Hot isostatic pressing (HIP) is a highly effective manufacturing process used in various industries, including aerospace, automotive, and ceramics, to improve material properties and produce high-density components. However, it comes with several limitations, such as lower surface accuracy, higher material and tooling costs, and slower production rates compared to other methods like extrusion or die compaction. These limitations often necessitate additional machining and can make the process less economical for certain applications. Despite these drawbacks, HIP offers significant advantages in terms of material performance and defect elimination, making it indispensable in high-end manufacturing.
Key Points Explained:
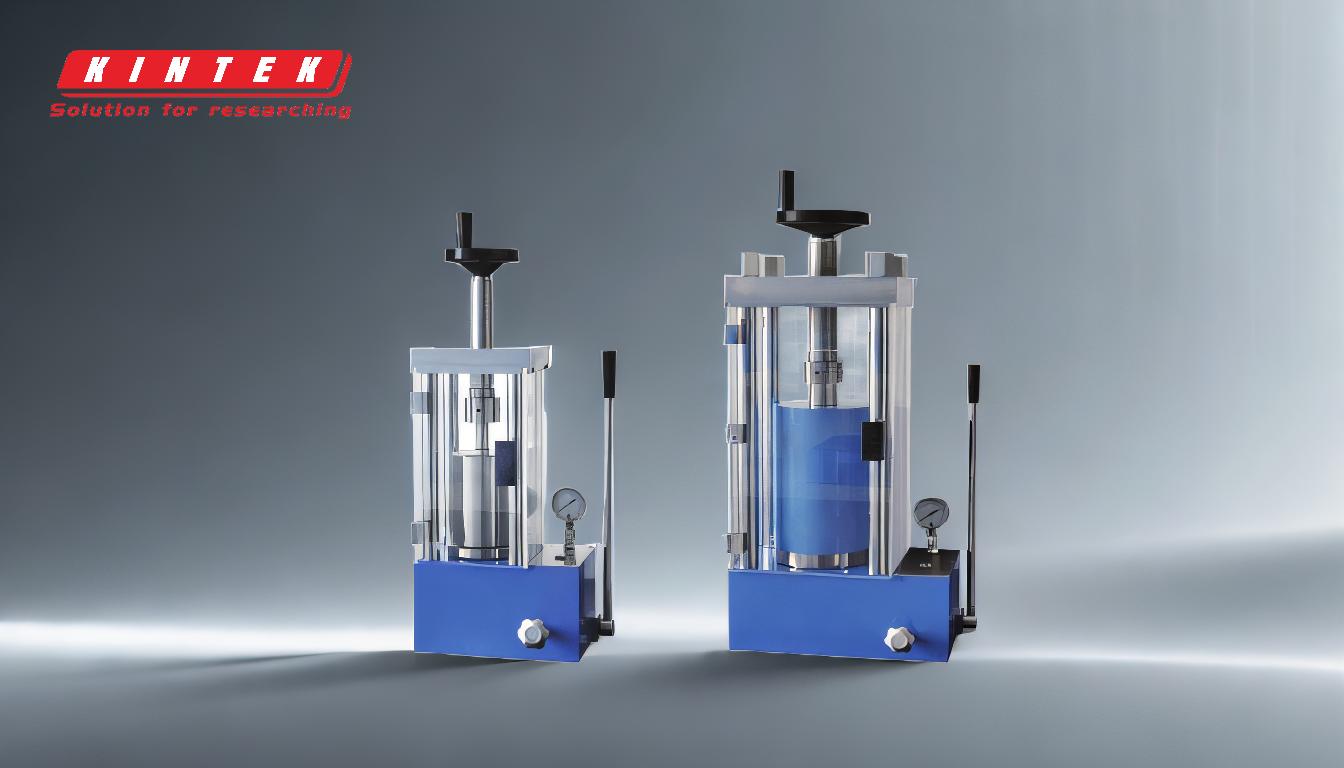
-
Lower Surface Accuracy:
- Hot isostatic pressing involves the use of flexible bags to apply uniform pressure, which can lead to lower accuracy on surfaces adjacent to these bags. This is in contrast to mechanical pressing or extrusion, which can achieve higher precision.
- As a result, components produced via HIP often require subsequent machining to achieve the desired dimensional accuracy and surface finish. This additional step can increase production time and costs.
-
Higher Material Costs:
- The process typically requires the use of relatively expensive spray-dried powder, especially for fully automatic dry bag presses. This can make the overall cost of materials higher compared to other pressing methods.
- The need for high-quality powders is essential to ensure uniform compaction and achieve the desired material properties, but it adds to the financial burden.
-
Lower Production Rates:
- HIP generally has lower production rates compared to extrusion or die compaction. The process is slower due to the need for precise control of temperature and pressure, as well as the time required for the isostatic pressing cycle.
- This limitation can make HIP less suitable for high-volume production where speed is a critical factor.
-
Higher Tooling Costs and Process Complexity:
- Both hot and warm isostatic press methods involve higher tooling costs and greater process complexity compared to simpler techniques like uniaxial pressing.
- The equipment used in HIP is sophisticated and requires significant investment, which can be a barrier for smaller manufacturers or those with limited budgets.
-
Limited Applicability for Certain Materials:
- While HIP is highly effective for metals, ceramics, and composites, it may not be the best choice for all materials. For example, some plastics or low-melting-point materials may not withstand the high temperatures and pressures involved in the process.
- This limitation restricts the range of materials that can be effectively processed using HIP.
-
Energy Consumption and Environmental Impact:
- The HIP process requires substantial energy input to achieve the necessary high temperatures and pressures. This can lead to higher operational costs and a larger environmental footprint.
- Manufacturers need to consider the energy efficiency and sustainability of the process, especially in industries where environmental impact is a significant concern.
In summary, while hot isostatic pressing offers numerous advantages, such as improved material properties and the ability to produce high-density components, it also comes with several limitations. These include lower surface accuracy, higher material and tooling costs, slower production rates, and greater process complexity. Understanding these limitations is crucial for manufacturers to make informed decisions about when and how to use HIP in their production processes.
Summary Table:
Limitation | Description |
---|---|
Lower Surface Accuracy | Requires additional machining due to flexible bag use, increasing time and costs. |
Higher Material Costs | Expensive spray-dried powder needed for uniform compaction. |
Lower Production Rates | Slower than extrusion or die compaction, unsuitable for high-volume production. |
Higher Tooling Costs | Sophisticated equipment and process complexity increase investment requirements. |
Limited Material Applicability | Not suitable for plastics or low-melting-point materials. |
Energy Consumption | High energy input leads to higher operational costs and environmental impact. |
Want to learn more about overcoming HIP limitations? Contact our experts today for tailored solutions!