Sintering is a critical manufacturing process used to create durable and high-performance materials by compacting and fusing particles without melting them. It is widely applied in industries such as automotive, aerospace, electronics, and biomedical engineering. The process involves applying heat and pressure to powdered materials, causing atoms to diffuse across particle boundaries and form a solid mass. The resulting products exhibit improved mechanical, thermal, and electrical properties, making them suitable for applications like automotive gears, cutting tools, aerospace components, and biomedical implants. Sintering also influences microstructural characteristics such as grain size and porosity, which directly impact material performance.
Key Points Explained:
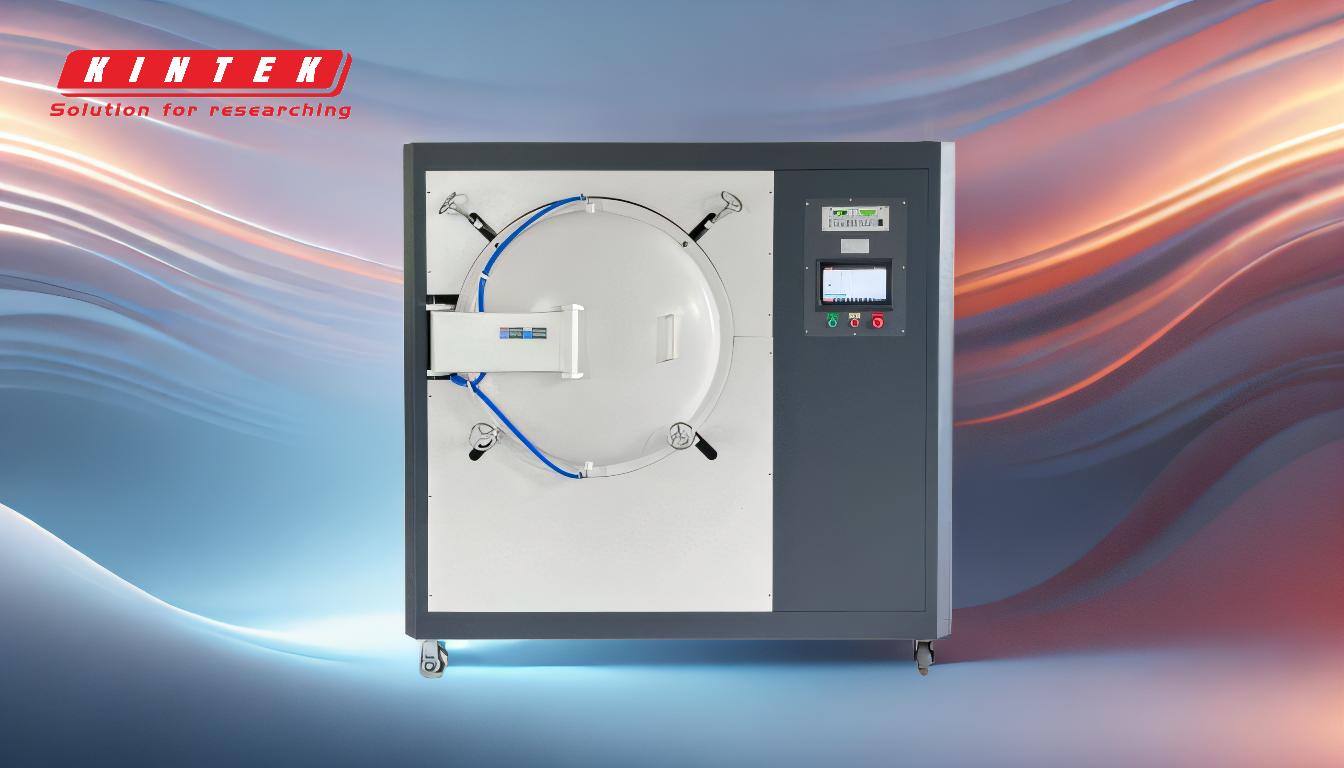
-
Definition and Purpose of Sintering:
- Sintering is a process that compacts and forms solid materials by applying heat and pressure without melting the material to a liquid state.
- It is particularly useful for materials with high melting points, such as tungsten and molybdenum, and is widely used in powder metallurgy and ceramic manufacturing.
-
Mechanism of Sintering:
- During sintering, atoms diffuse across particle boundaries, fusing them together to create a dense, solid mass.
- This process occurs at temperatures below the material's melting point, ensuring that the material retains its structural integrity while achieving enhanced properties.
-
Microstructural Changes:
- Sintering directly affects the microstructure of materials, including grain size, pore size, and grain boundary distribution.
- These changes lead to improved mechanical properties such as strength, durability, and thermal conductivity.
-
Applications of Sintered Products:
- Automotive Parts: Gears, actuators, and other components benefit from the strength and durability achieved through sintering.
- Electrical Components: Switchgear and other electrical parts are produced with enhanced conductivity and reliability.
- Cutting Tools: Tools like milling cutters, drills, and reamers are made more durable and efficient.
- Aerospace Components: Fuel valve components, actuators, and turbine blades are sintered to meet high-performance requirements.
- Biomedical Implants: Prosthetic joints and other implants are manufactured with biocompatible materials that are strong and long-lasting.
-
Material Properties Enhanced by Sintering:
- Reduced Porosity: Sintering decreases porosity, leading to denser and more uniform materials.
- Improved Strength and Durability: The process enhances mechanical properties, making materials more resistant to wear and tear.
- Enhanced Thermal and Electrical Conductivity: Sintered materials often exhibit better thermal and electrical performance, making them suitable for high-performance applications.
- Translucency: In some cases, sintering can improve translucency, which is particularly useful in ceramic and glass manufacturing.
-
Comparison with Other Processes:
- Unlike calcination, which removes impurities from metal ores, sintering focuses on fusing particles to create a solid mass.
- Sintering is distinct from melting, as it occurs below the material's melting point, preserving the material's microstructure and properties.
-
Process Considerations:
- The success of sintering depends on factors such as temperature, pressure, and the properties of the base material.
- Careful control of these parameters can optimize the balance between strength and porosity, depending on the desired application.
-
Industries Benefiting from Sintering:
- Powder Metallurgy: Used to produce metal components with complex shapes and high precision.
- Ceramic Manufacturing: Enables the production of durable and heat-resistant ceramic products.
- Advanced Materials: Sintering is crucial for developing materials with tailored properties for specific industrial needs.
In summary, sintering is a versatile and essential process for creating high-performance materials with enhanced properties. Its applications span multiple industries, and its ability to improve material characteristics makes it a cornerstone of modern manufacturing.
Summary Table:
Aspect | Details |
---|---|
Definition | Compacting and fusing particles without melting to form durable materials. |
Key Mechanism | Heat and pressure cause atomic diffusion, creating a solid mass. |
Microstructural Impact | Improves grain size, porosity, and material strength. |
Applications | Automotive gears, cutting tools, aerospace components, biomedical implants. |
Enhanced Properties | Strength, durability, thermal/electrical conductivity, and translucency. |
Industries | Automotive, aerospace, electronics, biomedical, and advanced materials. |
Discover how sintering can optimize your material manufacturing—contact our experts today!