PVD (Physical Vapor Deposition) coating is a versatile and widely used technique for applying thin films to various substrates. It involves the physical transfer of material from a source to a substrate in a vacuum environment. The methods of PVD coating vary based on the specific techniques used to vaporize and deposit the material. These methods include thermal evaporation, sputter deposition, ion plating, electron beam evaporation, and plasma sputter deposition. Each method has unique characteristics, advantages, and applications, making PVD coating suitable for industries such as electronics, optics, automotive, and aerospace. The choice of method depends on factors like the material being coated, the desired film properties, and the application requirements.
Key Points Explained:
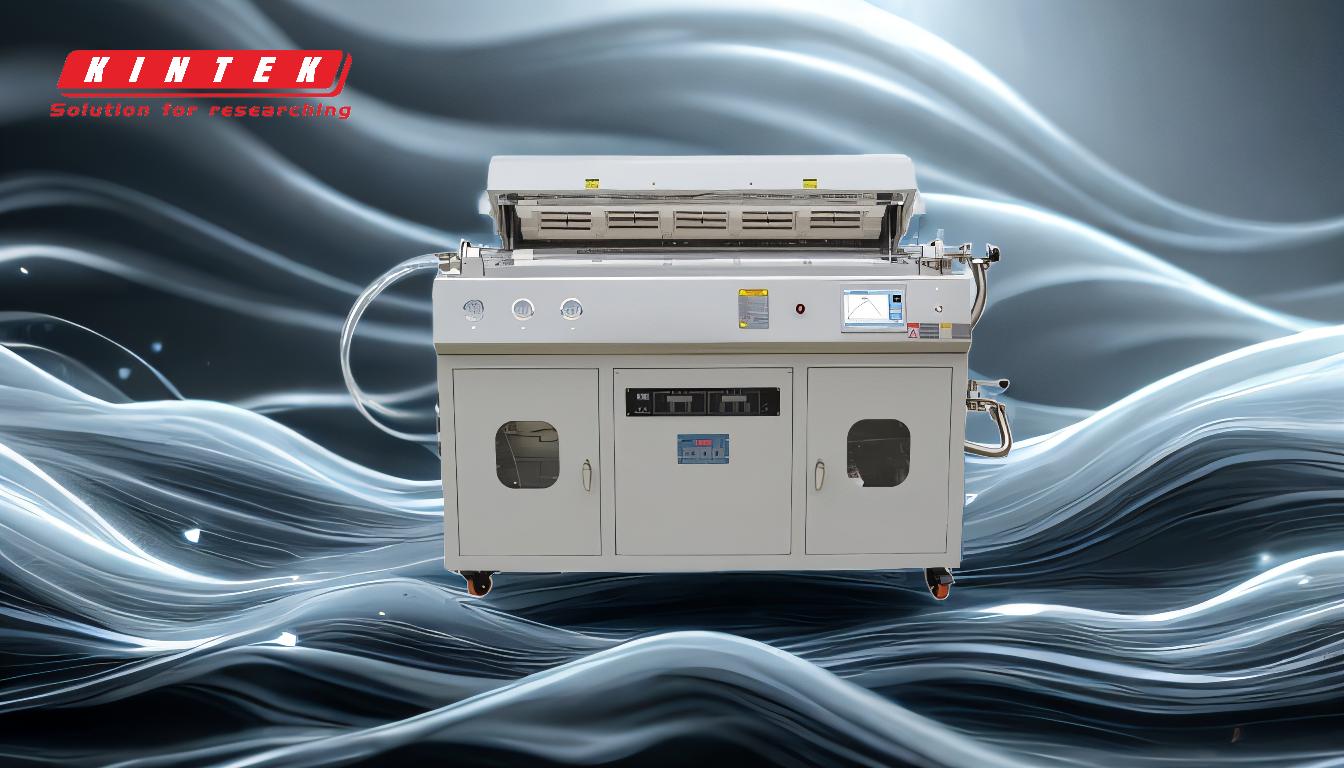
-
Thermal Evaporation:
- Thermal evaporation is one of the most common PVD coating methods. It involves heating the coating material (often in the form of pellets or wire) using an electric heater until it vaporizes. The vaporized material then condenses onto the substrate, forming a thin film.
- This method is known for its simplicity and ability to produce high-purity films. It is particularly effective for materials with low melting points.
- Applications include optical coatings, decorative coatings, and thin-film electronics.
-
Sputter Deposition:
- Sputter deposition involves bombarding a target material with high-energy ions (usually argon ions) in a vacuum chamber. The impact of the ions ejects atoms from the target, which then deposit onto the substrate.
- This method is highly versatile and can be used with a wide range of materials, including metals, alloys, and ceramics. It produces films with excellent adhesion and uniformity.
- Applications include semiconductor manufacturing, hard coatings for tools, and reflective coatings.
-
Ion Plating:
- Ion plating combines elements of sputtering and thermal evaporation. The coating material is vaporized, and the vapor is ionized before being deposited onto the substrate. This process enhances film adhesion and density.
- Ion plating is particularly useful for applications requiring high wear resistance, corrosion resistance, and decorative finishes.
- Common applications include automotive components, cutting tools, and aerospace parts.
-
Electron Beam Evaporation:
- In electron beam evaporation, a focused beam of high-energy electrons is used to heat and vaporize the coating material. The vaporized material then condenses onto the substrate.
- This method is ideal for materials with high melting points and is capable of producing extremely pure and uniform films.
- Applications include optical coatings, solar cells, and thin-film electronics.
-
Plasma Sputter Deposition:
- Plasma sputter deposition uses a plasma (ionized gas) to bombard the target material, causing it to vaporize. The vapor is then deposited onto the substrate.
- This method is known for its ability to produce dense, high-quality films with excellent adhesion and uniformity.
- Applications include protective coatings, decorative coatings, and thin-film electronics.
-
Molecular Beam Epitaxy (MBE):
- MBE is a specialized PVD technique used to grow high-quality crystalline films layer by layer. It involves directing molecular beams of the coating material onto the substrate under ultra-high vacuum conditions.
- This method is highly precise and is used primarily in the semiconductor industry for producing thin films with atomic-level control.
- Applications include advanced semiconductor devices, quantum dots, and optoelectronic components.
-
Ion Beam Sputtering Deposition:
- Ion beam sputtering uses a focused ion beam to sputter material from a target, which is then deposited onto the substrate. This method offers excellent control over film thickness and composition.
- It is commonly used for producing high-quality optical coatings and thin films for research and industrial applications.
-
Key Considerations for PVD Coating:
- Material Quality: High-quality raw materials, such as sputtering targets and evaporation materials, are essential for achieving optimal coating results.
- Process Control: Precise control over parameters like temperature, pressure, and deposition rate is critical for producing consistent and high-performance coatings.
- Application-Specific Selection: The choice of PVD method depends on the specific requirements of the application, such as film thickness, adhesion, and material compatibility.
By understanding these methods and their unique advantages, manufacturers and researchers can select the most appropriate PVD coating technique for their specific needs, ensuring high-quality and durable thin films.
Summary Table:
Method | Key Characteristics | Applications |
---|---|---|
Thermal Evaporation | Simple, high-purity films, effective for low melting points | Optical coatings, decorative coatings, thin-film electronics |
Sputter Deposition | Versatile, excellent adhesion and uniformity | Semiconductor manufacturing, hard coatings, reflective coatings |
Ion Plating | Combines sputtering and thermal evaporation, enhances adhesion and density | Automotive components, cutting tools, aerospace parts |
Electron Beam Evaporation | Ideal for high melting points, produces pure and uniform films | Optical coatings, solar cells, thin-film electronics |
Plasma Sputter Deposition | Produces dense, high-quality films with excellent adhesion | Protective coatings, decorative coatings, thin-film electronics |
Molecular Beam Epitaxy (MBE) | High-precision, atomic-level control for crystalline films | Advanced semiconductor devices, quantum dots, optoelectronic components |
Ion Beam Sputtering | Excellent control over film thickness and composition | High-quality optical coatings, research, and industrial applications |
Ready to choose the right PVD coating method for your application? Contact our experts today for personalized guidance!