Rotary kilns are cylindrical furnaces that rotate slowly around their longitudinal axis, designed to heat materials uniformly and induce specific chemical or physical reactions. They operate by feeding raw materials into the upper end of the inclined drum, where the rotation causes the material to tumble and move downward. Heat is applied either internally (direct heating) or externally (indirect heating) to achieve the desired temperature, typically ranging from 800 to 2,200°F. The process involves gas flow, fuel combustion, and heat transfer, ensuring the material undergoes physical and chemical changes to form the final product. Rotary kilns are widely used in processes such as calcination, incineration, thermal desorption, and organic combustion.
Key Points Explained:
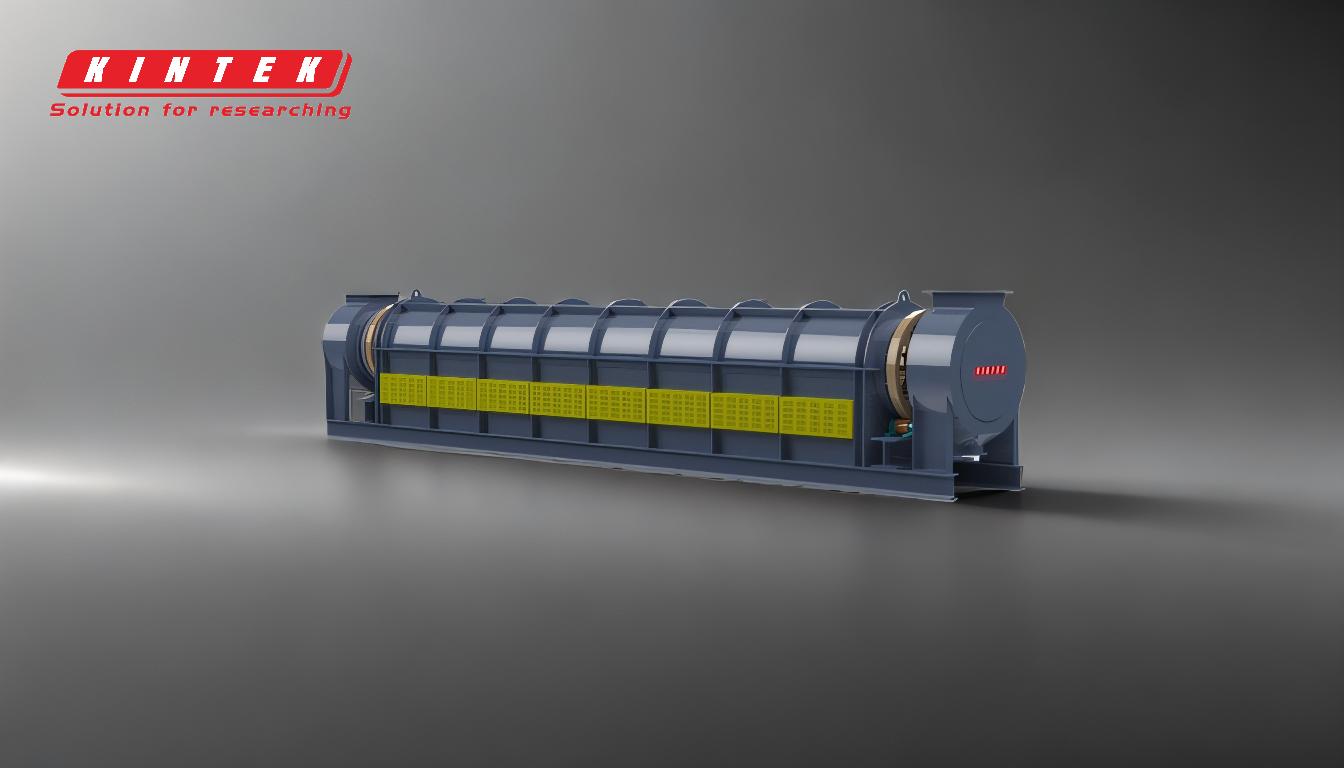
-
Basic Structure and Function:
- A rotary kiln is a cylindrical vessel, slightly inclined from the horizontal, that rotates slowly around its longitudinal axis.
- The inclination allows materials to move downward as the kiln rotates, ensuring continuous processing.
- The kiln is heated either internally (direct heating) or externally (indirect heating) to achieve the required temperature for the intended reaction.
-
Material Movement and Mixing:
- Raw materials are fed into the upper end of the kiln using a feeding device, such as a screw feeder.
- As the kiln rotates, the material tumbles and moves downward, undergoing constant stirring and mixing.
- This tumbling action ensures uniform heating and exposure to the hot gases, promoting consistent reactions.
-
Heating and Heat Transfer:
- Heat is generated either by an external furnace or by a flame inside the kiln, projected from a burner-pipe.
- The fuel for the flame can be gas, oil, pulverized petroleum coke, or pulverized coal.
- Hot gases flow along the kiln, either in the same direction (co-current) or opposite direction (counter-current) to the material flow, ensuring efficient heat transfer.
-
Temperature Range and Applications:
- Rotary kilns operate at temperatures ranging from 800 to 2,200°F, making them suitable for high-temperature processes.
- Common applications include calcination, incineration, thermal desorption, organic combustion, and heat setting.
-
Gas Flow and Combustion:
- The working principle involves gas flow, fuel combustion, and heat transfer.
- The kiln ensures that the fuel burns fully, and the heat from combustion is effectively transferred to the material.
- This process drives the physical and chemical changes required to form the final product, such as clinker in cement production.
-
Internal Configuration and Adjustments:
- The internal configuration of the kiln can be adjusted to increase tumbling or expose materials to more heat before they exit.
- This flexibility allows for optimization of the process to achieve the desired reaction or product quality.
-
Key Features:
- The rotary reactor is a long horizontal cylinder tilted on its axis, designed to drive specific bed reactions that require high bed temperatures for kinetic or thermodynamic reasons.
- The system is engineered to handle a wide range of materials and processes, making it versatile for various industrial applications.
By understanding these principles, equipment and consumable purchasers can make informed decisions about selecting and operating rotary kilns for their specific industrial needs.
Summary Table:
Aspect | Details |
---|---|
Structure | Cylindrical, inclined vessel rotating around its axis |
Heating Method | Direct (internal) or indirect (external) heating |
Temperature Range | 800°F to 2,200°F |
Material Movement | Tumbling action ensures uniform heating and mixing |
Applications | Calcination, incineration, thermal desorption, organic combustion |
Fuel Types | Gas, oil, pulverized petroleum coke, or coal |
Key Features | Adjustable internal configuration for optimized reactions |
Ready to optimize your industrial processes? Contact our experts today to find the perfect rotary kiln for your needs!