Thin film application involves a variety of methods that can be broadly categorized into chemical and physical deposition techniques. These methods allow for precise control over the thickness, composition, and properties of the thin films, making them suitable for a wide range of applications, from semiconductors to flexible electronics. The choice of method depends on the desired film properties, the substrate material, and the specific application requirements.
Key Points Explained:
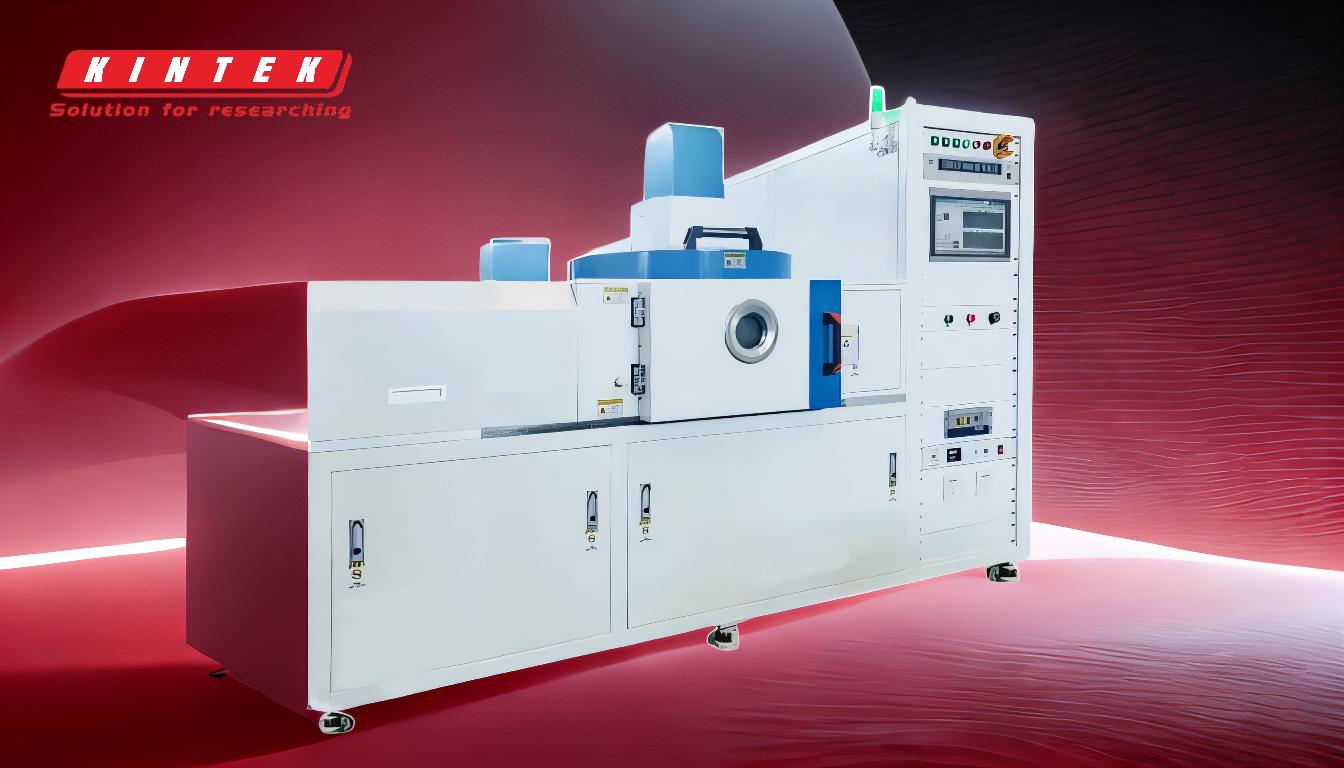
-
Chemical Deposition Methods:
- Electroplating: This method involves the deposition of a thin film onto a conductive substrate by passing an electric current through an electrolyte solution containing the desired metal ions. It is commonly used for coating metals and alloys.
- Sol-Gel: This technique involves the transition of a solution (sol) into a gel-like state, which is then dried and sintered to form a thin film. It is widely used for producing oxide films and is known for its ability to create films with high purity and homogeneity.
- Dip Coating: In this method, the substrate is dipped into a solution containing the film material and then withdrawn at a controlled speed. The thickness of the film is determined by the withdrawal speed and the viscosity of the solution. It is commonly used for coating large areas uniformly.
- Spin Coating: This technique involves depositing a liquid film onto a substrate and then spinning it at high speeds to spread the liquid into a thin, uniform layer. It is widely used in the semiconductor industry for applying photoresist layers.
- Chemical Vapor Deposition (CVD): CVD involves the chemical reaction of gaseous precursors on a heated substrate to form a solid thin film. It is used for depositing high-quality, uniform films and is widely used in the production of semiconductors and coatings.
- Plasma-Enhanced CVD (PECVD): This is a variation of CVD that uses plasma to enhance the chemical reaction at lower temperatures. It is particularly useful for depositing films on temperature-sensitive substrates.
- Atomic Layer Deposition (ALD): ALD is a precise method that deposits thin films one atomic layer at a time by alternating exposures to different gaseous precursors. It offers excellent control over film thickness and uniformity, making it ideal for applications requiring extremely thin and conformal coatings.
-
Physical Deposition Methods:
- Sputtering: This technique involves bombarding a target material with high-energy ions, causing atoms to be ejected and deposited onto a substrate. It is widely used for depositing metals, alloys, and compound films.
- Thermal Evaporation: In this method, the material to be deposited is heated to its evaporation point in a vacuum, and the vapor condenses onto the substrate to form a thin film. It is commonly used for depositing metals and simple compounds.
- Electron Beam Evaporation: This is a variation of thermal evaporation where an electron beam is used to heat the material to its evaporation point. It allows for the deposition of high-purity films and is used for materials with high melting points.
- Molecular Beam Epitaxy (MBE): MBE is a highly controlled method that deposits thin films by directing molecular or atomic beams onto a substrate under ultra-high vacuum conditions. It is used for growing high-quality crystalline films, particularly in semiconductor research.
- Pulsed Laser Deposition (PLD): PLD involves using a high-power laser to ablate material from a target, which then deposits onto a substrate. It is used for depositing complex oxide films and other materials that are difficult to deposit using other methods.
-
Combination Methods:
- Thermal Evaporation and Sputtering: Some applications may require the use of both thermal evaporation and sputtering to achieve specific film properties. For example, a combination of these methods can be used to deposit multi-layer films with different materials.
-
Applications and Considerations:
- Semiconductors: Methods like CVD, PECVD, and ALD are widely used in the semiconductor industry for depositing thin films of silicon, silicon dioxide, and other materials.
- Flexible Electronics: Techniques like spin coating and dip coating are used to deposit polymer films for flexible solar cells and OLEDs.
- Optical Coatings: Sputtering and thermal evaporation are commonly used for depositing thin films for optical applications, such as anti-reflective coatings and mirrors.
- Barrier Layers: ALD and PECVD are used to deposit ultra-thin barrier layers to protect sensitive materials from moisture and gases.
In conclusion, the choice of thin film application method depends on the specific requirements of the application, including the desired film properties, substrate material, and production scale. Each method has its advantages and limitations, and often, a combination of techniques is used to achieve the desired results.
Summary Table:
Category | Method | Key Applications |
---|---|---|
Chemical Deposition | Electroplating | Coating metals and alloys |
Sol-Gel | Oxide films, high purity and homogeneity | |
Dip Coating | Uniform coating of large areas | |
Spin Coating | Semiconductor photoresist layers | |
CVD | High-quality semiconductor films | |
PECVD | Films on temperature-sensitive substrates | |
ALD | Ultra-thin, conformal coatings | |
Physical Deposition | Sputtering | Metals, alloys, and compound films |
Thermal Evaporation | Metals and simple compounds | |
Electron Beam Evaporation | High-purity films, high melting point materials | |
MBE | High-quality crystalline films for semiconductors | |
PLD | Complex oxide films and hard-to-deposit materials | |
Combination Methods | Thermal Evaporation + Sputtering | Multi-layer films with different materials |
Need help selecting the right thin film application method? Contact our experts today for tailored solutions!