Calcination is a thermal treatment process primarily used to remove impurities, volatile substances, or moisture from materials, often metal ores or minerals. The process involves heating the material to high temperatures in the absence or limited supply of air or oxygen. The results of calcination include the decomposition of carbonates, hydroxides, and other compounds, leading to the formation of oxides, the removal of water or carbon dioxide, and the purification of the material. This process is crucial in metallurgy, ceramics, and chemical industries for preparing materials for further processing or use.
Key Points Explained:
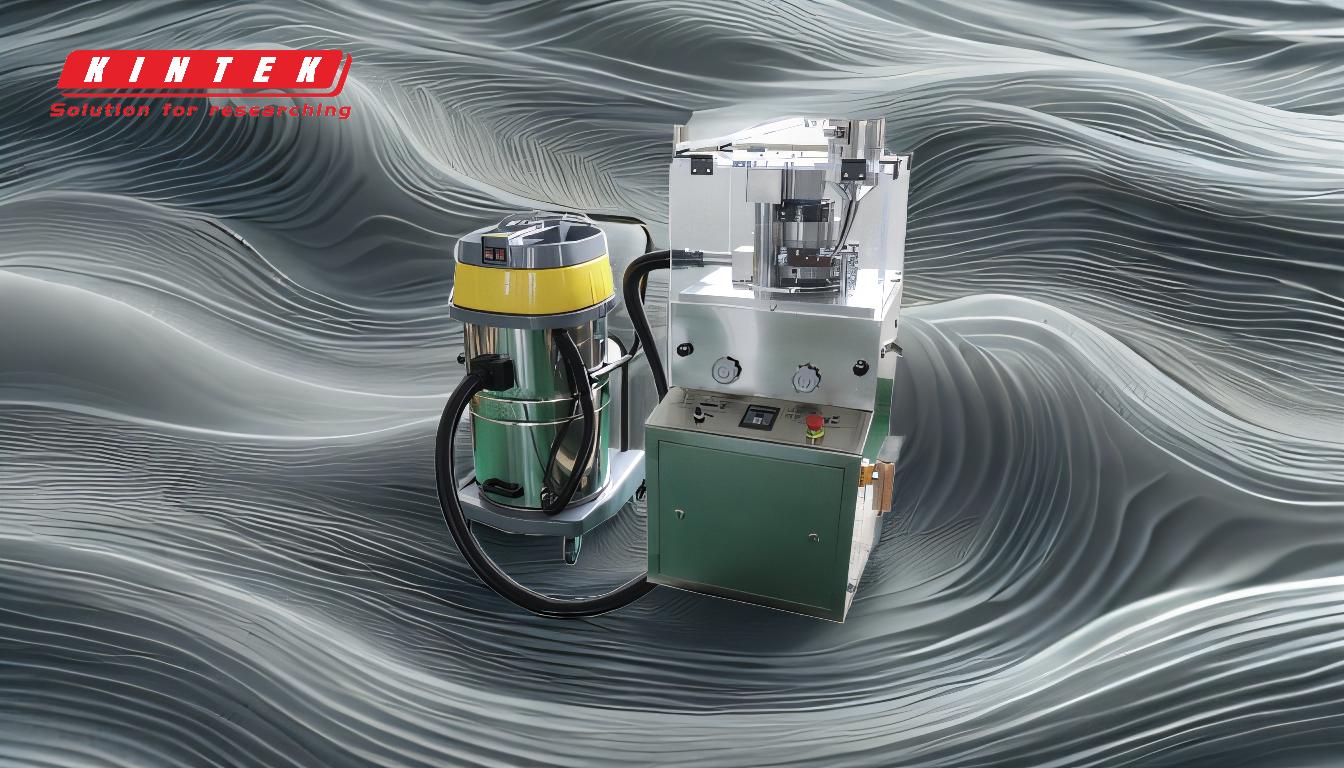
-
Removal of Impurities:
- Calcination effectively removes impurities such as moisture, carbon dioxide, and volatile organic compounds from raw materials.
- For example, in the case of metal ores, calcination helps eliminate unwanted substances like sulfur or arsenic, which can interfere with subsequent processing steps.
-
Decomposition of Compounds:
- During calcination, compounds such as carbonates, hydroxides, and sulfates decompose into simpler oxides or other stable compounds.
- For instance, calcium carbonate (CaCO₃) decomposes into calcium oxide (CaO) and carbon dioxide (CO₂) when heated.
-
Formation of Oxides:
- One of the primary outcomes of calcination is the conversion of metal carbonates or hydroxides into their respective oxides.
- This is particularly important in metallurgy, where metal oxides are often the desired intermediate products for further reduction to pure metals.
-
Thermal Stability Enhancement:
- Calcination increases the thermal stability of materials by removing volatile components that could otherwise degrade or decompose at high temperatures.
- This makes the material more suitable for high-temperature applications, such as in the production of ceramics or refractory materials.
-
Physical and Chemical Changes:
- Calcination induces significant physical and chemical changes in the material, including changes in crystal structure, porosity, and surface area.
- These changes can enhance the reactivity or suitability of the material for specific industrial applications.
-
Applications in Various Industries:
- Metallurgy: Calcination is used to prepare metal ores for smelting by removing impurities and converting carbonates to oxides.
- Ceramics: It helps in the production of ceramic materials by decomposing raw materials and enhancing their thermal properties.
- Chemical Industry: Calcination is employed to produce various chemical compounds, such as lime (CaO) from limestone (CaCO₃).
-
Comparison with Sintering:
- While calcination focuses on the removal of impurities and decomposition of compounds, sintering involves the welding or bonding of small particles to form a cohesive mass.
- Sintering typically occurs at higher temperatures and is used to create solid materials from powders, such as in the production of metal parts or ceramics.
In summary, calcination is a critical process that results in the purification, decomposition, and transformation of materials, making them more suitable for industrial applications. It plays a vital role in metallurgy, ceramics, and chemical production by enhancing the properties and usability of raw materials.
Summary Table:
Key Aspect | Description |
---|---|
Removal of Impurities | Eliminates moisture, CO₂, and volatile compounds, purifying raw materials. |
Decomposition of Compounds | Breaks down carbonates, hydroxides, and sulfates into simpler oxides. |
Formation of Oxides | Converts metal carbonates/hydroxides into oxides, crucial for metallurgy. |
Thermal Stability | Enhances material stability by removing volatile components. |
Physical/Chemical Changes | Alters crystal structure, porosity, and surface area for better reactivity. |
Applications | Used in metallurgy, ceramics, and chemical industries for material preparation. |
Comparison with Sintering | Focuses on impurity removal, unlike sintering, which bonds particles. |
Discover how calcination can optimize your industrial processes—contact our experts today!