Thin films are layers of material ranging from fractions of a nanometer to several micrometers in thickness, deposited onto substrates to achieve specific functionalities. The principles of thin films revolve around their unique properties, deposition processes, and applications. Key aspects include their optical, electrical, magnetic, chemical, mechanical, and thermal characteristics, which are influenced by factors like material purity, structural defects, and deposition techniques. Thin films are created using methods such as thermal evaporation, sputtering, and chemical vapor deposition, often in a vacuum to ensure uniformity and prevent contamination. These films enable functionalities like anti-reflective coatings, gas impermeability, and electrical conductivity, which are not achievable with bulk materials alone.
Key Points Explained:
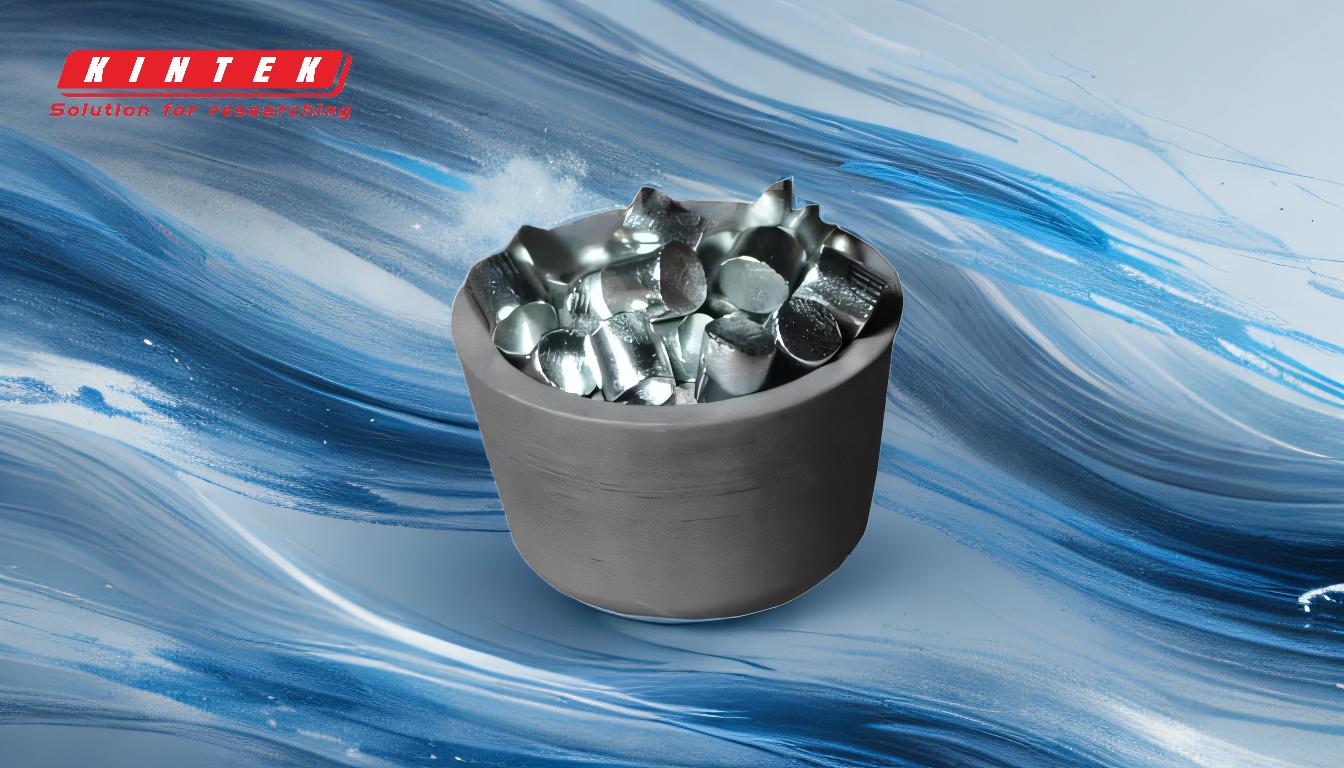
-
Definition and Characteristics of Thin Films:
- Thin films are layers of material with thicknesses ranging from nanometers to micrometers.
- They are characterized by three main processes: adsorption (transfer of atoms/molecules to a surface), desorption (release of adsorbed substances), and surface diffusion (movement of atoms/molecules on surfaces).
- These characteristics enable thin films to interact with their environment in unique ways, making them suitable for specialized applications.
-
Properties of Thin Films:
- Optical Properties: Influenced by factors like electrical conductivity, structural defects, and surface roughness. These properties determine how thin films interact with light, affecting transmission and reflection coefficients.
- Electrical Properties: Thin films can be designed to be electrically conductive or insulating, depending on the application.
- Magnetic, Chemical, Mechanical, and Thermal Properties: These enable functionalities such as corrosion resistance, wear protection, heat management, and catalytic activity.
- Functional Properties: Thin films can be anti-reflective, gas-impermeable, optically transparent yet electrically conductive, and self-cleaning.
-
Material Properties Influencing Thin Films:
- Purity, melting point, boiling point, electrical resistivity, and refractive index are critical material properties.
- These properties affect the deposition process and the final performance of the thin film in its intended application.
-
Deposition Processes:
- Thin films are deposited onto substrates using techniques such as thermal evaporation, sputtering, ion beam deposition, and chemical vapor deposition.
- The process typically occurs in a vacuum to prevent contamination and ensure uniform deposition.
- Evaporation Process: Involves heating the source material until it evaporates and condenses on the substrate. This requires a heat source and a vacuum environment.
-
Applications of Thin Films:
- Thin films are used in electronics, optics, energy, and protective coatings.
- Examples include reflective coatings, anti-reflective layers, gas barriers, and self-cleaning surfaces.
- Their ability to achieve functionalities not possible with bulk materials makes them indispensable in advanced technologies.
-
Importance of Vacuum in Deposition:
- A vacuum environment is crucial for maintaining process integrity, preventing contamination, and ensuring uniform film thickness.
- It also allows for precise control over the deposition process, which is essential for achieving desired film properties.
-
Advantages Over Bulk Materials:
- Thin films offer enhanced properties such as improved optical performance, electrical conductivity, and mechanical strength.
- They enable miniaturization and integration in microsystems, making them ideal for modern electronics and nanotechnology.
By understanding these principles, one can appreciate the versatility and significance of thin films in various industries, from electronics to energy and beyond. Their unique properties and deposition methods make them a cornerstone of advanced material science and engineering.
Summary Table:
Aspect | Details |
---|---|
Definition | Layers of material (nanometers to micrometers) deposited onto substrates. |
Key Properties | Optical, electrical, magnetic, chemical, mechanical, and thermal. |
Deposition Techniques | Thermal evaporation, sputtering, chemical vapor deposition, ion beam. |
Applications | Electronics, optics, energy, protective coatings, and self-cleaning surfaces. |
Advantages | Enhanced optical performance, electrical conductivity, and miniaturization. |
Discover how thin films can revolutionize your applications—contact our experts today!