Sintering is a highly advantageous process in material manufacturing, particularly in powder metallurgy, due to its ability to enhance material properties and improve production efficiency. It involves the application of heat and pressure to compact powdered materials without melting them, resulting in dense, strong, and durable products. Key benefits include reduced porosity, enhanced mechanical strength, improved electrical and thermal conductivity, and the ability to work with difficult-to-process materials. Additionally, sintering is a sustainable process that minimizes waste and allows for precise control over material properties, making it ideal for producing high-quality, consistent products.
Key Points Explained:
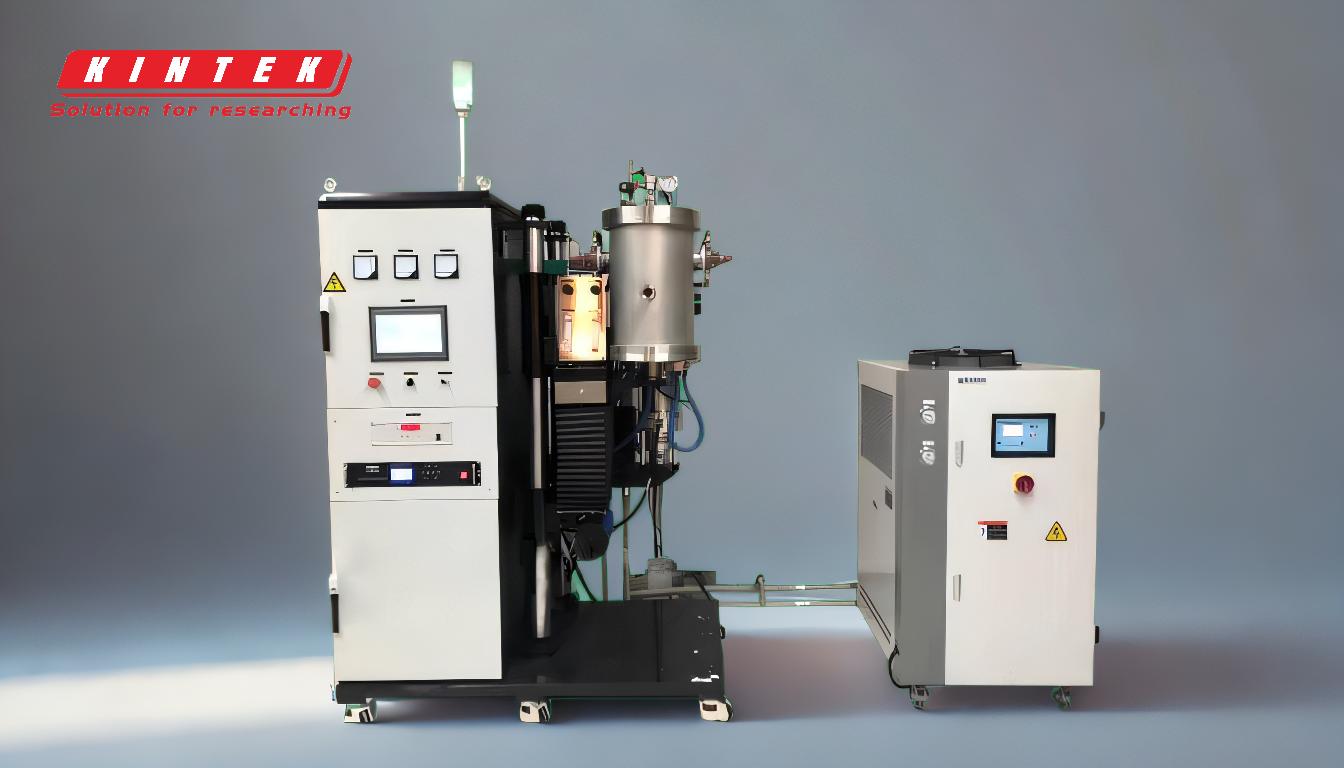
-
Enhanced Material Properties
- Sintering significantly improves the strength, durability, and conductivity of materials. By reducing porosity and creating sintered necks between particles, the process enhances the mechanical and electrical properties of the final product. This is particularly beneficial for applications requiring high-performance materials, such as turbine blades or electrical components.
-
Control Over Manufacturing Process
- The sintering process allows for precise control over grain size, porosity, and material composition. This results in highly repeatable operations and consistent product quality. The ability to create nearly net-shaped objects also reduces the need for additional machining, saving time and resources.
-
Sustainability and Waste Reduction
- Sintering is an eco-friendly process that produces minimal waste compared to traditional metalworking methods. By using powdered materials and avoiding melting, it conserves energy and reduces material loss, making it a sustainable choice for modern manufacturing.
-
Ability to Work with Difficult Materials
- Sintering is particularly useful for materials with high melting points or complex compositions, such as refractory metals and ceramics. The process enables the production of dense, strong materials that are difficult or impossible to achieve through melting and casting.
-
Improved Mechanical Handling Strength
- The sintering process strengthens materials by developing sintered necks between particles, which reduces pores and increases overall strength. This makes the final product more durable and capable of withstanding mechanical stress.
-
Uniformity and Purity
- Sintering ensures high levels of purity and uniformity in the starting materials, leading to consistent and reliable end products. The absence of binding contacts or inclusions between powder particles further enhances the material's quality.
-
Versatility in Applications
- Sintering is widely used in various industries, including aerospace, automotive, and electronics, due to its ability to produce complex shapes and high-strength components. Its versatility makes it a valuable process for manufacturing a wide range of products.
By leveraging these advantages, sintering has become a cornerstone of modern material manufacturing, offering a cost-effective, sustainable, and efficient solution for producing high-quality materials.
Summary Table:
Advantage | Description |
---|---|
Enhanced Material Properties | Improves strength, durability, and conductivity by reducing porosity. |
Control Over Manufacturing Process | Precise control over grain size, porosity, and material composition. |
Sustainability and Waste Reduction | Eco-friendly process with minimal waste and energy conservation. |
Ability to Work with Difficult Materials | Enables production of dense, strong materials with high melting points. |
Improved Mechanical Handling Strength | Strengthens materials by reducing pores and increasing durability. |
Uniformity and Purity | Ensures high levels of purity and uniformity in final products. |
Versatility in Applications | Widely used in aerospace, automotive, and electronics industries. |
Unlock the full potential of sintering for your manufacturing needs—contact our experts today!