Hot Isostatic Pressing (HIP) is a sophisticated manufacturing process that combines high temperature and pressure to achieve fully dense materials, often reaching up to 100% theoretical density. This process is particularly beneficial for engineered ceramics and high-performance applications, offering advantages such as improved mechanical properties, reduced internal stress, and the ability to repair internal defects. The parameters of HIP, including temperature, pressure, and process time, are critical to achieving the desired material properties. The process is widely used across various industries, including aerospace, automotive, medical devices, and energy storage technologies.
Key Points Explained:
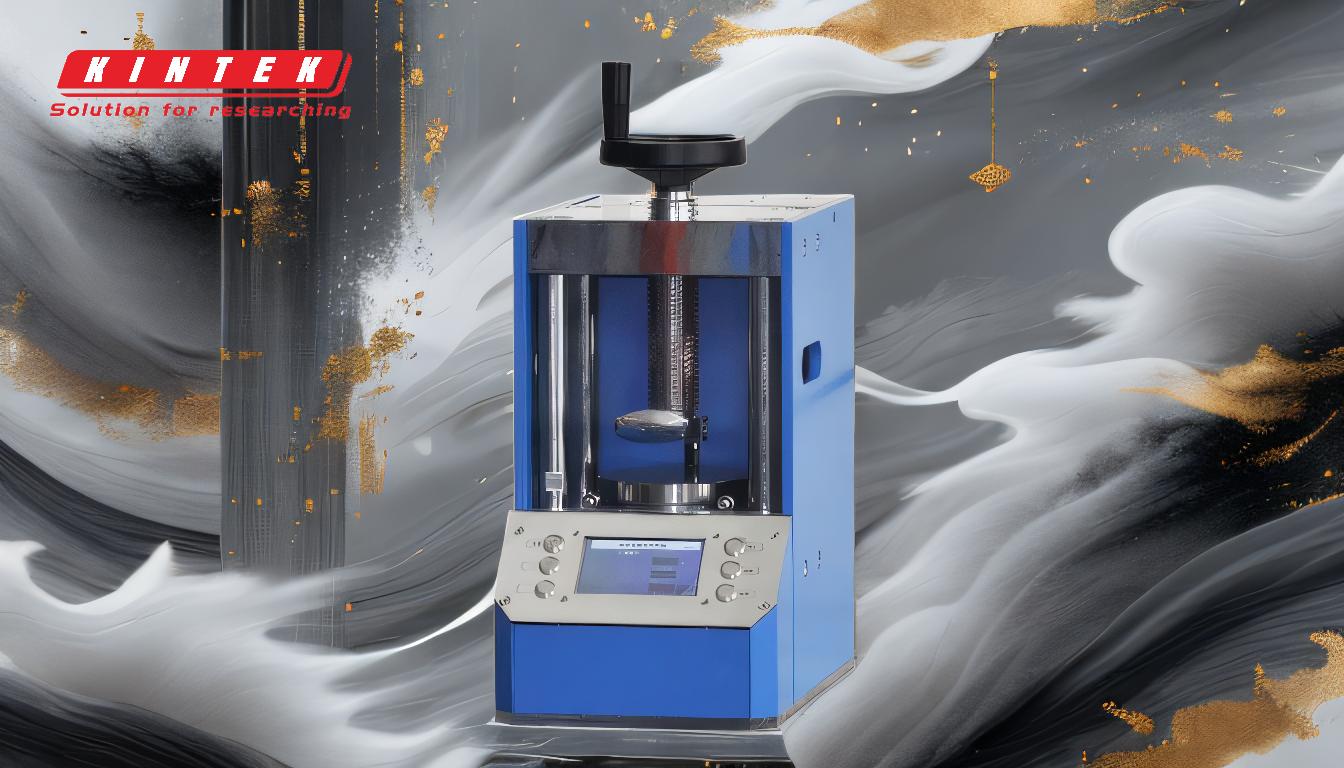
-
Temperature and Pressure Parameters:
- The temperature in HIP typically ranges from 900°C to 2,000°C, depending on the material being processed. For example, ceramics and metals may require different temperature ranges to achieve optimal densification.
- The pressure applied during HIP usually ranges from 100 MPa to 300 MPa. This high pressure, combined with elevated temperatures, helps in achieving full densification and eliminating porosity in the material.
-
Process Time:
- The total process time in HIP can vary significantly based on the material and the desired properties. It generally includes the time required for heating, holding at the desired temperature and pressure, and cooling. The holding time can range from a few minutes to several hours.
-
Inert Gas Environment:
- HIP is conducted in an inert gas environment, typically using argon, to prevent oxidation and other chemical reactions that could degrade the material properties. The inert gas also ensures uniform pressure application.
-
Applications and Industries:
- HIP is extensively used in industries requiring high-performance materials. For instance, in the aerospace industry, it is used to manufacture components that need to withstand extreme conditions. In the medical field, HIP is used to produce biocompatible implants with high strength and durability. The process is also crucial in the production of energy storage devices like lithium-ion batteries and fuel cells.
-
Advantages of HIP:
- Increased Density: HIP can achieve near-theoretical density, which enhances the material's mechanical properties.
- Improved Mechanical Properties: The process results in materials with better strength, ductility, and toughness.
- Defect Repair: HIP can heal internal porosity and other defects, leading to more reliable components.
- Versatility: It can be used to bond different materials metallurgically, creating composites with unique properties.
-
Types of HIP Capacities:
- HIP systems are categorized based on their size and capacity, including small-sized, medium-sized, and large-sized HIP units. The choice of system depends on the size and volume of the components being processed.
-
Comparison with Cold Isostatic Pressing (CIP):
- While CIP is used for compacting green parts at ambient temperatures, HIP involves elevated temperatures and is used for full consolidation and densification of materials. The uniform pressure application in both processes ensures minimal friction and uniform density distribution.
-
Uniform Pressure Application:
- In HIP, the pressure is applied uniformly in all directions due to the isostatic nature of the process. This uniformity ensures that the material experiences equal compaction forces, leading to consistent density and improved mechanical properties.
In summary, the parameters of hot isostatic pressing, including temperature, pressure, and process time, are crucial for achieving high-density, high-performance materials. The process's ability to uniformly apply pressure and heat in an inert environment makes it indispensable in various high-tech industries. For more detailed information on related equipment, you can explore the warm isostatic press.
Summary Table:
Parameter | Details |
---|---|
Temperature Range | 900°C to 2,000°C, depending on material. |
Pressure Range | 100 MPa to 300 MPa. |
Process Time | Varies from minutes to hours, including heating, holding, and cooling. |
Inert Gas | Typically argon, to prevent oxidation and ensure uniform pressure. |
Applications | Aerospace, automotive, medical devices, energy storage, and more. |
Advantages | Increased density, improved mechanical properties, defect repair, versatility. |
Learn how hot isostatic pressing can enhance your material performance—contact our experts today!