A direct core-type induction furnace, while highly efficient and suitable for high-throughput operations, has several significant drawbacks. These include the need for continuous maintenance of the metal loop, the inability to refine charge materials, and the requirement for charge materials to be free of oxides and of known composition. Additionally, the furnace is rarely allowed to cool, which can complicate operations and maintenance. These factors make it less flexible for operations requiring frequent alloy changes or those involving materials with varying compositions.
Key Points Explained:
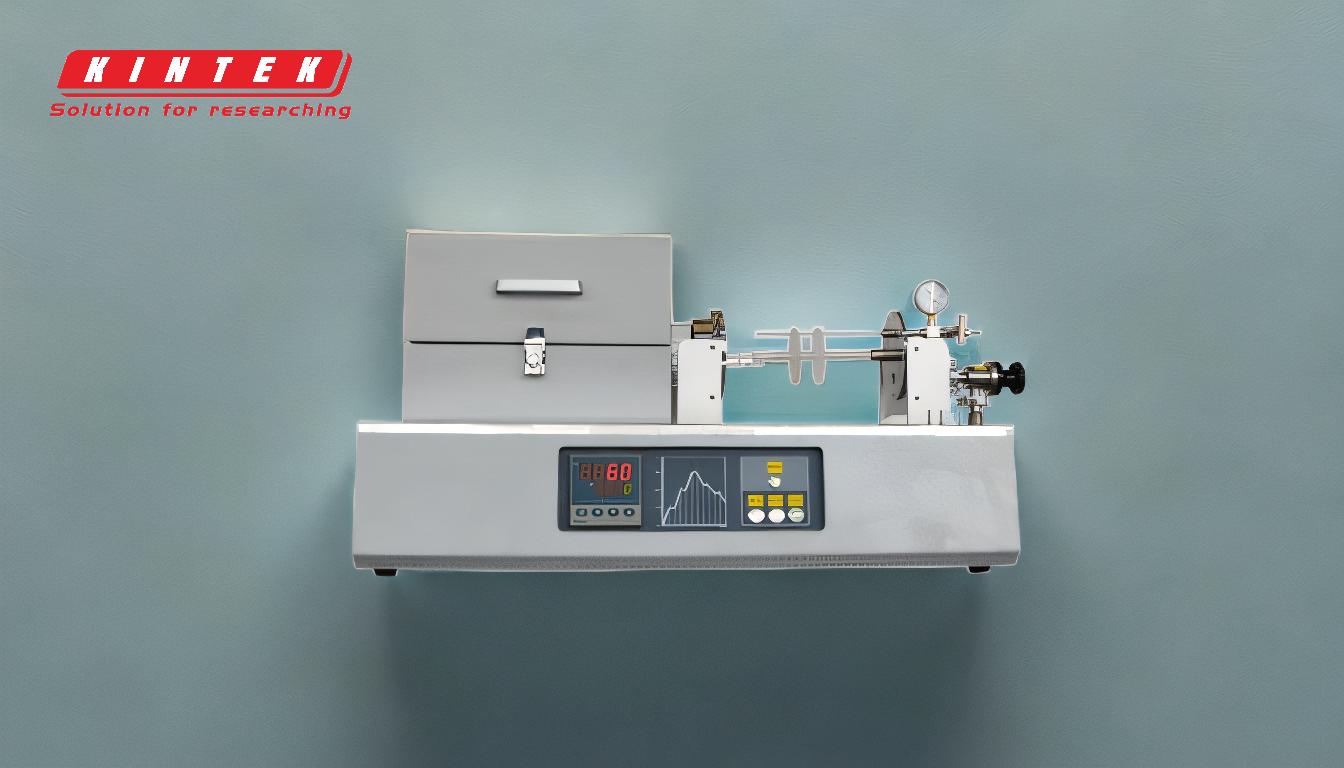
-
Continuous Maintenance of the Metal Loop:
- The direct core-type induction furnace requires ongoing maintenance to ensure the metal loop remains intact and functional. This continuous upkeep can be labor-intensive and may lead to increased operational costs over time.
-
Lack of Refining Capacity:
- Unlike some other types of furnaces, the direct core-type induction furnace does not have the capability to refine charge materials. This means that the materials used must already be free of oxides and have a known composition, limiting the types of materials that can be processed.
-
Oxidation and Alloying Element Loss:
- During the melting process, some alloying elements may be lost due to oxidation. This necessitates the re-addition of these elements to the melt, which can complicate the process and increase material costs.
-
Inability to Cool Down:
- The furnace is rarely allowed to cool, which can complicate operations and maintenance. This continuous operation can lead to wear and tear on the furnace components, potentially reducing the overall lifespan of the equipment.
-
Limited Flexibility for Alloy Changes:
- The direct core-type induction furnace is not well-suited for operations that require frequent alloy changes. This lack of flexibility can be a significant drawback for facilities that need to process a variety of materials with different compositions.
-
High Initial and Operational Costs:
- While the furnace is efficient, the initial setup and ongoing maintenance costs can be high. This includes the cost of maintaining the metal loop and the need for high-quality, oxide-free charge materials.
-
Complexity in Operation:
- The requirement for continuous operation and the need for precise control over the charge materials can make the operation of a direct core-type induction furnace more complex compared to other types of furnaces.
In summary, while the direct core-type induction furnace offers high efficiency and is suitable for high-throughput operations, its drawbacks, including the need for continuous maintenance, lack of refining capacity, and limited flexibility for alloy changes, make it less ideal for certain applications. These factors should be carefully considered when selecting a furnace for specific industrial needs.
Summary Table:
Drawback | Explanation |
---|---|
Continuous Maintenance of Metal Loop | Requires ongoing upkeep, increasing labor and operational costs. |
Lack of Refining Capacity | Cannot refine charge materials; materials must be oxide-free and of known composition. |
Oxidation and Alloying Element Loss | Alloying elements may oxidize, requiring re-addition and increasing material costs. |
Inability to Cool Down | Rarely allowed to cool, complicating operations and maintenance. |
Limited Flexibility for Alloy Changes | Not ideal for frequent alloy changes or materials with varying compositions. |
High Initial and Operational Costs | High setup and maintenance costs, including metal loop upkeep and material quality. |
Complexity in Operation | Continuous operation and precise material control make it more complex to operate. |
Considering a furnace for your operations? Contact our experts today to find the best solution for your needs!