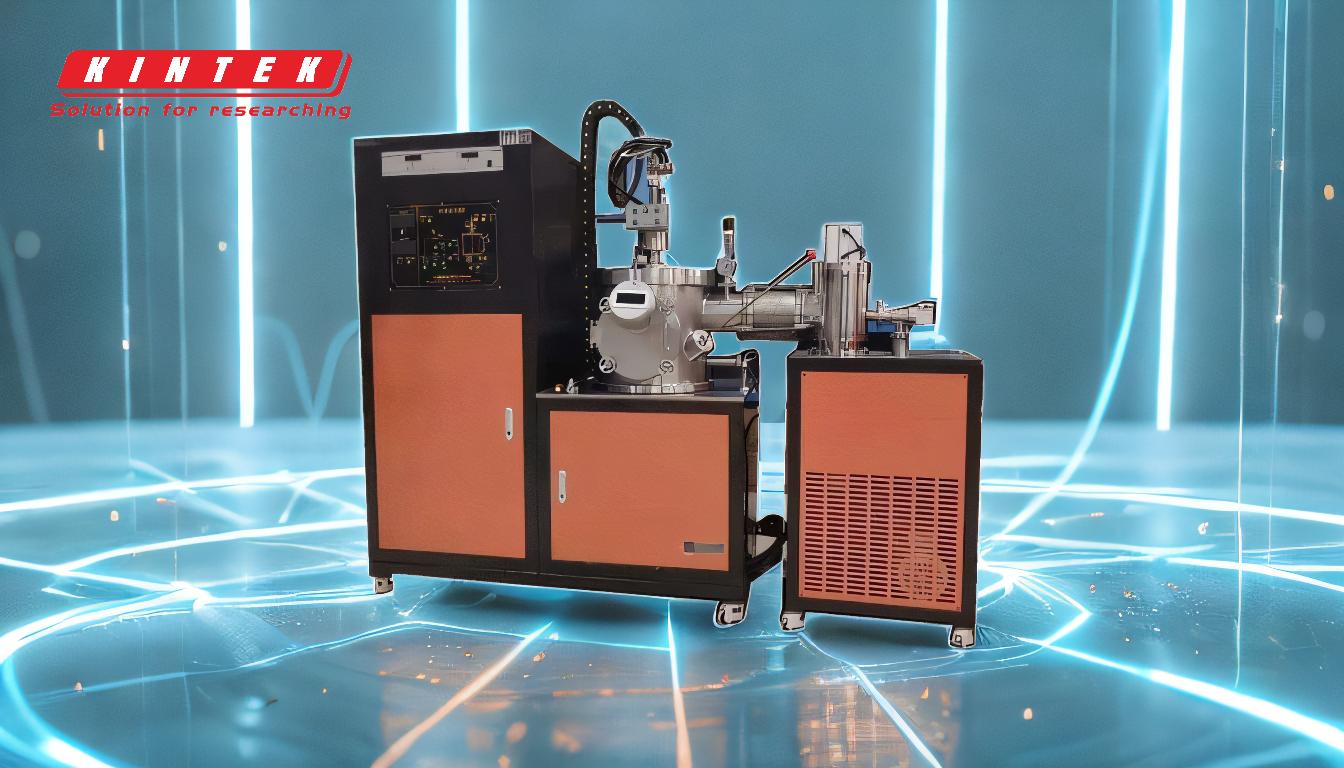
-
Annealing
- Process: Annealing involves heating the metal to a specific temperature, holding it at that temperature for a period, and then slowly cooling it. This process is typically done in a controlled environment to avoid oxidation.
- Purpose: The primary goal of annealing is to soften the metal, improve its ductility, and reduce internal stresses. It also refines the grain structure, making the metal more workable.
- Applications: Annealing is commonly used for metals like steel, copper, and aluminum, especially in applications where the metal needs to be shaped or formed without cracking.
-
Quenching
- Process: Quenching involves heating the metal to a high temperature and then rapidly cooling it by immersing it in a quenching medium such as water, oil, or air.
- Purpose: This process increases the hardness and strength of the metal by creating a martensitic structure, which is very hard but brittle.
- Applications: Quenching is widely used in the production of tools, gears, and components that require high surface hardness and wear resistance.
-
Tempering
- Process: Tempering is performed after quenching. The metal is reheated to a temperature below its critical point and then cooled at a controlled rate.
- Purpose: Tempering reduces the brittleness caused by quenching while maintaining a significant portion of the metal's hardness. It also improves toughness and ductility.
- Applications: This process is essential for components like springs, cutting tools, and structural parts that need a balance of hardness and toughness.
-
Case Hardening
- Process: Case hardening involves adding carbon or nitrogen to the surface layer of the metal while keeping the core relatively soft. Techniques like carburizing and nitriding are commonly used.
- Purpose: The goal is to create a hard, wear-resistant surface while maintaining a tough and ductile core.
- Applications: Case hardening is ideal for components like gears, camshafts, and bearings, where surface wear resistance is critical.
-
Precipitation Hardening
- Process: Precipitation hardening, also known as age hardening, involves heating the metal to a specific temperature to form precipitates within the metal matrix, followed by controlled cooling.
- Purpose: This process increases the strength and hardness of the metal by creating a fine dispersion of precipitates that impede dislocation movement.
- Applications: It is commonly used for alloys like aluminum, magnesium, and certain stainless steels, particularly in aerospace and high-performance applications.
Each of these heat treatment methods plays a vital role in tailoring the properties of metals to meet specific industrial requirements. By understanding these processes, purchasers and manufacturers can make informed decisions about which treatment is best suited for their needs.
Summary Table:
Method | Process | Purpose | Applications |
---|---|---|---|
Annealing | Heat to a specific temperature, hold, then slowly cool. | Soften metal, improve ductility, reduce internal stresses. | Steel, copper, aluminum for shaping or forming without cracking. |
Quenching | Heat to high temperature, then rapidly cool in water, oil, or air. | Increase hardness and strength by creating a martensitic structure. | Tools, gears, components requiring high surface hardness and wear resistance. |
Tempering | Reheat after quenching to below critical temperature, then cool slowly. | Reduce brittleness, maintain hardness, improve toughness and ductility. | Springs, cutting tools, structural parts needing hardness-toughness balance. |
Case Hardening | Add carbon or nitrogen to the surface layer, keeping the core soft. | Create a hard, wear-resistant surface with a tough, ductile core. | Gears, camshafts, bearings requiring surface wear resistance. |
Precipitation Hardening | Heat to form precipitates, then cool controlled. | Increase strength and hardness by creating fine precipitates. | Aluminum, magnesium, stainless steels for aerospace and high-performance uses. |
Need help selecting the right heat treatment for your metals? Contact our experts today for tailored solutions!