Chemical Vapor Deposition (CVD) is a sophisticated manufacturing process used to deposit thin films of materials onto a substrate. The process involves several stages, starting from the introduction of precursor gases into a reaction chamber, followed by their transportation, adsorption, and reaction on the substrate surface, and finally the desorption of by-products. The key steps include the transportation of gaseous precursors, their adsorption onto the substrate, surface reactions leading to film formation, and the removal of reaction by-products. Each stage is crucial for ensuring the quality, uniformity, and stoichiometry of the deposited film.
Key Points Explained:
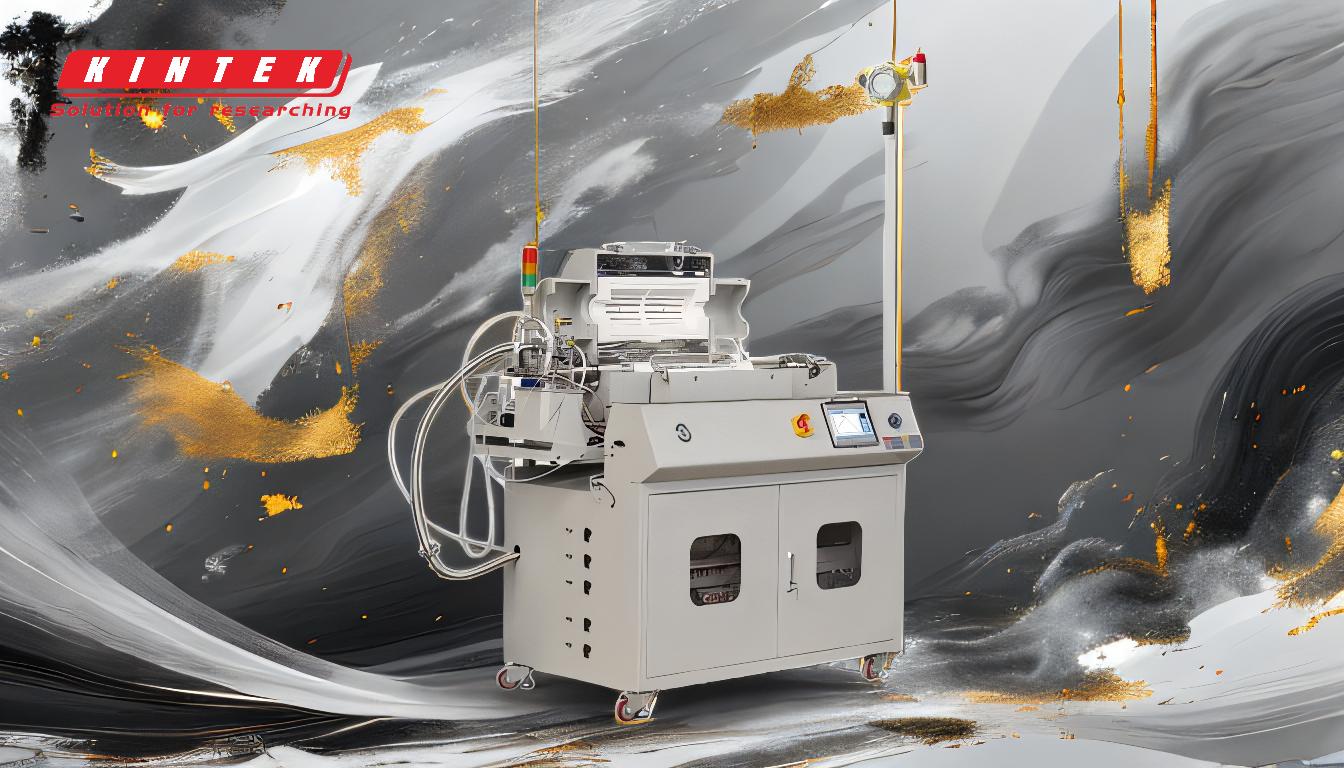
-
Transportation of Precursor Gases into the Chamber:
- The CVD process begins with the introduction of volatile precursor gases into a reaction chamber, typically under vacuum or controlled atmospheric conditions.
- These precursor gases are chosen based on their ability to decompose or react at the desired temperature to form the desired material.
- The gases are transported into the chamber using fluid dynamics principles, ensuring even distribution across the substrate.
-
Adsorption of Precursor Molecules onto the Substrate:
- Once inside the chamber, the precursor molecules diffuse toward the substrate surface.
- Adsorption occurs when these molecules adhere to the substrate surface, facilitated by surface energy and chemical interactions.
- This step is critical as it determines the initial nucleation sites for film growth.
-
Surface-Catalyzed Reactions and Film Formation:
- The adsorbed precursor molecules undergo chemical reactions on the substrate surface, often catalyzed by the surface itself or by external energy sources such as heat or plasma.
- These reactions lead to the decomposition of the precursor molecules, releasing the desired material atoms or molecules that bond to the substrate.
- Over time, these atoms or molecules accumulate, forming a thin film on the substrate.
-
Nucleation and Growth of the Film:
- Nucleation refers to the initial formation of small clusters of the deposited material on the substrate.
- These clusters grow and coalesce, forming a continuous film.
- The growth rate and film quality depend on factors such as temperature, pressure, and the reactivity of the precursor gases.
-
Desorption of By-Products and Transportation Away from the Surface:
- As the chemical reactions proceed, by-product molecules are generated and must be removed from the substrate surface to prevent contamination and ensure continuous film growth.
- Desorption involves the release of these by-products from the surface into the gas phase.
- The by-products are then transported out of the chamber, maintaining a clean environment for further deposition.
-
Control of Process Parameters:
- The CVD process requires precise control of parameters such as temperature, pressure, gas flow rates, and reaction time.
- These parameters influence the film's thickness, uniformity, stoichiometry, and overall quality.
- Advanced CVD systems often incorporate real-time monitoring and feedback mechanisms to optimize these parameters.
-
Applications and Advantages of CVD:
- CVD is widely used in industries such as semiconductors, optics, and coatings due to its ability to produce high-quality, uniform films.
- The process allows for the deposition of a wide range of materials, including metals, ceramics, and polymers, with precise control over film properties.
- CVD films are known for their density, stoichiometry, and ability to grow high-quality insulator films, making them suitable for demanding applications.
By understanding and optimizing each stage of the CVD process, manufacturers can achieve high-performance coatings and films tailored to specific applications.
Summary Table:
Stage | Description |
---|---|
1. Transportation of Gases | Precursor gases are introduced into the chamber for even distribution. |
2. Adsorption | Molecules adhere to the substrate, forming nucleation sites for film growth. |
3. Surface Reactions | Chemical reactions on the substrate lead to film formation. |
4. Nucleation & Growth | Clusters grow and coalesce, forming a continuous film. |
5. Desorption of By-Products | By-products are removed to maintain a clean environment for further deposition. |
6. Process Control | Precise control of temperature, pressure, and gas flow ensures film quality. |
7. Applications | Used in semiconductors, optics, and coatings for high-quality, uniform films. |
Discover how CVD can enhance your manufacturing process—contact us today for expert guidance!