Heat treatment of metals is a critical process used to alter the physical and sometimes chemical properties of a material. The primary goal is to improve the metal's hardness, strength, toughness, ductility, and resistance to wear and corrosion. Various methods of heat treatment are employed depending on the desired outcome and the type of metal being treated. These methods include annealing, normalizing, hardening, tempering, case hardening, and surface hardening. Each method involves heating the metal to a specific temperature, holding it at that temperature for a certain period, and then cooling it at a controlled rate. The choice of method depends on the metal's composition, the intended application, and the properties that need to be enhanced.
Key Points Explained:
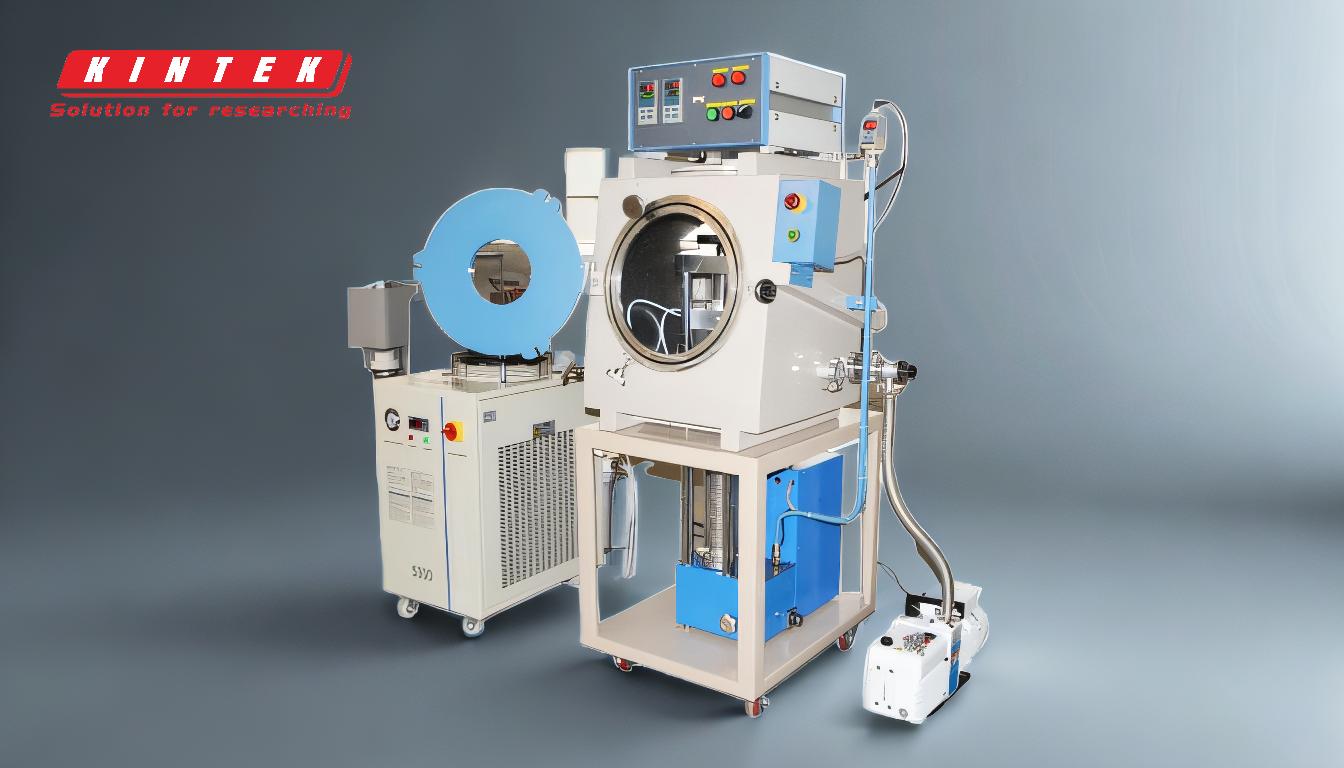
-
Annealing:
- Process: Annealing involves heating the metal to a specific temperature, holding it there for a period, and then slowly cooling it, usually in a furnace.
- Purpose: This process is used to soften the metal, improve its ductility, and relieve internal stresses. It also refines the grain structure, making the metal more uniform.
- Applications: Annealing is commonly used for steels, copper, and aluminum to prepare them for further processing like machining or cold working.
-
Normalizing:
- Process: Normalizing is similar to annealing but involves cooling the metal in air rather than in a furnace.
- Purpose: This method refines the grain structure and improves the mechanical properties of the metal, such as toughness and strength.
- Applications: Normalizing is often used for carbon steels to achieve a more uniform structure and better machinability.
-
Hardening:
- Process: Hardening involves heating the metal to a high temperature and then rapidly cooling it, usually by quenching in water, oil, or air.
- Purpose: This process increases the hardness and strength of the metal but can also make it more brittle.
- Applications: Hardening is used for tools, gears, and other components that require high wear resistance.
-
Tempering:
- Process: Tempering is performed after hardening and involves reheating the metal to a lower temperature and then cooling it.
- Purpose: This process reduces the brittleness caused by hardening while maintaining the increased hardness and strength.
- Applications: Tempering is essential for tools and components that need to be both hard and tough, such as springs and cutting tools.
-
Case Hardening:
- Process: Case hardening involves adding carbon or nitrogen to the surface of the metal and then heat treating it to create a hard outer layer while keeping the core soft and tough.
- Purpose: This method increases the wear resistance of the surface while maintaining the ductility and toughness of the core.
- Applications: Case hardening is used for gears, bearings, and other components that require a hard surface and a tough core.
-
Surface Hardening:
- Process: Surface hardening, such as induction hardening, involves heating only the surface of the metal to a high temperature and then rapidly cooling it.
- Purpose: This process hardens the surface while keeping the core relatively soft, improving wear resistance without compromising the overall toughness.
- Applications: Induction hardening is suitable for larger parts and localized areas that need to be wear-resistant, such as crankshafts and camshafts.
-
Vacuum Heat Treatment:
- Process: This involves heat treating metals in a vacuum to prevent oxidation and contamination. It includes processes like vacuum sintering, vacuum brazing, and vacuum quenching.
- Purpose: Vacuum heat treatment provides a clean environment, improving the metal's surface finish and mechanical properties.
- Applications: This method is used for high-precision components, aerospace parts, and materials that require a high degree of purity and surface quality.
Each of these heat treatment methods has specific applications and benefits, making them essential techniques in metallurgy and manufacturing. The choice of method depends on the metal type, the desired properties, and the intended use of the final product.
Summary Table:
Method | Process | Purpose | Applications |
---|---|---|---|
Annealing | Heat, hold, and slowly cool in a furnace | Softens metal, improves ductility, relieves stress, refines grain structure | Steels, copper, aluminum for machining or cold working |
Normalizing | Heat and cool in air | Refines grain structure, improves toughness and strength | Carbon steels for uniform structure and machinability |
Hardening | Heat to high temperature, then rapidly cool (quench) | Increases hardness and strength, may increase brittleness | Tools, gears, and components requiring high wear resistance |
Tempering | Reheat after hardening to a lower temperature, then cool | Reduces brittleness while maintaining hardness and strength | Springs, cutting tools, and components needing hardness and toughness |
Case Hardening | Add carbon/nitrogen to surface, then heat treat | Creates hard outer layer with a tough core | Gears, bearings, and components requiring a hard surface and tough core |
Surface Hardening | Heat only the surface, then rapidly cool | Hardens surface while keeping core soft | Crankshafts, camshafts, and localized wear-resistant areas |
Vacuum Heat Treatment | Heat treat in a vacuum to prevent oxidation and contamination | Improves surface finish and mechanical properties | High-precision components, aerospace parts, and materials requiring purity |
Need help choosing the right heat treatment method for your metals? Contact our experts today!