Induction furnaces are widely used in industrial settings for their ability to rapidly heat and melt metals, enhancing productivity and meeting large production demands. However, their operation can lead to several power quality issues that may affect the efficiency and reliability of the power system. These issues include harmonic distortions, voltage fluctuations, and power factor problems, which can result in increased energy costs, equipment malfunctions, and reduced lifespan of electrical components. Understanding these power quality challenges is crucial for industries to implement effective mitigation strategies and maintain optimal operational performance.
Key Points Explained:
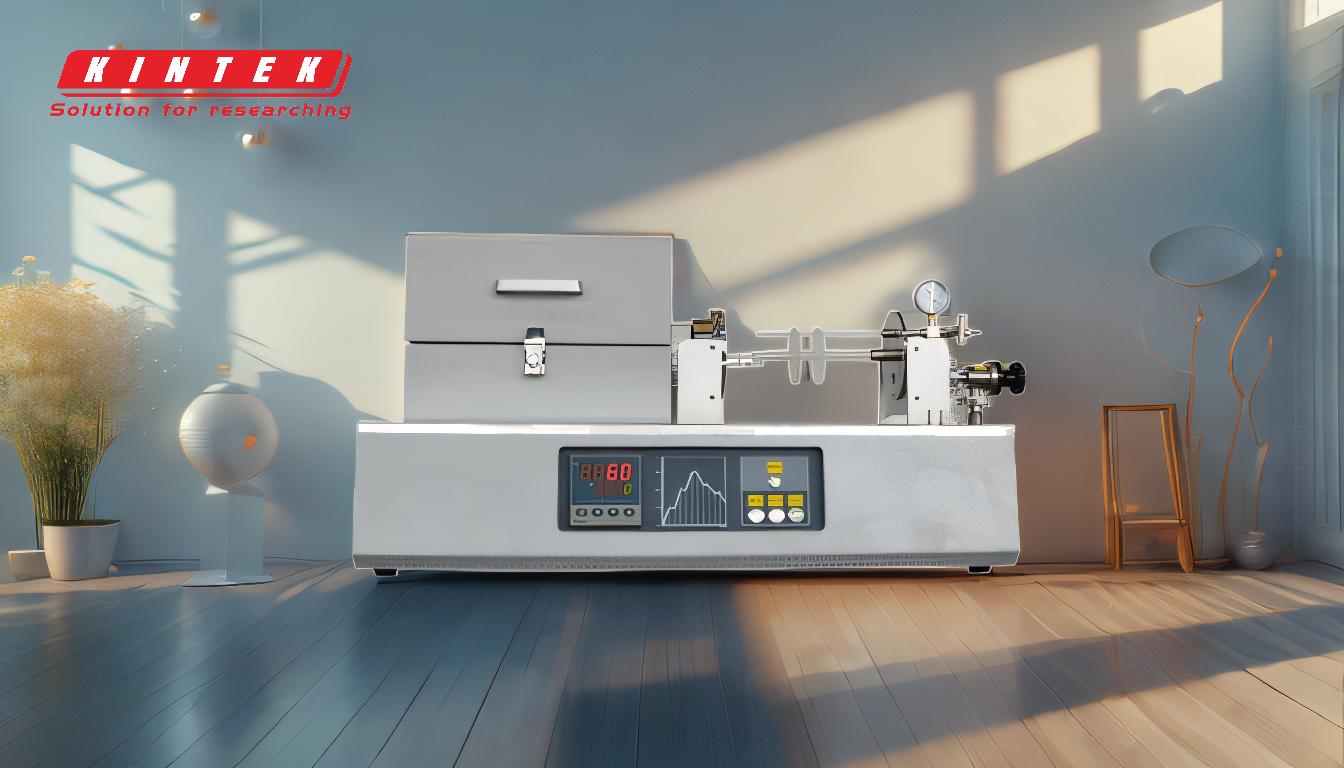
-
Harmonic Distortions:
- Cause: Induction furnaces, especially those using IGBT induction furnace technology, generate harmonics due to the non-linear nature of their power electronic components. These harmonics can distort the sinusoidal waveform of the electrical supply.
- Impact: Harmonic distortions can lead to overheating of transformers and cables, malfunctions in sensitive electronic equipment, and interference with communication systems. They can also cause resonance issues in the power network, leading to severe damage.
- Mitigation: To address harmonic distortions, industries can use harmonic filters, active power filters, or install equipment designed to handle harmonic loads.
-
Voltage Fluctuations:
- Cause: The rapid and variable power demand of induction furnaces can cause voltage fluctuations, also known as flicker. This is particularly noticeable when the furnace is started or when there are sudden changes in the load.
- Impact: Voltage fluctuations can cause lighting flicker, which is not only a nuisance but can also affect the performance of other connected equipment. It can lead to inconsistent operation of machinery and may trip protective devices.
- Mitigation: Voltage stabilizers, dynamic voltage restorers, and proper load management can help mitigate voltage fluctuations. Ensuring a robust and well-designed power supply system is also crucial.
-
Power Factor Issues:
- Cause: Induction furnaces often operate at a low power factor due to the inductive nature of the load. This results in a higher reactive power demand, which can strain the power supply system.
- Impact: A low power factor increases the current flow in the system, leading to higher energy losses, increased electricity bills, and reduced capacity of the power distribution network. It can also cause voltage drops and affect the performance of other equipment.
- Mitigation: Power factor correction devices, such as capacitors or synchronous condensers, can be installed to improve the power factor. Regular monitoring and maintenance of the power system are also essential to ensure optimal power factor levels.
-
Electromagnetic Interference (EMI):
- Cause: The high-frequency operation of induction furnaces can generate electromagnetic interference, which can affect nearby electronic devices and communication systems.
- Impact: EMI can disrupt the operation of sensitive equipment, leading to data corruption, signal interference, and potential safety hazards. It can also affect the performance of wireless communication systems.
- Mitigation: Shielding, proper grounding, and the use of EMI filters can help reduce electromagnetic interference. Ensuring that the furnace is installed at an appropriate distance from sensitive equipment is also important.
-
Energy Efficiency Concerns:
- Cause: While induction furnaces are generally energy-efficient, power quality issues such as harmonics and low power factor can reduce their overall efficiency.
- Impact: Reduced energy efficiency can lead to higher operational costs and increased energy consumption. It can also contribute to a larger carbon footprint, which is a concern for environmentally conscious industries.
- Mitigation: Implementing energy management systems, optimizing furnace operation, and using energy-efficient components can help improve the overall energy efficiency of induction furnaces.
-
Maintenance and Reliability:
- Cause: Power quality issues can increase the wear and tear on electrical components, leading to more frequent maintenance requirements and reduced reliability of the equipment.
- Impact: Increased maintenance costs, unexpected downtime, and potential production losses are some of the consequences of poor power quality. It can also affect the lifespan of the induction furnace and other connected equipment.
- Mitigation: Regular maintenance, condition monitoring, and the use of high-quality components can help enhance the reliability and longevity of induction furnaces.
By addressing these power quality issues, industries can ensure the efficient and reliable operation of their induction furnaces, ultimately leading to improved productivity and reduced operational costs.
Summary Table:
Issue | Cause | Impact | Mitigation |
---|---|---|---|
Harmonic Distortions | Non-linear power electronic components distort the electrical waveform. | Overheating, equipment malfunctions, communication interference, and resonance issues. | Use harmonic filters, active power filters, or install harmonic-tolerant equipment. |
Voltage Fluctuations | Rapid and variable power demand causes flicker. | Lighting flicker, inconsistent machinery operation, and tripping of protective devices. | Use voltage stabilizers, dynamic voltage restorers, and proper load management. |
Power Factor Issues | Inductive load results in low power factor and higher reactive power. | Increased energy losses, higher electricity bills, and reduced power distribution capacity. | Install power factor correction devices like capacitors or synchronous condensers. |
EMI | High-frequency operation generates electromagnetic interference. | Disruption of sensitive equipment, data corruption, and signal interference. | Use shielding, proper grounding, and EMI filters. |
Energy Efficiency | Harmonics and low power factor reduce overall efficiency. | Higher operational costs, increased energy consumption, and larger carbon footprint. | Implement energy management systems and optimize furnace operation. |
Maintenance | Power quality issues increase wear and tear on electrical components. | Increased maintenance costs, unexpected downtime, and reduced equipment lifespan. | Regular maintenance, condition monitoring, and use of high-quality components. |
Ensure your induction furnace operates efficiently—contact our experts today for tailored solutions!