Heat treatment processes for metals are essential for enhancing their mechanical, physical, and chemical properties to meet specific application requirements. These processes involve controlled heating and cooling to achieve desired outcomes such as increased hardness, improved ductility, enhanced strength, or better resistance to wear and corrosion. Heat treatment is widely used in industries ranging from automotive and aerospace to construction and manufacturing, ensuring that metals perform optimally under various conditions. The primary goals include relieving internal stresses, refining grain structure, and improving machinability or workability.
Key Points Explained:
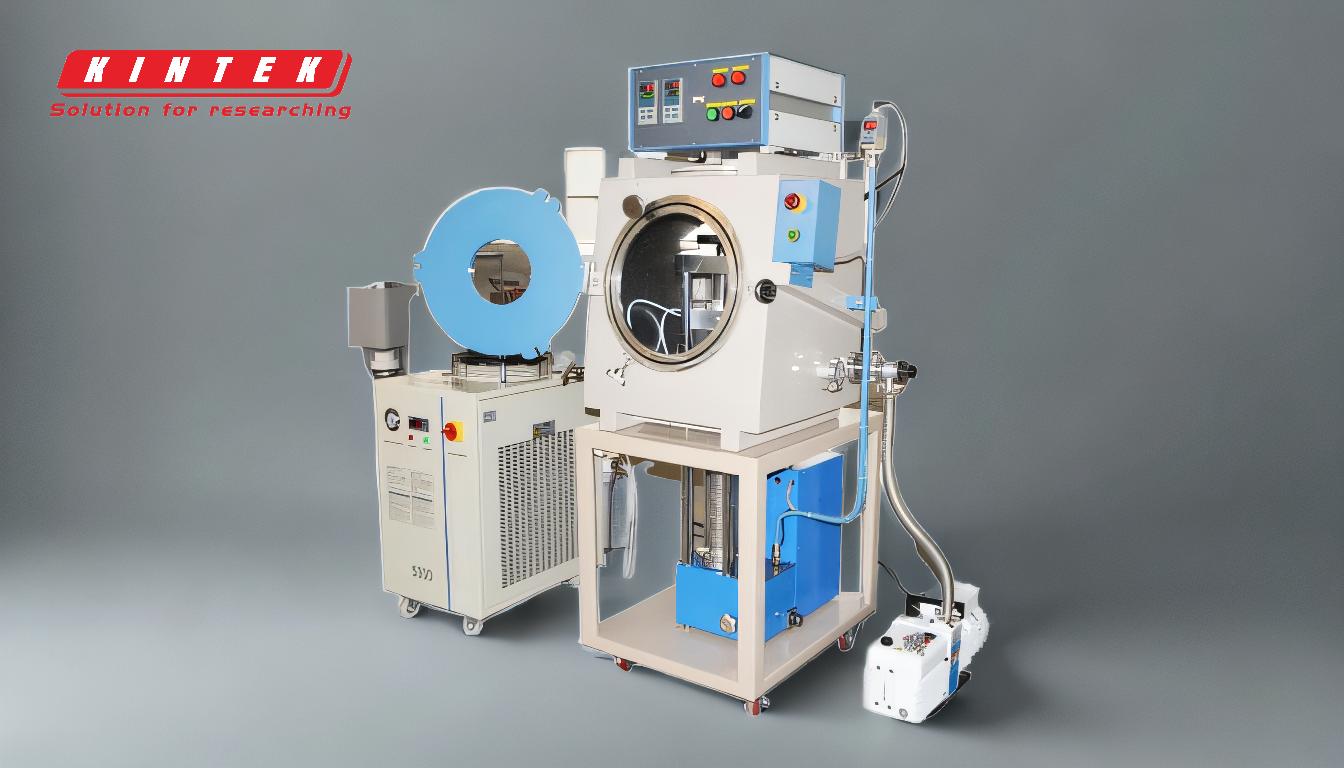
-
Purpose of Heat Treatment
Heat treatment is carried out to modify the properties of metals, making them suitable for specific applications. The processes are designed to:- Relieve internal stresses induced during fabrication, such as during casting or welding.
- Improve mechanical properties like hardness, toughness, and tensile strength.
- Enhance wear resistance, corrosion resistance, and thermal stability.
- Refine grain structure to achieve uniformity and improve machinability.
-
Common Heat Treatment Processes
Several heat treatment techniques are employed depending on the desired outcome:- Annealing: This process involves heating the metal to a specific temperature and then slowly cooling it to soften the material, relieve internal stresses, and improve ductility. It is particularly useful after cold working or casting.
- Quenching: Rapid cooling of the metal after heating to increase hardness and strength. However, quenching can make the metal brittle, so it is often followed by tempering.
- Tempering: After quenching, tempering involves reheating the metal to a lower temperature to reduce brittleness while maintaining hardness and strength.
- Normalizing: Similar to annealing but with faster cooling, normalizing refines the grain structure and improves mechanical properties.
- Case Hardening: This process hardens the surface of the metal while keeping the core soft and ductile, enhancing wear resistance.
-
Applications of Heat Treatment
Heat treatment is critical in various industries:- Automotive: Enhances the durability and performance of engine components, gears, and axles.
- Aerospace: Improves the strength-to-weight ratio of materials used in aircraft structures and engines.
- Construction: Increases the load-bearing capacity and longevity of structural steel.
- Manufacturing: Ensures tools and machinery parts can withstand high stress and wear.
-
Benefits of Heat Treatment
The advantages of heat treatment include:- Improved material properties tailored to specific applications.
- Extended lifespan of components by enhancing wear and corrosion resistance.
- Reduced material waste by optimizing the use of metals.
- Cost savings through improved efficiency and reduced maintenance.
-
Considerations for Heat Treatment
When selecting a heat treatment process, factors to consider include:- The type of metal and its composition.
- The desired mechanical and physical properties.
- The operating environment and stress conditions the metal will face.
- The cost and feasibility of the process.
By understanding and applying the appropriate heat treatment processes, manufacturers can ensure that metals meet the required specifications and perform reliably in their intended applications.
Summary Table:
Process | Purpose | Applications |
---|---|---|
Annealing | Softens metal, relieves stress, improves ductility | Post-casting, cold working |
Quenching | Increases hardness and strength | Tools, gears, engine components |
Tempering | Reduces brittleness while maintaining hardness | Structural steel, machinery parts |
Normalizing | Refines grain structure, improves mechanical properties | Automotive, aerospace components |
Case Hardening | Hardens surface while keeping core soft and ductile | Wear-resistant parts, tools |
Optimize your metal components with the right heat treatment—contact our experts today for tailored solutions!