The powder metallurgy process is a manufacturing method used to produce metal parts and components from powdered materials. It involves four fundamental steps: powder preparation, mixing and blending, compacting, and sintering. Each step plays a critical role in shaping the final product, ensuring it meets the desired specifications in terms of strength, density, and dimensional accuracy. This process is widely used in industries such as automotive, aerospace, and electronics due to its ability to produce complex shapes with minimal material waste. Below, we will explore each step in detail to understand its significance and how it contributes to the overall process.
Key Points Explained:
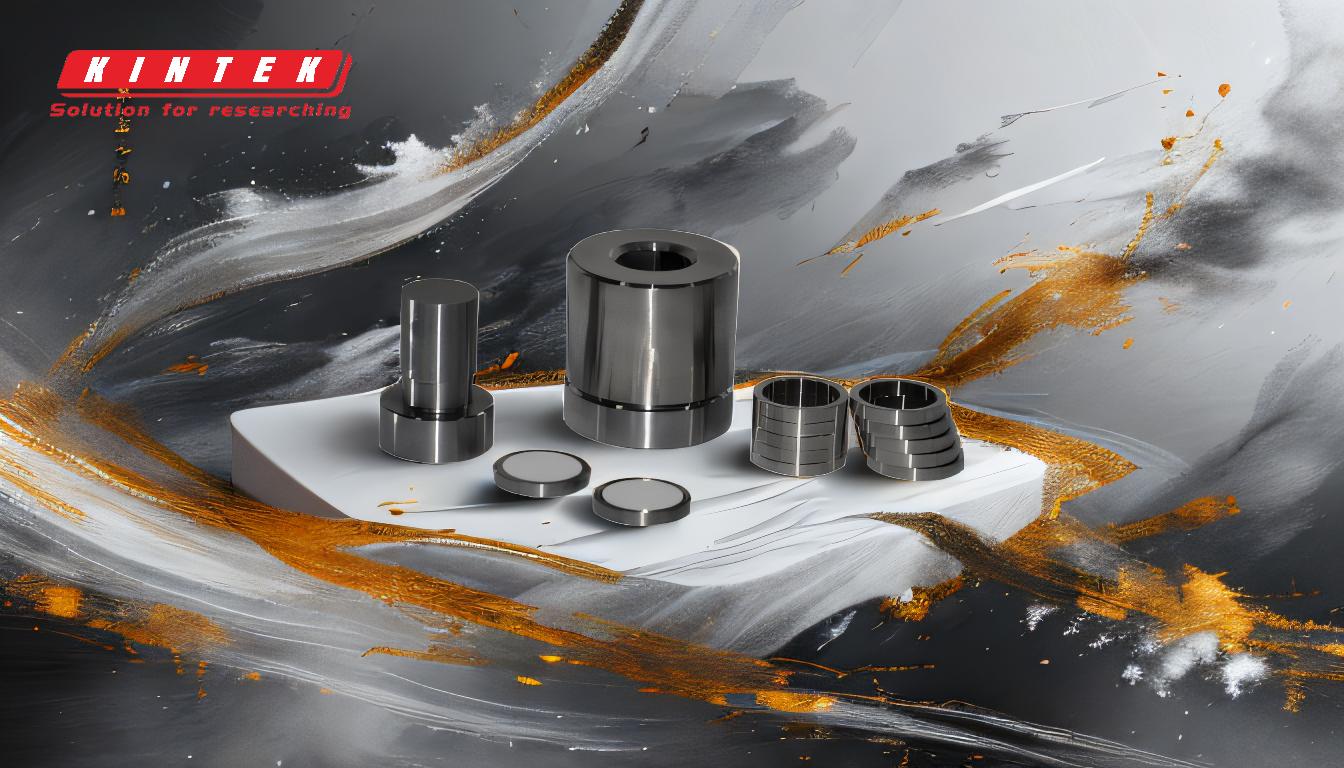
-
Powder Preparation
- Powder preparation is the first step in the powder metallurgy process. It involves the production of metal powders, which can be achieved through various methods such as atomization, chemical reduction, or mechanical processes.
- The quality of the powder is crucial, as it directly affects the properties of the final product. Powders must have consistent particle size, shape, and composition to ensure uniformity during subsequent steps.
- Common metals used in powder metallurgy include iron, copper, aluminum, and titanium, as well as alloys like stainless steel and bronze.
-
Mixing and Blending
- After powder preparation, the next step is mixing and blending. This involves combining different metal powders or adding lubricants and binders to improve the flowability and compressibility of the powder mixture.
- Lubricants are added to reduce friction during compaction, while binders help hold the powder particles together after compaction.
- The goal of this step is to achieve a homogeneous mixture, ensuring that the final product has uniform properties and consistent performance.
-
Compacting
- Compacting is the process of applying intense pressure to the powder mixture to form a "green compact," which is a shaped but unsintered part. This step is typically performed using a hydraulic or mechanical press and a die.
- The pressure applied during compaction ranges from 100 to 1,000 MPa, depending on the material and desired density of the final product.
- The green compact retains the shape of the die but is relatively fragile and requires careful handling.
-
Sintering
- Sintering is the final and most critical step in the powder metallurgy process. It involves heating the green compact in a controlled atmosphere (e.g., vacuum, hydrogen, or inert gas) at a temperature below the melting point of the metal.
- The sintering temperature typically ranges from 70% to 90% of the metal's melting point. For example, iron is sintered at around 1,100°C to 1,300°C.
- During sintering, the powder particles bond together through diffusion, resulting in a denser and stronger final product. This step also helps eliminate any remaining lubricants or binders.
By following these four steps, the powder metallurgy process can produce high-quality metal parts with precise dimensions, excellent mechanical properties, and minimal material waste. This method is particularly advantageous for manufacturing complex shapes and components that would be difficult or costly to produce using traditional methods.
Summary Table:
Step | Description | Key Details |
---|---|---|
Powder Preparation | Production of metal powders using methods like atomization, chemical reduction, or mechanical processes. | - Consistent particle size, shape, and composition. - Metals: iron, copper, aluminum, titanium, stainless steel, bronze. |
Mixing and Blending | Combining powders with lubricants and binders for improved flowability and compressibility. | - Homogeneous mixture ensures uniform properties. - Lubricants reduce friction; binders hold particles together. |
Compacting | Applying pressure (100–1,000 MPa) to form a 'green compact' using a hydraulic or mechanical press. | - Green compact is shaped but fragile. - Retains die shape, requires careful handling. |
Sintering | Heating the green compact in a controlled atmosphere below the metal's melting point. | - Temperature: 70–90% of melting point. - Bonds particles, increases density, and removes binders. |
Ready to optimize your metal part production? Contact us today to learn more about powder metallurgy solutions!