Melting metal is a fundamental process in metallurgy and manufacturing, involving the transformation of solid metal into a liquid state by heating it above its melting point. This process is critical for casting, alloying, and shaping metals into desired forms. The stages of melting metal include preparation, heating, melting, and post-melting treatment. Each stage requires precise control of temperature, environment, and equipment to ensure the quality and properties of the molten metal. Understanding these stages is essential for optimizing the melting process and achieving the desired outcomes in metalworking.
Key Points Explained:
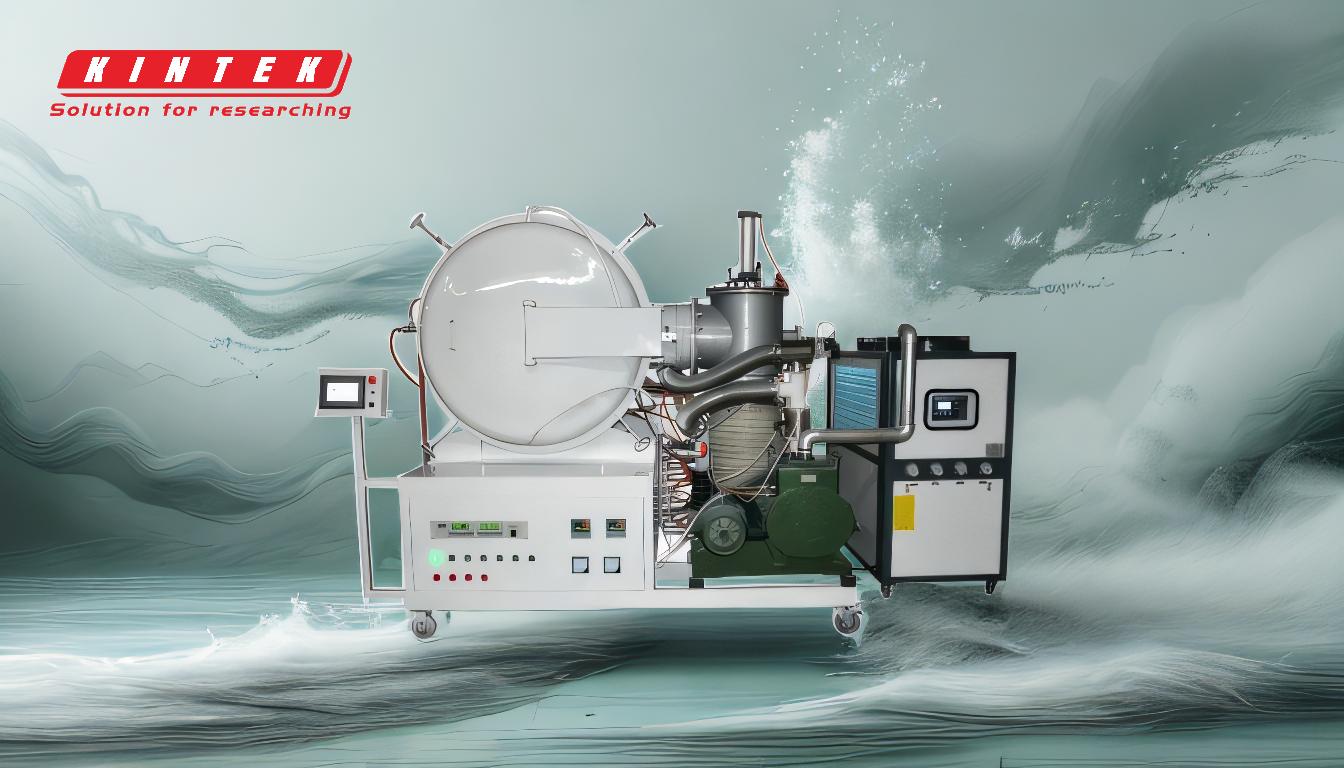
-
Preparation Stage:
- Cleaning and Sorting: Before melting, the metal must be cleaned to remove impurities such as dirt, oil, or oxidation layers. Sorting ensures that only the desired metal or alloy is melted, preventing contamination.
- Preheating: Some metals may require preheating to remove moisture or to bring them closer to the melting temperature, reducing the energy required for the main heating stage.
-
Heating Stage:
- Furnace Selection: The type of furnace used depends on the metal being melted, the required temperature, and the scale of operation. Common furnaces include induction furnaces, arc furnaces, and crucible furnaces.
- Temperature Control: Precise temperature control is crucial to avoid overheating, which can degrade the metal's properties, or underheating, which may result in incomplete melting.
-
Melting Stage:
- Transition to Liquid State: As the metal reaches its melting point, it transitions from a solid to a liquid state. This phase change requires careful monitoring to ensure uniform melting.
- Stirring and Mixing: In some cases, stirring or mixing is necessary to ensure homogeneity, especially when melting alloys or when additives are introduced to modify the metal's properties.
-
Post-Melting Treatment:
- Degassing and Refining: Molten metal may contain dissolved gases or impurities that need to be removed. Degassing processes, such as vacuum degassing or fluxing, are used to eliminate these contaminants.
- Temperature Adjustment: After melting, the temperature of the molten metal may need to be adjusted to suit the subsequent casting or forming process.
- Pouring and Casting: The molten metal is poured into molds or prepared for further processing. Proper pouring techniques are essential to avoid defects such as porosity or inclusions.
-
Safety and Environmental Considerations:
- Ventilation and Fume Extraction: Melting metals can release harmful fumes and gases. Proper ventilation and fume extraction systems are necessary to protect workers and the environment.
- Energy Efficiency: Optimizing the melting process for energy efficiency not only reduces costs but also minimizes the environmental impact.
By understanding and carefully managing each stage of the metal melting process, manufacturers can achieve high-quality molten metal suitable for a wide range of applications. This structured approach ensures that the metal's properties are preserved or enhanced, leading to better performance in its final form.
Summary Table:
Stage | Key Activities |
---|---|
Preparation | Cleaning, sorting, and preheating metals to remove impurities and moisture. |
Heating | Selecting the right furnace and maintaining precise temperature control. |
Melting | Transitioning metal to liquid state and ensuring uniform melting with stirring. |
Post-Melting | Degassing, refining, temperature adjustment, and proper pouring techniques. |
Safety & Environment | Ventilation, fume extraction, and energy efficiency measures. |
Optimize your metal melting process today—contact our experts for tailored solutions!