Chemical Vapor Deposition (CVD) is a widely used technique in materials science and engineering to produce high-quality, high-performance solid materials. The process involves the deposition of a solid material from a gas phase onto a substrate, typically through chemical reactions. The steps of CVD can be broken down into several key stages, each of which plays a crucial role in the overall process. These stages include the transport of reacting gaseous species to the substrate surface, adsorption of these species onto the surface, chemical reactions that lead to the formation of a solid deposit, and the removal of by-products from the surface. The process is highly controllable, allowing for the production of thin films with precise thickness, composition, and properties.
Key Points Explained:
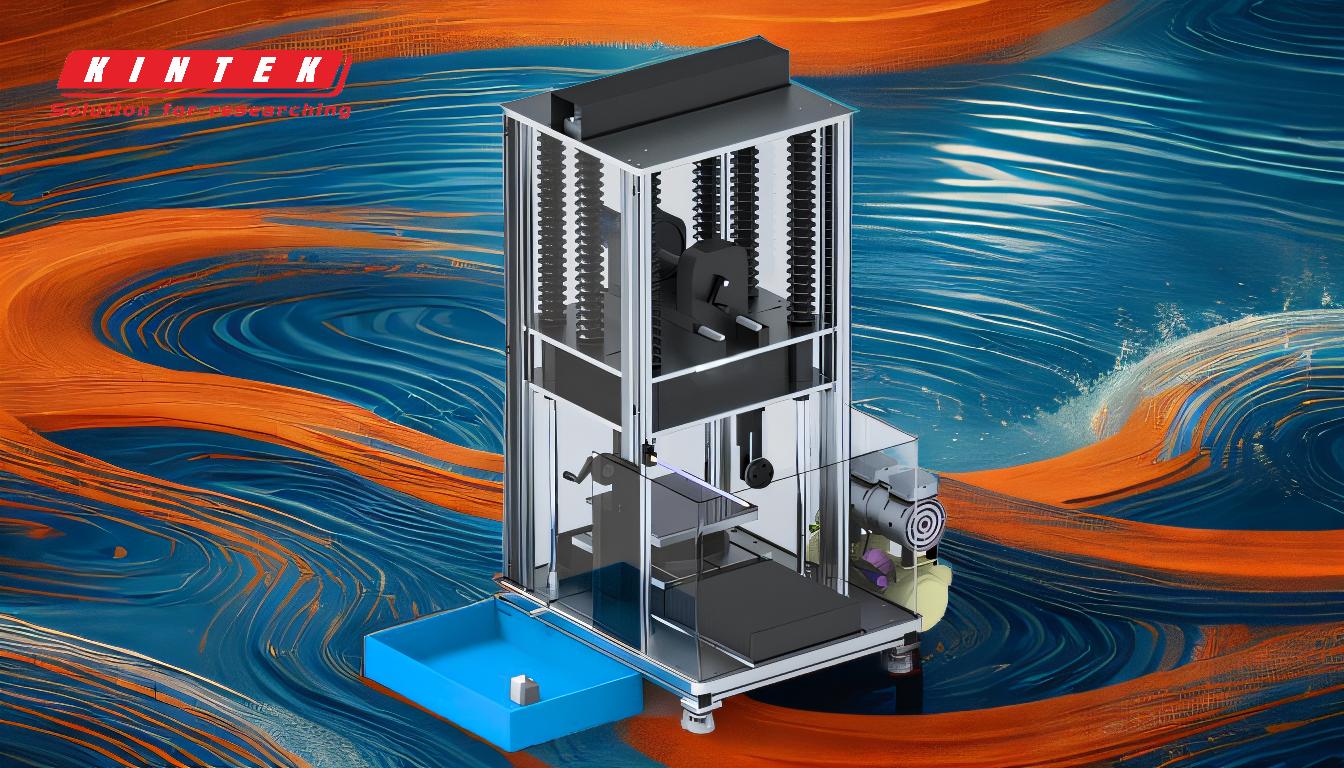
-
Transport of Reacting Gaseous Species to the Surface:
- The first step in the CVD process involves the transport of the gaseous precursors to the substrate surface. These precursors are typically volatile compounds that contain the elements to be deposited. The transport is usually facilitated by a carrier gas, which helps in evenly distributing the precursors over the substrate. The flow rate and concentration of the precursors are carefully controlled to ensure uniform deposition.
-
Adsorption of the Species on the Surface:
- Once the gaseous species reach the substrate surface, they adsorb onto it. Adsorption is the process by which atoms, ions, or molecules from a gas, liquid, or dissolved solid adhere to a surface. In CVD, this step is crucial because it determines how well the precursors will interact with the substrate. The adsorption process can be influenced by factors such as temperature, pressure, and the nature of the substrate surface.
-
Heterogeneous Surface-Catalyzed Reactions:
- After adsorption, the precursors undergo chemical reactions on the substrate surface. These reactions are often catalyzed by the surface itself, which is why they are referred to as heterogeneous reactions. The reactions can involve decomposition of the precursors, reduction, oxidation, or other chemical transformations that lead to the formation of the desired solid material. The reaction conditions, such as temperature and pressure, are optimized to ensure the desired chemical reactions occur efficiently.
-
Surface Diffusion of the Species to Growth Sites:
- Once the chemical reactions have occurred, the resulting atoms or molecules diffuse across the substrate surface to find suitable growth sites. Surface diffusion is a critical step because it influences the uniformity and quality of the deposited film. The diffusion process is affected by the surface temperature and the nature of the substrate material.
-
Nucleation and Growth of the Film:
- Nucleation is the initial stage of film formation, where small clusters of atoms or molecules form on the substrate surface. These clusters then grow into larger islands, which eventually coalesce to form a continuous film. The nucleation and growth processes are influenced by factors such as substrate temperature, precursor concentration, and the presence of impurities. Controlling these factors is essential for producing high-quality films with the desired properties.
-
Desorption of Gaseous Reaction Products and Transportation Away from the Surface:
- As the film grows, gaseous by-products are formed as a result of the chemical reactions. These by-products must be desorbed from the surface and transported away to prevent contamination of the film. The desorption process is typically driven by the vacuum environment in which CVD is performed. Efficient removal of by-products is crucial for maintaining the purity and quality of the deposited film.
-
Types of Chemical Vapor Deposition:
- There are several variations of the CVD process, each tailored to specific applications and materials. Some common types include:
- Aerosol-Assisted Chemical Vapor Deposition (AACVD): This method uses an aerosol to deliver the precursor to the substrate, allowing for the deposition of materials that are difficult to vaporize.
- Direct Liquid Injection (DLI): In DLI, a liquid precursor is injected into a heated chamber, where it vaporizes and reacts to form the desired film.
- Plasma-Enhanced Chemical Vapor Deposition (PECVD): This technique uses plasma to enhance the chemical reactions, allowing for lower deposition temperatures and faster growth rates.
- There are several variations of the CVD process, each tailored to specific applications and materials. Some common types include:
-
Advantages of CVD:
- CVD offers several advantages, including the ability to produce high-quality, dense, and stoichiometric films. The process is highly controllable, allowing for precise management of film thickness and composition. Additionally, CVD can be used to deposit a wide range of materials, including metals, semiconductors, and insulators, making it a versatile technique for various applications.
In summary, the Chemical Vapor Deposition process is a complex but highly effective method for depositing thin films with precise control over their properties. Each step in the process, from the transport of precursors to the removal of by-products, plays a critical role in determining the quality and characteristics of the final film. Understanding and optimizing each of these steps is essential for achieving the desired results in CVD applications.
Summary Table:
Step | Description |
---|---|
1. Transport of Reacting Gaseous Species | Precursors are transported to the substrate surface via a carrier gas. |
2. Adsorption of Species | Gaseous species adsorb onto the substrate surface, influenced by temperature and pressure. |
3. Heterogeneous Surface Reactions | Chemical reactions occur on the surface, forming the desired solid material. |
4. Surface Diffusion | Atoms or molecules diffuse across the surface to growth sites. |
5. Nucleation and Growth | Small clusters form and grow into a continuous film. |
6. Desorption of By-products | Gaseous by-products are removed to maintain film purity. |
7. Types of CVD | Includes AACVD, DLI, and PECVD for specialized applications. |
8. Advantages | Produces high-quality, precise, and versatile thin films. |
Discover how CVD can transform your material science projects—contact our experts today for tailored solutions!