The process of making a mould involves several critical steps, starting with the design and conceptualization phase, where a 3D model of the part is created. This is followed by selecting the appropriate material for the mould, which is essential for ensuring durability and performance. The subsequent steps include creating the mould design, manufacturing the mould using techniques like CNC machining or 3D printing, and finally, testing and refining the mould to ensure it meets the required specifications. Each step requires careful planning and execution to produce a high-quality mould.
Key Points Explained:
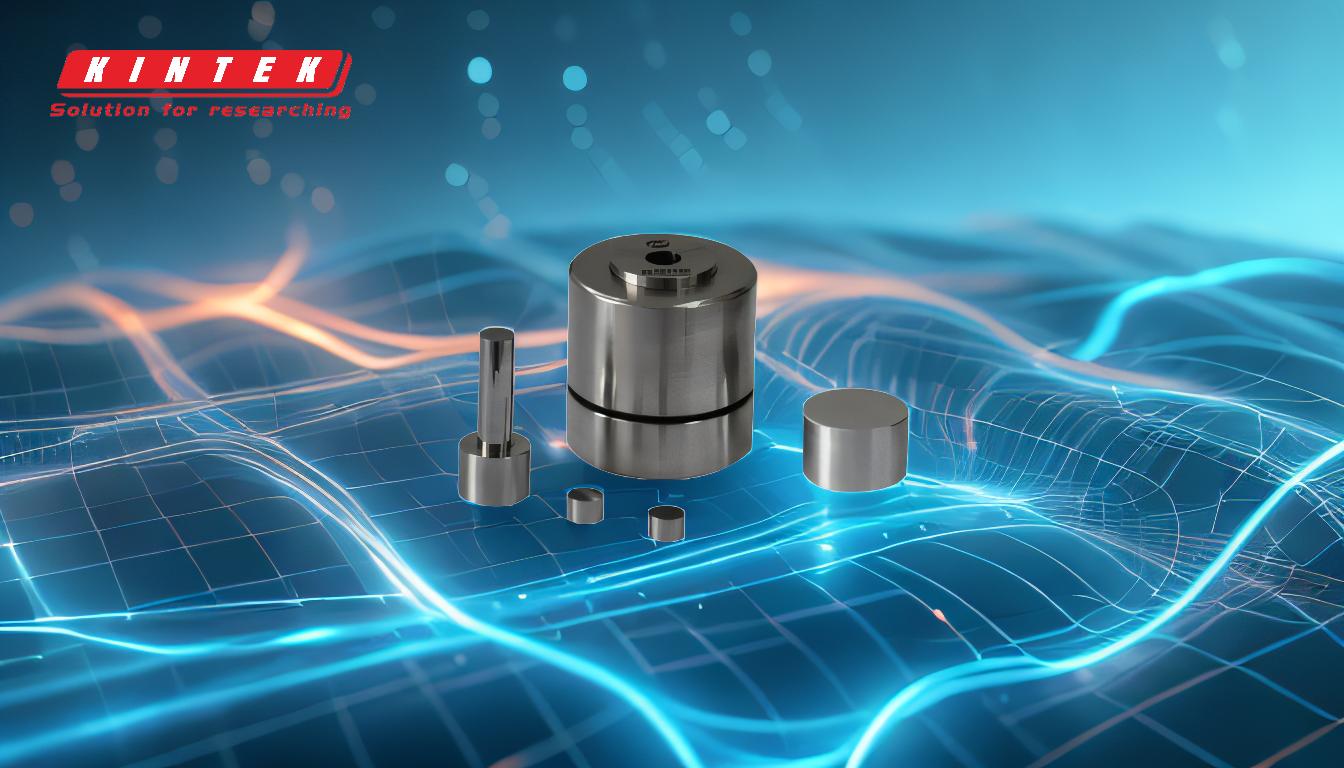
-
Design and Conceptualization:
- Purpose: This phase involves creating a detailed 3D model of the part to be produced. It ensures that the mould will accurately replicate the desired shape and features.
- Process: Engineers and designers use CAD (Computer-Aided Design) software to develop the model, considering factors like part geometry, material flow, and cooling requirements.
- Outcome: A precise blueprint that guides the entire mould-making process.
-
Material Selection:
- Importance: The material used for the mould must withstand the stresses of the manufacturing process, including high temperatures and pressures.
- Criteria: Factors such as thermal conductivity, hardness, and wear resistance are considered. Common materials include steel, aluminum, and composite materials.
- Impact: The right material ensures the mould's longevity and the quality of the final product.
-
Mould Design:
- Details: This step involves translating the 3D model into a mould design, including the creation of cavities, cores, and cooling channels.
- Considerations: Designers must account for part ejection, shrinkage, and potential defects like warping or air traps.
- Tools: Advanced software tools are used to simulate the injection molding process, optimizing the design for efficiency and quality.
-
Mould Manufacturing:
- Techniques: The mould is typically manufactured using CNC machining, EDM (Electrical Discharge Machining), or 3D printing, depending on the complexity and material.
- Precision: High precision is required to ensure that the mould components fit together perfectly and that the final product meets dimensional tolerances.
- Quality Control: Throughout the manufacturing process, rigorous quality checks are performed to detect and correct any deviations from the design.
-
Testing and Refinement:
- Purpose: Once the mould is manufactured, it undergoes testing to ensure it produces parts that meet the required specifications.
- Process: Initial test runs are conducted, and the parts produced are inspected for defects. Adjustments are made to the mould as necessary.
- Finalization: After successful testing, the mould is ready for production, ensuring consistent quality in the manufactured parts.
By following these steps meticulously, manufacturers can create high-quality moulds that are essential for producing precise and reliable components in various industries.
Summary Table:
Step | Key Details |
---|---|
Design & Conceptualization | - Create a 3D model using CAD software. - Consider part geometry, material flow, and cooling. |
Material Selection | - Choose materials like steel or aluminum based on thermal conductivity and durability. |
Mould Design | - Translate 3D model into mould design. - Include cavities, cores, and cooling channels. |
Mould Manufacturing | - Use CNC machining, EDM, or 3D printing. - Ensure precision and quality control. |
Testing & Refinement | - Conduct test runs and inspect parts. - Refine mould to meet specifications. |
Need a high-quality mould for your project? Contact us today to get started!