Tempering is a critical heat treatment process used to enhance the mechanical properties of quench-hardened or normalized ferrous alloys. By heating the material to a temperature below its transformation range and then cooling it, tempering reduces brittleness, relieves internal stresses, and improves ductility and toughness. The process results in the formation of specific microstructures, such as troostite (formed at 300-750°F) or sorbite (formed at 750-1290°F), which directly influence the steel's strength and ductility. The three primary types of tempering—low, medium, and high—are distinguished by the temperature ranges used and the resulting material properties.
Key Points Explained:
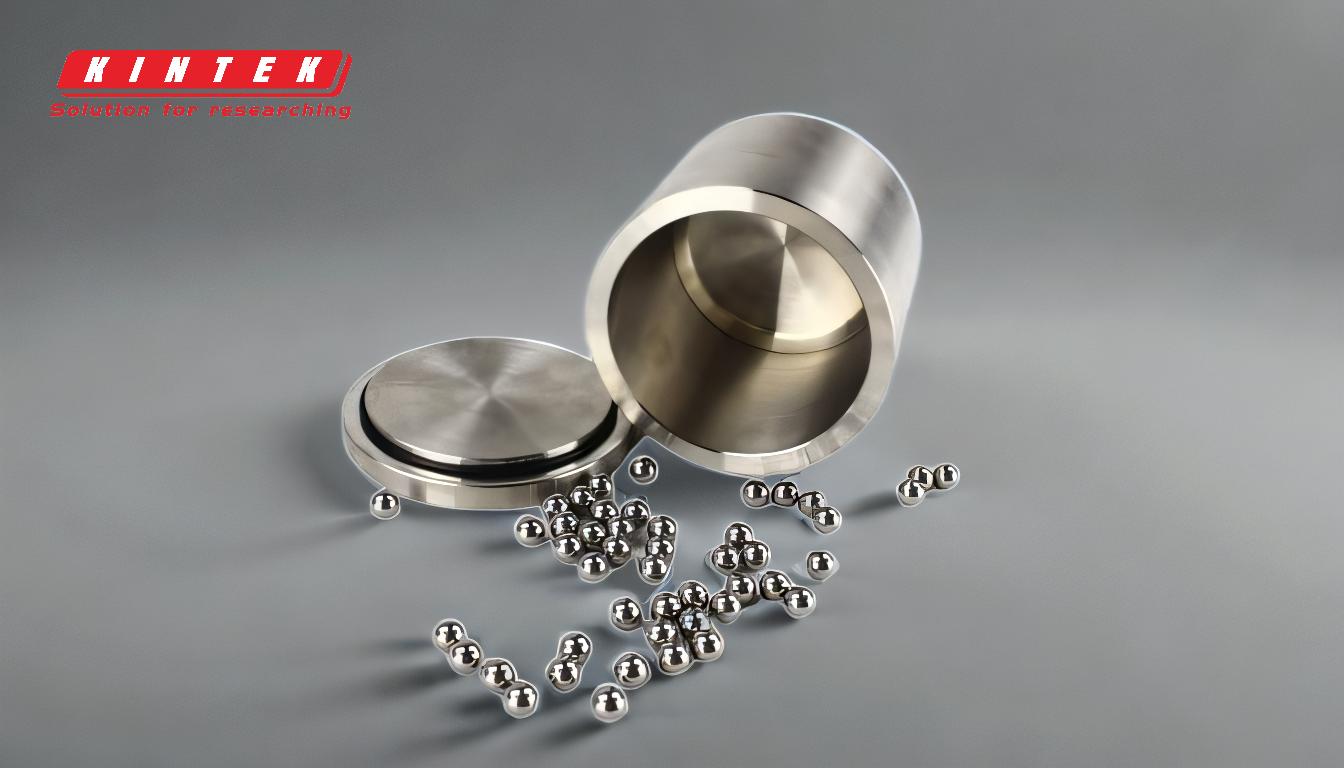
-
Purpose of Tempering:
- Tempering is performed to reduce brittleness in hardened steel, making it more ductile and less prone to cracking.
- It relieves internal stresses caused by rapid cooling during quenching, ensuring dimensional stability and improved mechanical performance.
-
Temperature Ranges and Microstructures:
- Low Tempering (300-750°F): Forms troostite, a fine microstructure that provides a balance between hardness and toughness. This range is ideal for applications requiring high surface hardness with moderate ductility.
- Medium Tempering (750-1290°F): Produces sorbite, a coarser microstructure that offers increased ductility and toughness while retaining sufficient strength. This range is suitable for components subjected to moderate stress.
- High Tempering (above 1290°F): Results in a coarse microstructure with maximum ductility and toughness but reduced hardness. This range is used for components requiring high impact resistance and flexibility.
-
Applications of Tempering Types:
- Low Tempering: Commonly used for cutting tools, dies, and bearings where surface hardness is critical.
- Medium Tempering: Applied to structural components like springs, gears, and axles that need a balance of strength and toughness.
- High Tempering: Suitable for heavy-duty machinery parts, such as crankshafts and connecting rods, which require high impact resistance.
-
Cooling Methods:
- After heating, the steel is typically cooled in air or oil, depending on the desired properties and the specific alloy. Controlled cooling ensures the formation of the desired microstructure and prevents the reintroduction of internal stresses.
By understanding the three types of tempering and their respective temperature ranges, manufacturers can tailor the heat treatment process to achieve the optimal combination of hardness, strength, and ductility for specific applications. This knowledge is essential for equipment and consumable purchasers to select materials that meet performance requirements and ensure long-term reliability.
Summary Table:
Tempering Type | Temperature Range | Microstructure | Key Properties | Applications |
---|---|---|---|---|
Low Tempering | 300-750°F | Troostite | High hardness, moderate ductility | Cutting tools, dies, bearings |
Medium Tempering | 750-1290°F | Sorbite | Balanced strength and toughness | Springs, gears, axles |
High Tempering | Above 1290°F | Coarse microstructure | Maximum ductility and toughness | Crankshafts, connecting rods |
Need help selecting the right tempering process for your materials? Contact our experts today for tailored solutions!