The process of operating a filter press involves several systematic steps to ensure efficient filtration and separation of solids from liquids. It begins with the preparation of the slurry and the filter press, followed by filling the press, monitoring the filtration process, and concluding with the removal of the filter cake and evaluation of the results. Each step is critical to achieving optimal performance and obtaining accurate results. Below, the key steps are explained in detail to provide a comprehensive understanding of the filter press operation.
Key Points Explained:
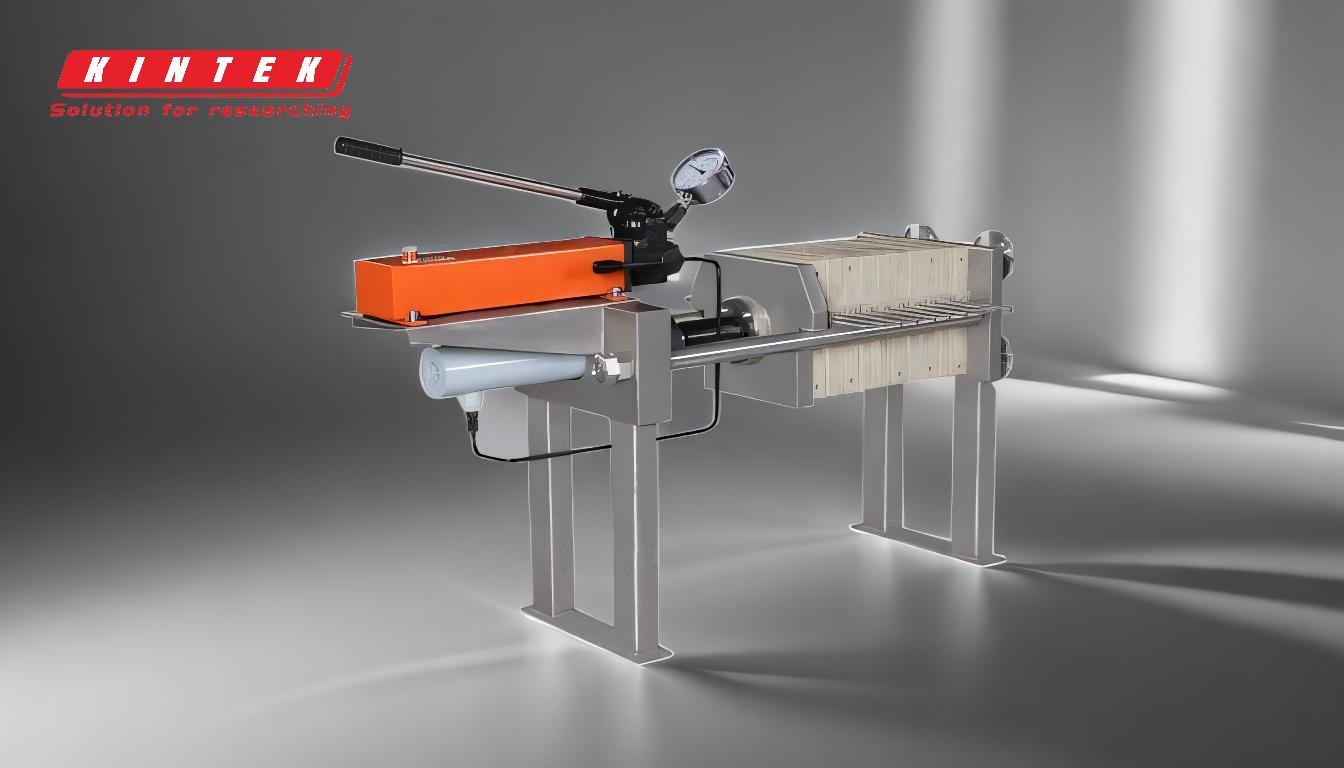
-
Preparation of Slurry and Filter Press
- The process begins by preparing the slurry, which is the mixture of solid particles and liquid to be separated.
- The filter press is prepared by installing the appropriate plates and filter cloth. The choice of plates (e.g., recessed chamber or membrane plates) and filter cloth depends on the specific application and the nature of the slurry.
- Proper preparation ensures that the filter press is ready to handle the slurry efficiently and achieve the desired separation.
-
Filling the Filter Press
- Once the press is prepared, the pump is turned on to fill the press with the slurry.
- The slurry is pumped into the chambers formed by the filter plates, where the solid particles are trapped by the filter cloth, and the liquid (filtrate) passes through.
- Filtrate samples may be taken during this stage to monitor the quality and clarity of the liquid.
-
Filtration Process
- The filtration continues until low flow and maximum pressure conditions are reached. These conditions indicate that the chambers are full of solid particles, and further filtration is no longer efficient.
- For a recessed chamber filter press, the process typically ends at this stage. However, for a membrane filter press, additional steps such as cake wash, membrane squeeze, and optional air blowdown may be performed to further dewater the filter cake.
-
Optional Steps for Membrane Filter Press
- Cake Wash: If required, the filter cake can be washed to remove any residual impurities or contaminants.
- Membrane Squeeze: The membranes are inflated to apply additional pressure on the filter cake, reducing its moisture content.
- Air Blowdown: Compressed air may be used to further dry the filter cake by displacing any remaining liquid.
-
Opening the Filter Press and Removing the Filter Cake
- After the filtration process is complete, the filter press is opened, and the filter cake is removed.
- The filter cake is the solid material that has been separated from the liquid. Samples of the filter cake may be taken for further analysis.
-
Evaluation and Observations
- Observations are made on the condition of the filter cloth and the ease of cake release. These observations help in assessing the performance of the filtration process and identifying any issues with the filter cloth or plates.
- The results of the filtration process, including the quality of the filtrate and the filter cake, are evaluated to determine the success of the operation.
-
Maintenance and Cleaning
- After the test, the filter press is cleaned and maintained to ensure its readiness for the next operation. This includes inspecting and replacing the filter cloth if necessary, as well as checking the condition of the plates and other components.
By following these steps, a filter press can effectively separate solids from liquids, making it a valuable tool in various industries such as wastewater treatment, mining, and chemical processing. For applications requiring precise analysis, such as preparing samples for FTIR spectroscopy, specialized equipment like an FTIR press may be used in conjunction with the filter press to ensure high-quality results.
Summary Table:
Step | Description |
---|---|
1. Preparation | Prepare the slurry and install appropriate filter plates and cloth. |
2. Filling | Pump slurry into the filter press chambers for separation. |
3. Filtration | Monitor until low flow and maximum pressure are reached. |
4. Optional Steps | Perform cake wash, membrane squeeze, and air blowdown (for membrane presses). |
5. Cake Removal | Open the press and remove the filter cake for analysis. |
6. Evaluation | Assess filter cloth condition, cake release, and results. |
7. Maintenance | Clean and inspect the press for the next operation. |
Need help optimizing your filtration process? Contact our experts today for tailored solutions!