Graphene, a single layer of carbon atoms arranged in a hexagonal lattice, can be produced using several methods, each with its own advantages and limitations. The primary methods include mechanical exfoliation, liquid-phase exfoliation, reduction of graphene oxide, sublimation of silicon carbide (SiC), and chemical vapor deposition (CVD). These methods can be broadly categorized into "top-down" approaches, which involve breaking down graphite into graphene layers, and "bottom-up" approaches, which build graphene layers atom by atom. Among these, CVD is considered the most promising for producing large-area, high-quality graphene, while mechanical exfoliation is often used for fundamental research due to its simplicity and ability to produce high-quality samples.
Key Points Explained:
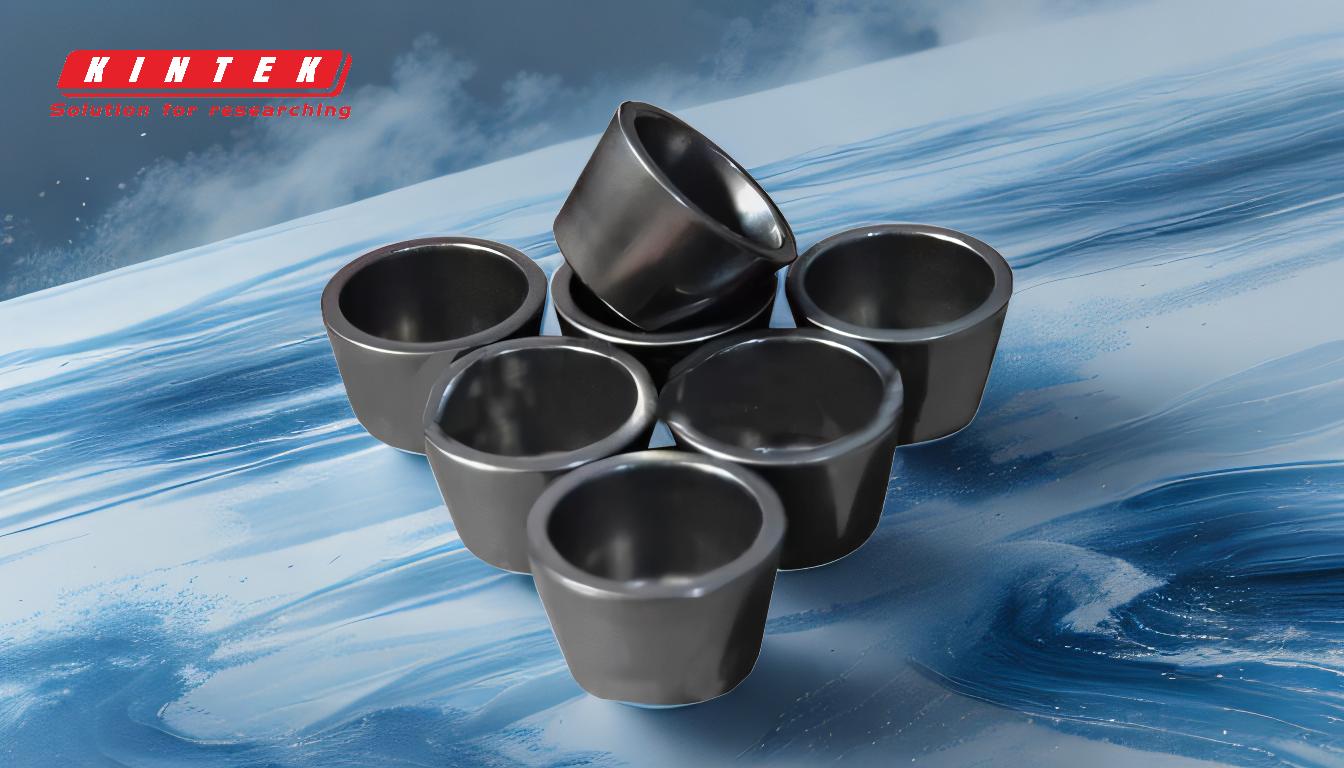
-
Mechanical Exfoliation (Top-Down Method):
- Process: This method involves peeling off layers of graphene from graphite using adhesive tape or other mechanical means. The process is simple and can produce high-quality graphene flakes.
- Applications: Primarily used in fundamental research and laboratory settings due to the small size and low yield of the graphene produced.
-
Advantages:
- Produces high-quality graphene with minimal defects.
- Simple and cost-effective for small-scale production.
-
Disadvantages:
- Not suitable for large-scale production.
- Low yield and inconsistent flake sizes.
-
Liquid-Phase Exfoliation (Top-Down Method):
- Process: Graphite is dispersed in a liquid medium and subjected to ultrasonic treatment or shear forces to exfoliate the graphene layers.
- Applications: Suitable for mass production, particularly in applications where electrical quality is not the primary concern, such as composites or coatings.
-
Advantages:
- Scalable and capable of producing large quantities of graphene.
- Can be used to produce graphene in various solvents, allowing for functionalization.
-
Disadvantages:
- Graphene produced often has lower electrical quality due to defects and impurities.
- Requires post-processing to remove solvents and impurities.
-
Reduction of Graphene Oxide (Top-Down Method):
- Process: Graphene oxide (GO) is first produced by oxidizing graphite, and then reduced to graphene using chemical or thermal methods.
- Applications: Commonly used in applications where cost and scalability are more important than electrical quality, such as in energy storage devices or sensors.
-
Advantages:
- Scalable and cost-effective.
- Can produce graphene with a large surface area.
-
Disadvantages:
- The reduction process often leaves residual oxygen groups, leading to lower electrical conductivity.
- Graphene produced may have structural defects.
-
Sublimation of Silicon Carbide (SiC) (Bottom-Up Method):
- Process: Silicon carbide is heated to high temperatures, causing the silicon atoms to sublimate and leaving behind a layer of graphene on the surface.
- Applications: Used in high-performance electronic applications where high-quality graphene is required.
-
Advantages:
- Produces high-quality, single-crystal graphene.
- Suitable for electronic applications due to its excellent electrical properties.
-
Disadvantages:
- High cost due to the expensive SiC substrate and the need for high-temperature processing.
- Limited scalability compared to other methods.
-
Chemical Vapor Deposition (CVD) (Bottom-Up Method):
- Process: A hydrocarbon gas is decomposed at high temperatures on a metal substrate (e.g., copper or nickel), forming a layer of graphene.
- Applications: The most promising method for producing large-area, high-quality graphene, suitable for electronic devices, transparent conductive films, and other high-tech applications.
-
Advantages:
- Produces large-area, high-quality graphene with minimal defects.
- Scalable and suitable for industrial production.
-
Disadvantages:
- Requires precise control of temperature, pressure, and gas flow rates.
- The need for a metal substrate adds to the cost and complexity of the process.
-
Comparison of Methods:
- Top-Down vs. Bottom-Up: Top-down methods (e.g., mechanical exfoliation, liquid-phase exfoliation) are generally simpler and more cost-effective but are limited in terms of scalability and quality. Bottom-up methods (e.g., CVD, SiC sublimation) offer better control over the quality and properties of graphene but are more complex and expensive.
- Quality vs. Scalability: Mechanical exfoliation and CVD produce the highest quality graphene but are limited in scalability. Liquid-phase exfoliation and reduction of graphene oxide are more scalable but produce lower-quality graphene.
In conclusion, the choice of graphene production method depends on the intended application, with each method offering a unique balance of quality, scalability, and cost. CVD stands out as the most promising method for producing large-area, high-quality graphene, making it the preferred choice for industrial applications.
Summary Table:
Method | Type | Key Advantages | Limitations | Applications |
---|---|---|---|---|
Mechanical Exfoliation | Top-Down | High-quality, simple, cost-effective | Low yield, not scalable | Fundamental research |
Liquid-Phase Exfoliation | Top-Down | Scalable, functionalization possible | Lower electrical quality | Composites, coatings |
Reduction of Graphene Oxide | Top-Down | Scalable, cost-effective | Residual defects, lower conductivity | Energy storage, sensors |
SiC Sublimation | Bottom-Up | High-quality, single-crystal graphene | High cost, limited scalability | High-performance electronics |
Chemical Vapor Deposition (CVD) | Bottom-Up | Large-area, high-quality, scalable | Complex, expensive | Electronics, transparent conductive films |
Want to learn more about graphene production methods? Contact our experts today for tailored advice!