Crucible furnaces are essential in various industrial and laboratory settings for melting metals, ceramics, and other materials. The three primary types of crucible furnaces are resistance furnaces, induction furnaces, and fuel-fired furnaces. Each type has distinct characteristics, advantages, and applications. Resistance furnaces use electric heating elements, induction furnaces rely on electromagnetic induction, and fuel-fired furnaces utilize combustion of fuels like gas or oil. The choice of furnace depends on factors such as the material being melted, required temperature, and operational efficiency. Additionally, the type of crucible used, such as a zirconia crucible, plays a critical role in determining the furnace's performance and suitability for specific applications.
Key Points Explained:
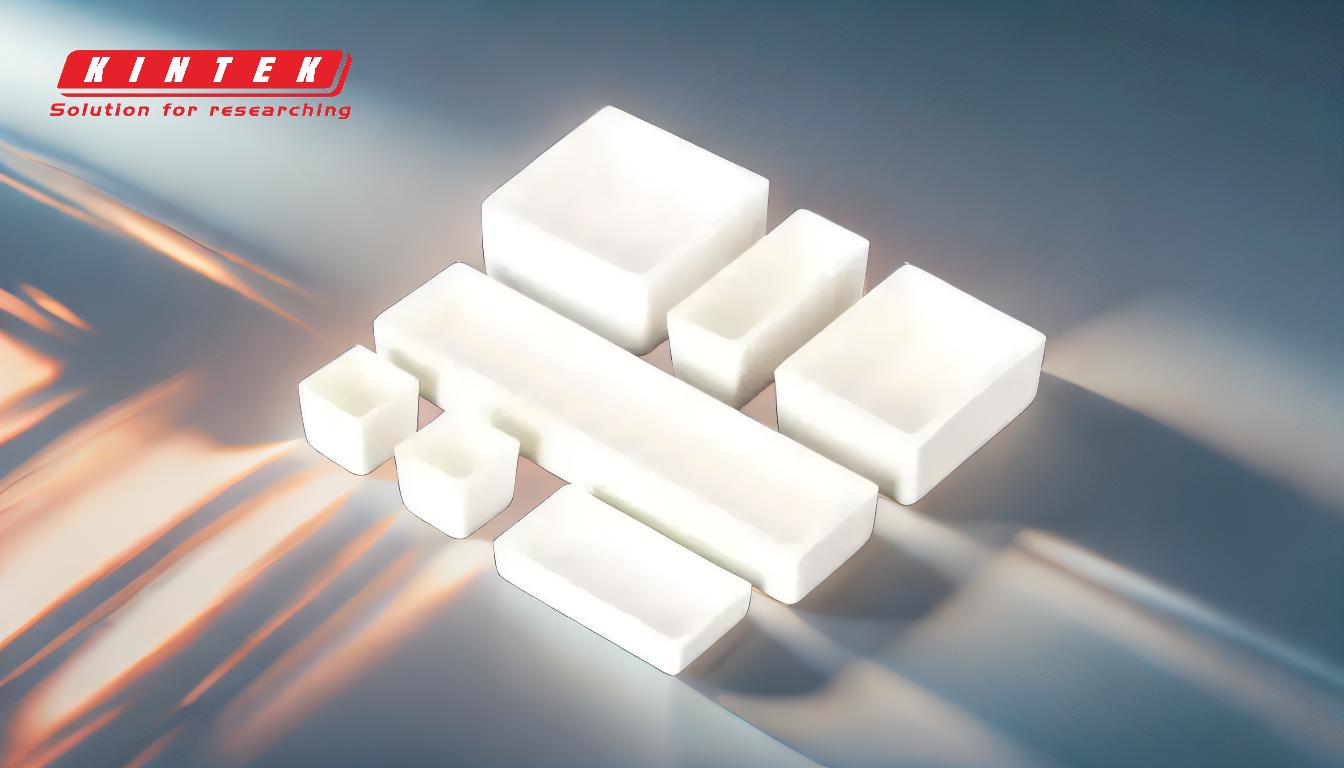
-
Resistance Furnaces
- Description: Resistance furnaces use electric heating elements to generate heat. These elements are typically made of materials like nichrome or silicon carbide, which have high electrical resistance and can withstand high temperatures.
-
Advantages:
- Precise temperature control.
- Uniform heating.
- Suitable for small-scale operations and laboratory use.
-
Applications:
- Melting non-ferrous metals like aluminum and copper.
- Heat treatment processes.
- Laboratory research and testing.
- Crucible Compatibility: Works well with crucibles made of materials like graphite, alumina, or zirconia crucible, depending on the required temperature and chemical resistance.
-
Induction Furnaces
- Description: Induction furnaces use electromagnetic induction to generate heat within the crucible. An alternating current passes through a coil, creating a magnetic field that induces eddy currents in the crucible or the material inside, causing it to heat up.
-
Advantages:
- High energy efficiency.
- Rapid heating.
- Clean operation with minimal contamination.
-
Applications:
- Melting ferrous and non-ferrous metals.
- Foundry operations.
- Alloy production.
- Crucible Compatibility: Typically uses graphite or silicon carbide crucibles, but zirconia crucible can be used for high-temperature applications requiring chemical inertness.
-
Fuel-Fired Furnaces
- Description: Fuel-fired furnaces rely on the combustion of fuels such as natural gas, propane, or oil to generate heat. The heat is transferred to the crucible through convection or radiation.
-
Advantages:
- High-temperature capability.
- Cost-effective for large-scale operations.
- Versatile in terms of fuel options.
-
Applications:
- Melting metals like steel and cast iron.
- Glass and ceramic production.
- Large-scale industrial processes.
- Crucible Compatibility: Often uses crucibles made of refractory materials like alumina, silicon carbide, or zirconia crucible for high-temperature and corrosive environments.
-
Importance of Crucible Material
- The choice of crucible material is critical for the performance and longevity of the furnace.
- Zirconia Crucible: Known for its exceptional thermal stability, chemical resistance, and ability to withstand extreme temperatures, making it ideal for high-temperature applications and corrosive environments.
- Other materials like graphite, alumina, and silicon carbide are also commonly used, depending on the specific requirements of the application.
-
Factors Influencing Furnace Selection
- Material to be Melted: Different materials require different melting temperatures and crucible materials.
- Scale of Operation: Small-scale operations may prefer resistance furnaces, while large-scale industries may opt for fuel-fired or induction furnaces.
- Energy Efficiency: Induction furnaces are highly energy-efficient, while fuel-fired furnaces may be more cost-effective for large-scale operations.
- Temperature Requirements: High-temperature applications may require specialized crucibles like zirconia crucible and specific furnace types.
By understanding the characteristics and applications of each type of crucible furnace, users can make informed decisions based on their specific needs. The choice of crucible, such as a zirconia crucible, further enhances the furnace's performance and suitability for demanding applications.
Summary Table:
Type | Description | Advantages | Applications | Crucible Compatibility |
---|---|---|---|---|
Resistance Furnaces | Uses electric heating elements for precise temperature control. | - Precise temperature control. - Uniform heating. - Small-scale use. |
- Melting non-ferrous metals. - Heat treatment. - Laboratory research. |
Graphite, alumina, zirconia crucible. |
Induction Furnaces | Uses electromagnetic induction for rapid, energy-efficient heating. | - High energy efficiency. - Rapid heating. - Minimal contamination. |
- Melting ferrous/non-ferrous metals. - Foundry operations. - Alloys. |
Graphite, silicon carbide, zirconia crucible. |
Fuel-Fired Furnaces | Relies on combustion of fuels like gas or oil for high-temperature operations. | - High-temperature capability. - Cost-effective for large-scale use. |
- Melting steel/cast iron. - Glass/ceramic production. - Industrial use. |
Alumina, silicon carbide, zirconia crucible. |
Need help choosing the right crucible furnace? Contact our experts today for personalized advice!