Heat treatment of steel is a critical process that involves heating and cooling to alter the material's physical and mechanical properties. Precautions during this process are essential to ensure the desired outcomes, such as improved hardness, strength, or ductility, while avoiding defects like cracking, warping, or uneven hardness. Key precautions include proper temperature control, uniform heating and cooling, appropriate atmosphere control, and adherence to specific steel grades' requirements. Understanding the steel's composition, selecting the right heat treatment method, and using suitable equipment are also crucial. Below is a detailed explanation of the precautions to consider during the heat treatment of steel.
Key Points Explained:
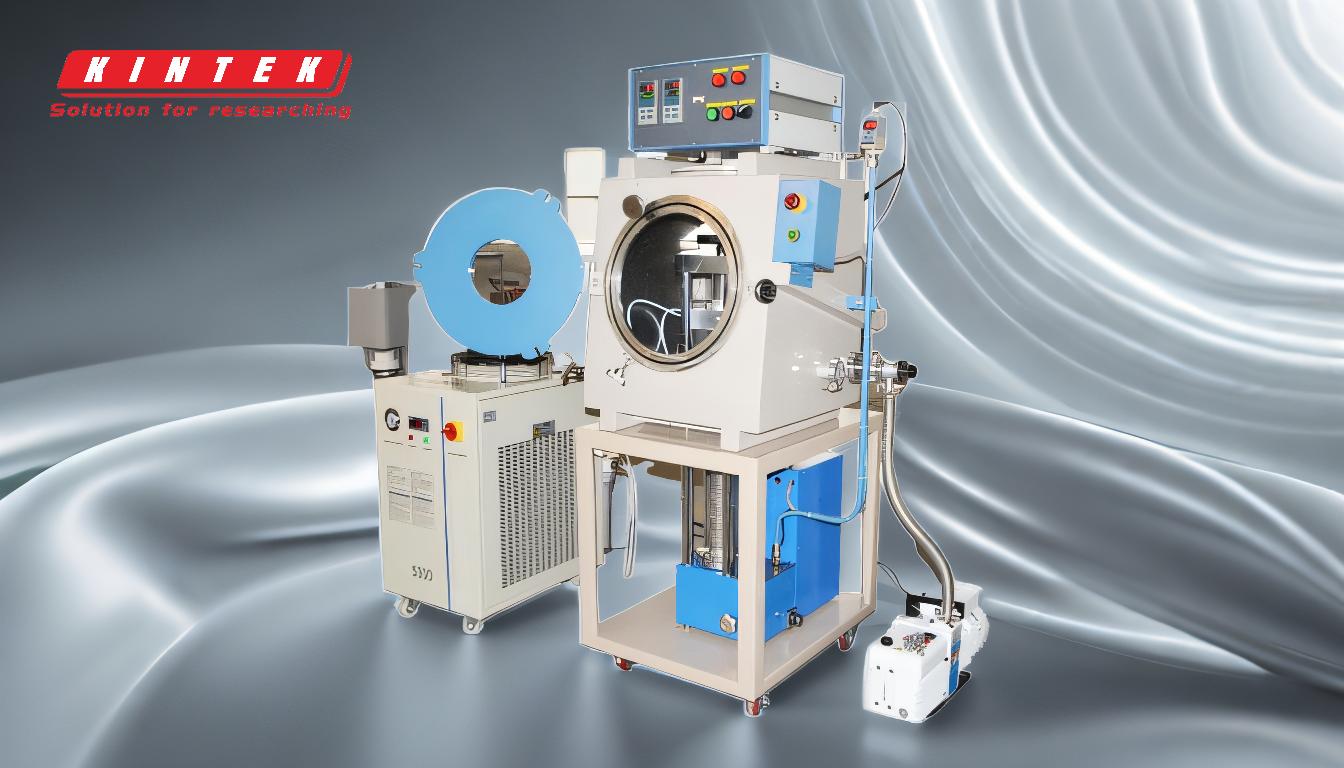
-
Temperature Control
- Importance: Precise temperature control is vital to achieve the desired microstructure and properties.
-
Precautions:
- Use calibrated thermocouples and temperature controllers to monitor and maintain the correct temperature.
- Avoid overheating, which can lead to grain growth, reduced strength, and potential melting.
- Ensure the steel reaches the required temperature uniformly to prevent thermal stresses.
-
Uniform Heating and Cooling
- Importance: Non-uniform heating or cooling can cause warping, cracking, or uneven hardness.
-
Precautions:
- Use furnaces with good heat circulation to ensure even temperature distribution.
- For cooling, choose appropriate quenching media (oil, water, or air) based on the steel grade and desired properties.
- Avoid rapid cooling in thick sections, as it can cause internal stresses and cracking.
-
Atmosphere Control
- Importance: The furnace atmosphere can affect the steel's surface quality and properties.
-
Precautions:
- Use inert or controlled atmospheres (e.g., nitrogen, argon) to prevent oxidation or decarburization.
- For carburizing or nitriding processes, maintain the correct gas composition to achieve the desired surface hardness.
- Regularly check and maintain the furnace atmosphere to avoid contamination.
-
Understanding Steel Composition
- Importance: Different steel grades have unique heat treatment requirements based on their alloying elements.
-
Precautions:
- Refer to the steel's material data sheet to determine the appropriate heat treatment parameters.
- Adjust the heating and cooling rates based on the carbon content and alloying elements.
- Be aware of the steel's hardenability, which affects the depth of hardness achieved during quenching.
-
Selection of Heat Treatment Method
- Importance: The choice of heat treatment method (e.g., annealing, quenching, tempering) depends on the desired properties.
-
Precautions:
- Annealing: Use slow cooling to soften the steel and relieve internal stresses.
- Quenching: Rapidly cool the steel to achieve high hardness, but avoid excessive cooling rates that can cause cracking.
- Tempering: Reheat quenched steel to a specific temperature to reduce brittleness and improve toughness.
-
Equipment and Consumables
- Importance: Proper equipment and consumables are essential for consistent and reliable heat treatment.
-
Precautions:
- Use furnaces with accurate temperature control and uniform heating capabilities.
- Ensure quenching media are clean and at the correct temperature to avoid contamination or inconsistent cooling.
- Regularly maintain and calibrate heat treatment equipment to ensure optimal performance.
-
Post-Treatment Inspection
- Importance: Inspecting the steel after heat treatment ensures the desired properties have been achieved.
-
Precautions:
- Perform hardness testing, microstructure analysis, and dimensional checks to verify the results.
- Look for defects such as cracks, warping, or uneven hardness, and address any issues promptly.
- Document the heat treatment process and results for quality control and future reference.
-
Safety Considerations
- Importance: Heat treatment involves high temperatures and potentially hazardous materials, requiring strict safety measures.
-
Precautions:
- Wear appropriate personal protective equipment (PPE), such as heat-resistant gloves and face shields.
- Ensure proper ventilation to avoid exposure to harmful fumes or gases.
- Train personnel on safe handling of heat treatment equipment and emergency procedures.
By following these precautions, manufacturers can achieve the desired mechanical properties in steel while minimizing the risk of defects or failures. Proper planning, execution, and inspection are key to successful heat treatment processes.
Summary Table:
Precaution | Importance | Key Actions |
---|---|---|
Temperature Control | Ensures desired microstructure and properties. | Use calibrated thermocouples, avoid overheating, ensure uniform heating. |
Uniform Heating & Cooling | Prevents warping, cracking, or uneven hardness. | Use furnaces with good heat circulation, choose appropriate quenching media. |
Atmosphere Control | Protects steel surface quality and properties. | Use inert or controlled atmospheres, maintain correct gas composition. |
Understanding Steel Composition | Tailors heat treatment to specific steel grades. | Refer to material data sheets, adjust heating/cooling rates. |
Selection of Heat Treatment Method | Achieves desired properties (e.g., hardness, toughness). | Choose annealing, quenching, or tempering based on requirements. |
Equipment & Consumables | Ensures consistent and reliable heat treatment. | Use accurate furnaces, clean quenching media, maintain equipment. |
Post-Treatment Inspection | Verifies desired properties and detects defects. | Perform hardness testing, microstructure analysis, and dimensional checks. |
Safety Considerations | Protects personnel and ensures safe operations. | Wear PPE, ensure ventilation, train personnel on safety protocols. |
Optimize your steel heat treatment process—contact our experts today for tailored solutions!