Thin films are essential in various industries, including electronics, optics, and energy, due to their unique properties and applications. Several methods are used to prepare thin films, each offering distinct advantages and suited for specific applications. These methods can be broadly categorized into chemical, physical, and electrically-based techniques. Key methods include drop casting, spin coating, plasma sputtering, chemical vapor deposition (CVD), and vapor deposition. Each technique allows for precise control over the thickness, composition, and properties of the thin films, making them suitable for applications ranging from semiconductor devices to flexible solar cells and organic light-emitting diodes (OLEDs).
Key Points Explained:
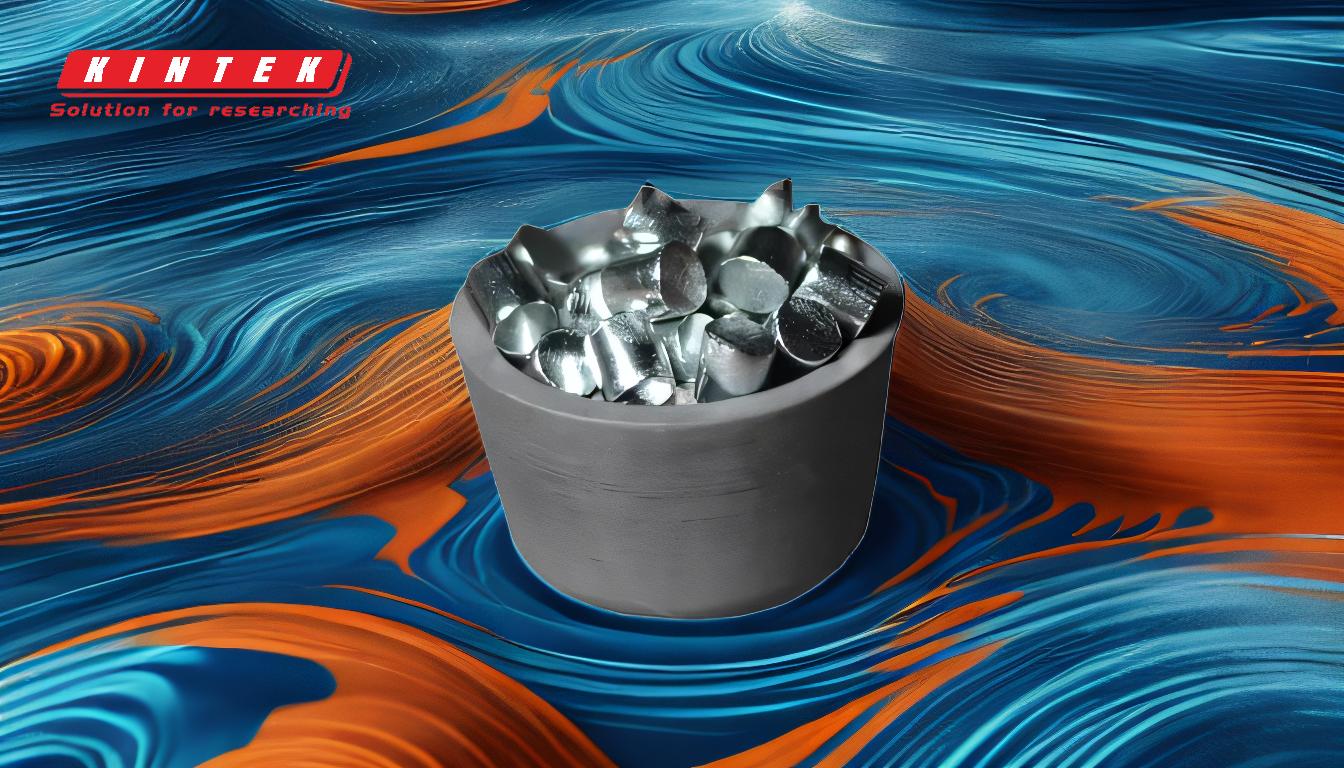
-
Drop Casting and Dip Casting:
- Process: In drop casting, a solution containing the material to be deposited is dropped onto a substrate, and the solvent evaporates, leaving behind a thin film. Dip casting involves immersing the substrate into a solution and then withdrawing it, allowing the solvent to evaporate.
- Advantages: Simple and cost-effective; suitable for small-scale production.
- Applications: Often used in research settings for creating thin films of polymers or nanoparticles.
-
Spin Coating:
- Process: A solution is applied to a substrate, which is then spun at high speeds to spread the solution evenly across the surface. The solvent evaporates, leaving a uniform thin film.
- Advantages: Produces highly uniform films with controlled thickness; widely used in the semiconductor industry.
- Applications: Used in the fabrication of microelectronics, photoresists, and optical coatings.
-
Plasma Sputtering:
- Process: A target material is bombarded with high-energy ions in a vacuum, causing atoms to be ejected and deposited onto a substrate.
- Advantages: Can deposit a wide range of materials, including metals, alloys, and ceramics; produces dense and adherent films.
- Applications: Commonly used in the production of thin films for semiconductors, optical coatings, and magnetic storage media.
-
Chemical Vapor Deposition (CVD):
- Process: A substrate is exposed to volatile precursors, which react or decompose on the surface to form a thin film.
- Advantages: Allows for precise control over film composition and thickness; can produce high-quality films with excellent conformality.
- Applications: Widely used in the semiconductor industry for depositing silicon, silicon dioxide, and other materials.
-
Vapor Deposition:
- Process: Material is vaporized in a vacuum and then condensed onto a substrate to form a thin film. This can be done through thermal evaporation or electron beam evaporation.
- Advantages: High purity films; suitable for depositing metals and simple compounds.
- Applications: Used in the production of optical coatings, thin-film transistors, and protective coatings.
-
Langmuir-Blodgett Film Formation:
- Process: A monolayer of amphiphilic molecules is spread on the surface of a liquid, compressed, and then transferred onto a solid substrate.
- Advantages: Allows for the creation of highly ordered and uniform films at the molecular level.
- Applications: Used in the study of molecular interactions, sensors, and organic electronics.
-
Self-Assembled Monolayer (SAM) Formation:
- Process: Molecules spontaneously organize into ordered structures on a substrate due to specific interactions between the molecules and the surface.
- Advantages: Simple and versatile; can create highly ordered films with specific functional groups.
- Applications: Used in surface modification, biosensors, and nanotechnology.
-
Spin-Assisted Layer-by-Layer (LbL) Assembly:
- Process: Alternating layers of different materials are deposited onto a substrate through sequential spin coating steps.
- Advantages: Allows for the creation of multilayer films with precise control over each layer's thickness and composition.
- Applications: Used in the fabrication of multilayer coatings, sensors, and drug delivery systems.
Each of these methods has its own set of advantages and is chosen based on the specific requirements of the application, such as film thickness, uniformity, material compatibility, and scalability. The choice of method can significantly impact the properties and performance of the thin film, making it crucial to select the appropriate technique for the desired outcome.
Summary Table:
Method | Process | Advantages | Applications |
---|---|---|---|
Drop/Dip Casting | Solution dropped or dipped onto a substrate; solvent evaporates. | Simple, cost-effective, suitable for small-scale production. | Research settings, polymers, nanoparticles. |
Spin Coating | Solution spun on a substrate; solvent evaporates to form a uniform film. | Produces highly uniform films; controlled thickness. | Microelectronics, photoresists, optical coatings. |
Plasma Sputtering | Target material bombarded with ions; atoms deposited onto a substrate. | Deposits metals, alloys, ceramics; dense and adherent films. | Semiconductors, optical coatings, magnetic storage. |
Chemical Vapor Deposition (CVD) | Substrate exposed to volatile precursors; reaction forms a thin film. | Precise control over composition and thickness; high-quality films. | Semiconductor industry, silicon, silicon dioxide. |
Vapor Deposition | Material vaporized in a vacuum; condensed onto a substrate. | High purity films; suitable for metals and simple compounds. | Optical coatings, thin-film transistors, protective coatings. |
Langmuir-Blodgett | Monolayer spread on liquid, compressed, and transferred to a substrate. | Highly ordered and uniform films at the molecular level. | Molecular interactions, sensors, organic electronics. |
Self-Assembled Monolayer (SAM) | Molecules organize into ordered structures on a substrate. | Simple, versatile; creates highly ordered films with specific functional groups. | Surface modification, biosensors, nanotechnology. |
Spin-Assisted LbL | Alternating layers deposited via sequential spin coating. | Precise control over multilayer film thickness and composition. | Multilayer coatings, sensors, drug delivery systems. |
Need help selecting the right thin film preparation method for your application? Contact our experts today!