Physical Vapor Deposition (PVD) is a versatile and widely used technique for depositing thin films of materials onto substrates. The process involves transforming a material from a condensed phase to a vapor phase and then back to a condensed phase on the substrate. The most common PVD methods include sputtering and evaporation. The process typically consists of four main steps: evaporation, transportation, reaction, and deposition. Each step is crucial in ensuring the quality and properties of the final coating. PVD is favored for its ability to deposit a wide range of materials, including inorganic and some organic materials, with improved properties compared to the substrate. Additionally, PVD is considered more environmentally friendly than other coating methods like electroplating.
Key Points Explained:
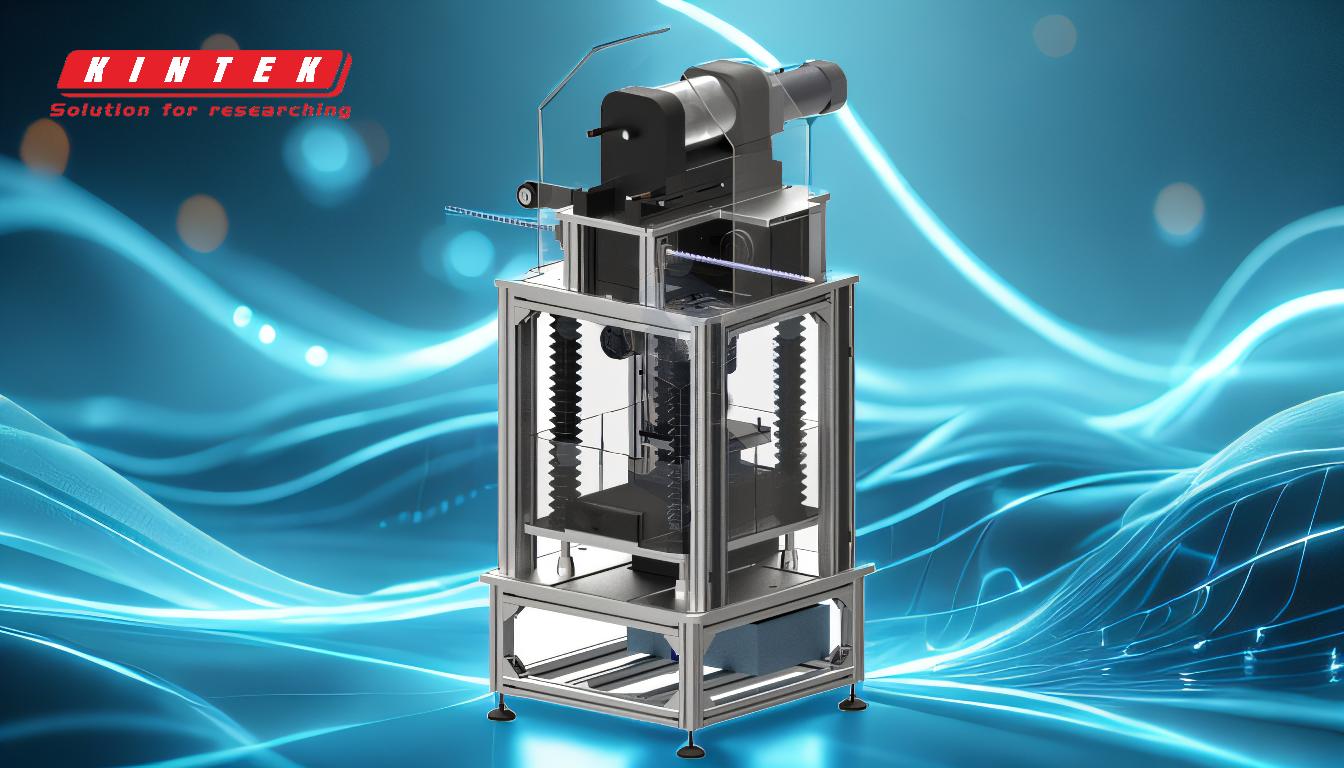
-
Evaporation:
- In this initial step, the target material is bombarded by a high-energy source, such as an ion beam or laser pulses, to dislodge atoms from the target. This process is known as sputtering. The high-energy source causes the target material to vaporize, forming a cloud of vaporized atoms.
- The sputtering rate is a critical parameter that influences the growth rate and quality of the deposited films. Higher sputtering rates generally lead to faster deposition but must be carefully controlled to ensure film quality.
-
Transportation:
- Once the target material has been vaporized, the vaporized atoms are transported through a vacuum chamber to the substrate. The vacuum environment is essential to prevent contamination and ensure that the vaporized atoms can travel unimpeded to the substrate.
- The transportation phase is influenced by the vacuum conditions, including pressure and temperature, which must be optimized to achieve uniform deposition.
-
Reaction:
- During the transportation phase, the vaporized atoms may react with gases introduced into the vacuum chamber. These reactions can form compounds such as oxides or nitrides, depending on the gases used. For example, introducing oxygen can lead to the formation of metal oxide coatings.
- The reaction step allows for the creation of coatings with specific chemical compositions and properties, enhancing the functionality of the final product.
-
Deposition:
- In the final step, the vaporized atoms or reaction products condense onto the substrate, forming a thin film. The deposition process is carefully controlled to ensure that the film is uniform and adheres well to the substrate.
- The properties of the deposited film, such as thickness, uniformity, and adhesion, are critical to the performance of the coated product. Parameters such as substrate temperature, deposition rate, and vacuum conditions are adjusted to achieve the desired film properties.
-
Advantages of PVD:
- Material Versatility: PVD can deposit almost any type of inorganic material and some organic materials, allowing for a wide range of applications.
- Improved Properties: The coatings produced by PVD often have superior properties, such as increased hardness, wear resistance, and corrosion resistance, compared to the substrate material.
- Environmental Friendliness: PVD is considered more environmentally friendly than other coating methods like electroplating, as it typically involves fewer hazardous chemicals and produces less waste.
-
Common PVD Methods:
- Sputtering: This method uses an accelerated plasma to bombard the target material, causing it to sputter and form a vapor. The vaporized atoms are then deposited onto the substrate.
- Thermal Evaporation: In this method, the target material is heated to a high temperature, causing it to evaporate. The vaporized atoms are then transported to the substrate and deposited as a thin film.
- eBeam Evaporation: Similar to thermal evaporation, but uses an electron beam to heat the target material, allowing for higher evaporation rates and better control over the deposition process.
In summary, the PVD process involves a series of well-defined steps that transform a target material into a thin film on a substrate. Each step, from evaporation to deposition, is carefully controlled to ensure the quality and properties of the final coating. The versatility, improved material properties, and environmental benefits of PVD make it a preferred choice for a wide range of applications.
Summary Table:
Step | Description |
---|---|
Evaporation | Target material is vaporized using high-energy sources like ion beams or lasers. |
Transportation | Vaporized atoms travel through a vacuum chamber to the substrate. |
Reaction | Atoms may react with gases to form compounds like oxides or nitrides. |
Deposition | Atoms condense onto the substrate, forming a thin, uniform film. |
Ready to enhance your coatings with PVD? Contact our experts today for tailored solutions!