The annealing process, while widely used in metallurgy and materials science to improve the properties of metals and alloys, has several limitations. These include constraints related to temperature control, time requirements, material-specific challenges, energy consumption, and potential for surface oxidation. Additionally, the process may not always achieve the desired material properties due to microstructural complexities or improper parameter selection. Understanding these limitations is crucial for optimizing the annealing process and ensuring the desired outcomes for specific applications.
Key Points Explained:
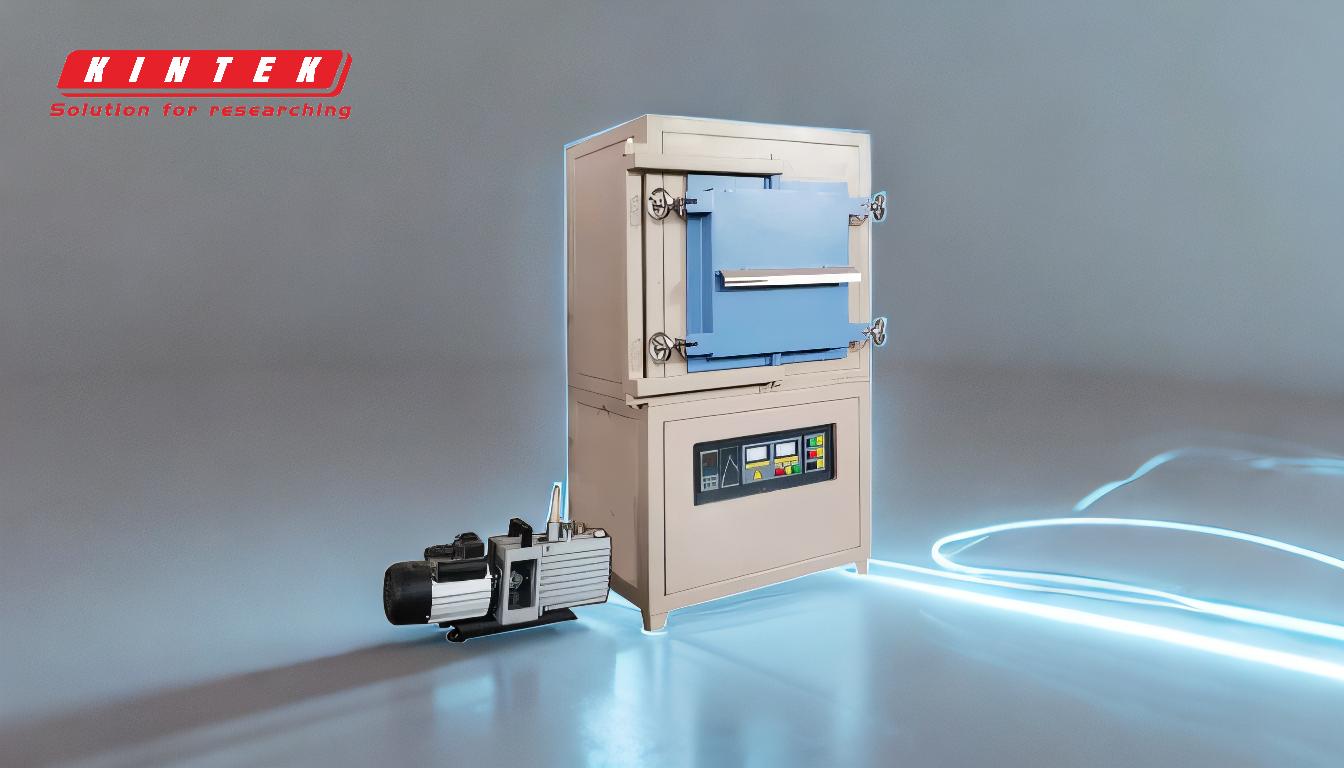
-
Temperature Control Challenges:
- Precision Requirements: Annealing requires precise temperature control to achieve the desired material properties. Slight deviations can lead to incomplete recrystallization or grain growth issues.
- Equipment Limitations: Not all furnaces can maintain uniform temperatures across large or complex workpieces, leading to inconsistent results.
- Material Sensitivity: Some materials, such as high-carbon steels or certain alloys, have narrow temperature ranges for effective annealing, making the process more challenging.
-
Time Constraints:
- Long Processing Times: Annealing often requires prolonged heating and cooling cycles, which can be time-consuming and inefficient for high-volume production.
- Cooling Rate Sensitivity: Slow cooling rates are necessary for some materials to avoid internal stresses, but this can further extend processing times.
-
Material-Specific Limitations:
- Non-Uniform Microstructures: Materials with heterogeneous compositions or prior processing histories may not respond uniformly to annealing.
- Grain Growth Issues: Over-annealing can lead to excessive grain growth, reducing material strength and toughness.
- Limited Applicability: Some materials, such as non-metallic composites or ceramics, do not benefit significantly from annealing.
-
Energy Consumption:
- High Energy Requirements: Maintaining high temperatures for extended periods consumes significant energy, making the process costly and less environmentally friendly.
- Inefficiency in Batch Processing: Batch annealing, while common, is less energy-efficient compared to continuous annealing processes.
-
Surface Oxidation and Decarburization:
- Oxidation Risks: Exposure to high temperatures in the presence of oxygen can lead to surface oxidation, degrading material quality.
- Decarburization: In steels, prolonged heating can cause carbon loss from the surface, reducing hardness and wear resistance.
-
Process Complexity and Skill Requirements:
- Parameter Optimization: Selecting the correct annealing temperature, time, and cooling rate requires expertise and experimentation.
- Post-Annealing Treatments: Additional processes, such as quenching or tempering, may be needed to achieve the desired properties, adding complexity.
-
Economic and Practical Constraints:
- Cost of Equipment: High-quality annealing furnaces and temperature control systems can be expensive to purchase and maintain.
- Space Requirements: Large-scale annealing operations require significant floor space, which may not be feasible for smaller facilities.
-
Inconsistent Results:
- Variability in Material Response: Even with controlled parameters, variations in material composition or prior processing can lead to inconsistent outcomes.
- Human Error: Manual control of annealing processes increases the risk of errors, such as incorrect temperature settings or timing.
-
Limited Improvement for Certain Properties:
- Hardness and Strength Trade-offs: Annealing often reduces hardness and strength to improve ductility, which may not be desirable for all applications.
- Limited Impact on Defects: While annealing can reduce internal stresses, it may not eliminate all defects, such as voids or inclusions.
-
Environmental and Safety Concerns:
- Heat and Emissions: High-temperature processes generate heat and emissions, requiring proper ventilation and safety measures.
- Worker Safety: Handling hot materials and operating high-temperature equipment pose safety risks.
By understanding these limitations, manufacturers and engineers can better design annealing processes, select appropriate materials, and implement complementary treatments to achieve optimal results.
Summary Table:
Limitation Category | Key Challenges |
---|---|
Temperature Control | Precision requirements, equipment limitations, material sensitivity |
Time Constraints | Long processing times, cooling rate sensitivity |
Material-Specific Issues | Non-uniform microstructures, grain growth, limited applicability |
Energy Consumption | High energy requirements, inefficiency in batch processing |
Surface Oxidation | Oxidation risks, decarburization in steels |
Process Complexity | Parameter optimization, post-annealing treatments |
Economic Constraints | Cost of equipment, space requirements |
Inconsistent Results | Variability in material response, human error |
Limited Property Improvement | Hardness-strength trade-offs, limited defect elimination |
Environmental Concerns | Heat and emissions, worker safety risks |
Need help optimizing your annealing process? Contact our experts today for tailored solutions!